filmov
tv
Real-time Integration of Machine and Sensor Data for Predictive Maintenance
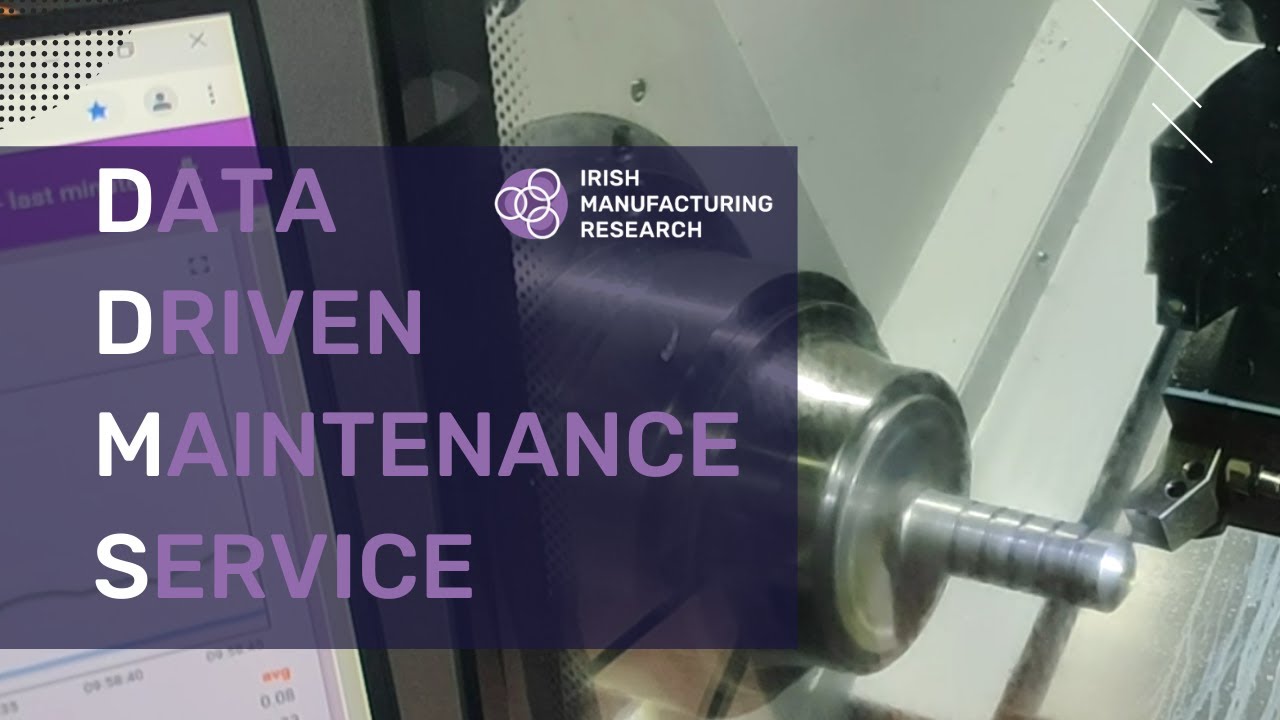
Показать описание
When trying to monitor a specific aspect of a machining process for predictive maintenance, such as the machine spindle, it is not only important to monitor the specific aspect but also capture what is occurring within the machine tool at the same time.
For the DDMS project (Data-driven Maintenance Service), monitoring spindle vibration is a good method of identifying behavior that can be detrimental to spindle life but monitoring spindle vibration alone did not go far enough to identify potential causes for spindle wear and potential premature spindle failure. We also needed to study the machine data in near real-time and correlate it to vibration monitoring. This enabled us to identify what is actually causing the vibration spikes and act accordingly.
For example, when we observe a vibration spike, we can query the potential root cause of the spike. What was the tool? Is it the same tool causing the spike each time? What was the feed rate override? Are operators manually interfering with the machine causing vibration spikes? Being able to create this digital version of the machine allows actionable decision-making and monitor the impact of changes as they are being made.
For the DDMS project (Data-driven Maintenance Service), monitoring spindle vibration is a good method of identifying behavior that can be detrimental to spindle life but monitoring spindle vibration alone did not go far enough to identify potential causes for spindle wear and potential premature spindle failure. We also needed to study the machine data in near real-time and correlate it to vibration monitoring. This enabled us to identify what is actually causing the vibration spikes and act accordingly.
For example, when we observe a vibration spike, we can query the potential root cause of the spike. What was the tool? Is it the same tool causing the spike each time? What was the feed rate override? Are operators manually interfering with the machine causing vibration spikes? Being able to create this digital version of the machine allows actionable decision-making and monitor the impact of changes as they are being made.