filmov
tv
Ep 3 - BoB1 - It's a learning curve. - Ben Crowe Builds an Insane Guitar
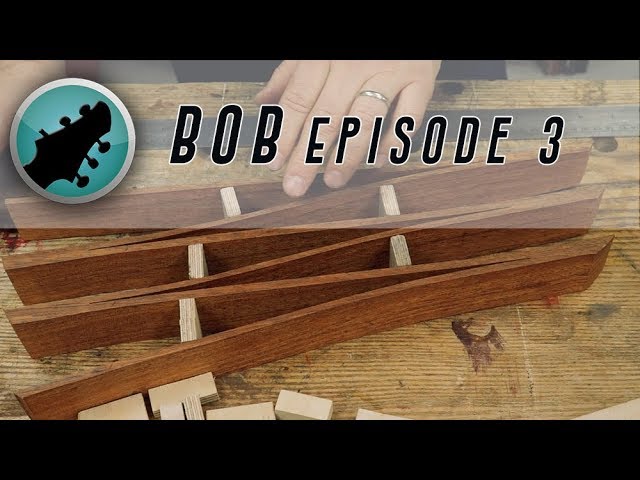
Показать описание
#guitardesign #guitarbuilder #guitarbuilding #guitar #luthier
In this episode, Ben reduces the size of the neck blank and finalises the neck. Experiments with the slices of wood that will make up the body - unsuccessfully.
Chapters
0:00 Introduction
1:05 Marking out and cutting the neck and headstock
5:15 Slicing the offcuts - do they bend?
6:42 It works.
11:22 Well, not quite. The alternative idea also a dud. Oh, dear!
17:53 Conclusion
___________________________________________________________________________________________
We'd like to thank our partners for helping to make this video series possible.
Support us by supporting our Partners, and at the same time get yourself a great deal with ISOtunes.
SOCIAL
As always, thank you so much to our Patrons, who help make videos like this possible.
Thank you again for all your support, we really appreciate it! – Ben
Stay tuned and stay awesome!
In this episode, Ben reduces the size of the neck blank and finalises the neck. Experiments with the slices of wood that will make up the body - unsuccessfully.
Chapters
0:00 Introduction
1:05 Marking out and cutting the neck and headstock
5:15 Slicing the offcuts - do they bend?
6:42 It works.
11:22 Well, not quite. The alternative idea also a dud. Oh, dear!
17:53 Conclusion
___________________________________________________________________________________________
We'd like to thank our partners for helping to make this video series possible.
Support us by supporting our Partners, and at the same time get yourself a great deal with ISOtunes.
SOCIAL
As always, thank you so much to our Patrons, who help make videos like this possible.
Thank you again for all your support, we really appreciate it! – Ben
Stay tuned and stay awesome!
Комментарии