filmov
tv
TangerineTiger15 Is Ordinary Engraving another disappoinment
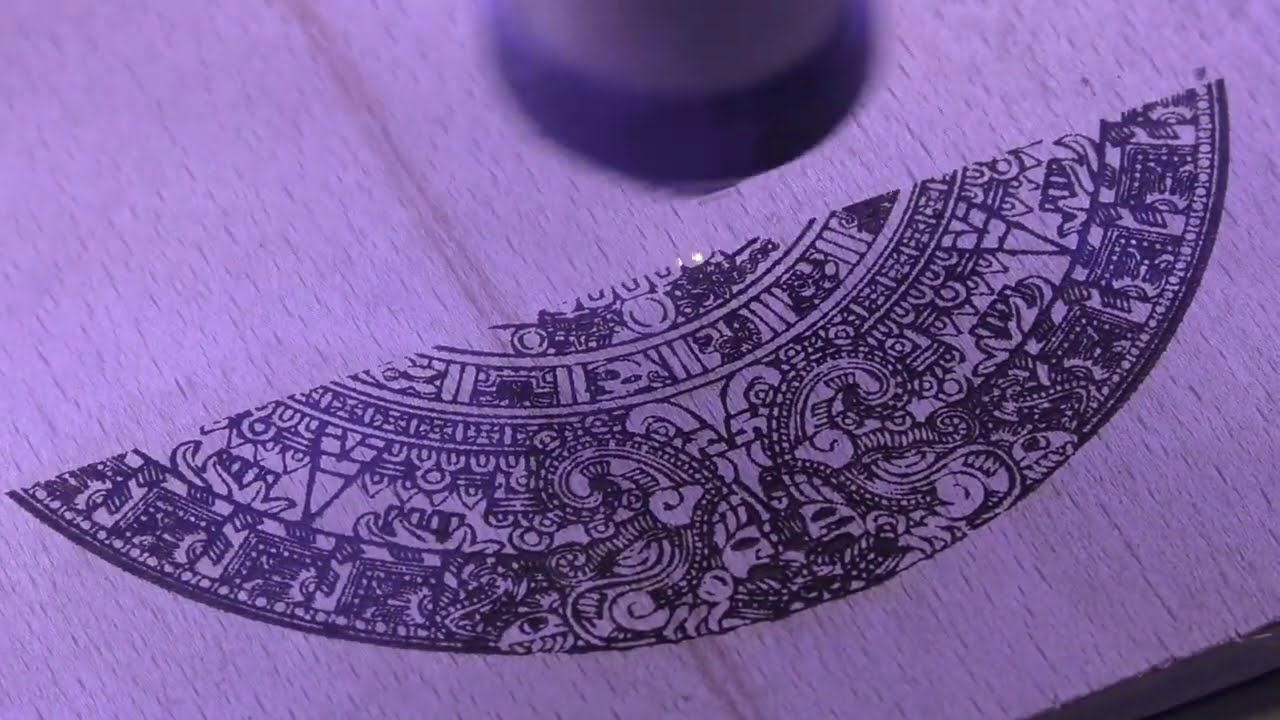
Показать описание
Ordinary engraving is one of the areas where the almost instant switching capability of this technology should excel. In this session we explore the superficial properties of this high speed engraving capability. However, with only 20 watts of burning power , just how fast will that allow us to go. We know this machine is currently capable of at least 1400mm/s but does that mean faster cycle times? Caution...... there may be two limiting factors that will prevent this speed being usable. First is POWER, Just how thinly can I spread 20 watts and get acceptable results? Second is ACCELERATION.,The faster the linear speed, the longer it takes to accelerate and decelerate. We have already seen how this second factor can have a HUGE effect on cycle time . Hence, the headline speed capability of a machine maybe impressive but without sufficient watts and motor power that number may be meaningless
Комментарии