filmov
tv
Lost Ancient High Technology In Egypt: Saw Marks And Drill Holes
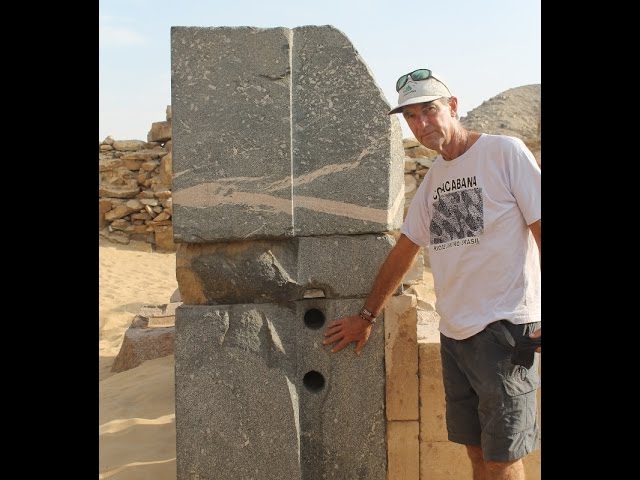
Показать описание
Lost Ancient High Technology Of Egypt Full Lecture
The Serapeum, Part I: Lost Ancient High Technology?
Evidence for Ancient High Technology - Part 1: Machining
Pre-Egyptian Technology Left By an Advanced Civilization That Disappeared
More Lost Ancient High Technology Of Egypt Part 1 Of 2
Joe Rogan on Ancient High Technology
Lost Ancient High Technology Evidence At Megalithic Sites
Lost Ancient High Technology And Dynastic Grandness In Egypt In 2017
'Mysterious Artifacts That REWROTE History | Secrets of Ancient Technology Revealed'
Expert REVEALS Discovered Ancient Relics Are So Advanced They Shouldn't Exist! | Ben Van Kerkwy...
Making Egyptian Drill Holes: Lost Ancient High Technology
THIS Ancient Egyptian Saw-Cut Proves They Had a Lost Technology
Lost Ancient High Technology On The Giza Plateau Of Egypt
Lost Ancient High Technology And Cataclysm At Ollantaytambo Peru
Lost Ancient High Technology In Peru: Highland City Of Wari
Lost Ancient High Technology Of Egypt 2017: Abu Ghurob
Ancient Egyptian Technology Left By An Advanced Civilization That Disappeared
Precision! - Evidence for Ancient High Technology, part 2
Lost Ancient High Technology Of Egypt 2018: Giza Plateau Machine Marks
Lost Ancient High Technology Of Mexico
Lost Ancient High Technology of the Valley Temple. Seriously though it's just good craftsmanshi...
More Lost Ancient High Technology In Egypt: Part 2 Of 2
Proof of Advanced Technology in Ancient Egypt?
Ancient Cataclysm And Lost High Technology At Tanis in Egypt
Комментарии