filmov
tv
Ancra Chain Loading & Unloading System in food business
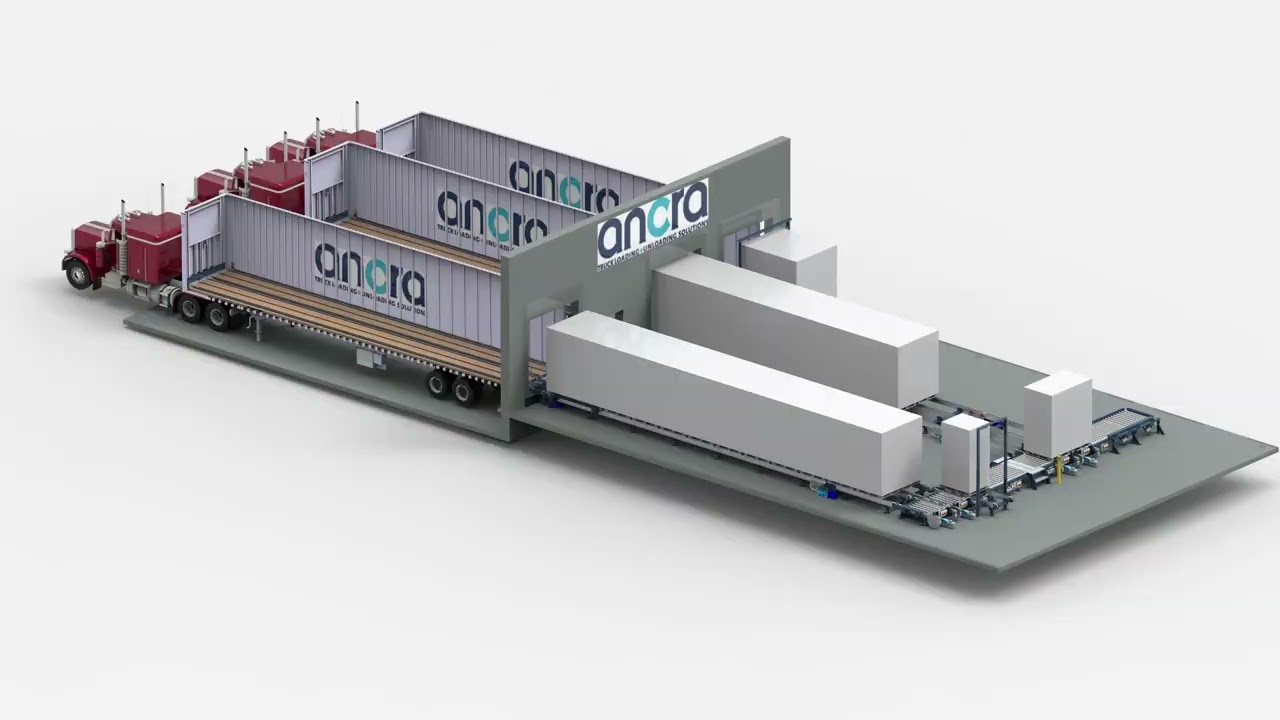
Показать описание
Loading
For shuttle transport between a food facility and the fully automated temperature-controlled warehouse (1-5 Celsius), located 5 miles further.
From the food production facility, two stationary chain conveyor loading systems will be integrated in the docks which are connected to their automated production line. The stationary chain loading systems are equipped with four chain conveyors for loading GMA pallets (40 x 48”). The stationary chain conveyor systems are automatically loaded by the buffer conveyor.
A back-up chain loading system in the third dock is available for manual feeding with forklift truck in the event of a jam in the production line.
There are three shuttle 53ft trailers that transfer the pallets to the warehouse. On arrival, the trailer is guided into a positioning frame installed in front of the loading bay to align the trailer position correctly.
The shuttle trailers are equipped with Ancra’s chain track systems. These chain tracks work together with the stationary system to allow for fully automatic loading in just 3 minutes. The tree trailers are driven between two locations Multiple times per hour, 7 days per week.
Unloading
When the truck arrives at the temperature-controlled warehouse, the trailer is docked, then the pallets unload onto the stationary chain conveyor systems fully automatic, in just three minutes as well.
This temperature-controlled warehouse receives pallets 24/7 without any warehouse personnel on the ground since the unloading is being done by Ancra’s ATLS system, in combination with other material handling equipment.
With Ancra’s modified cargo spaces ATLS solution, the overall loading or unloading cycle can be reduced from ± 35 minutes to 3 minutes with as result that a single dock door can handle up to four full trailers per hour.
Ancra is very excited to be part of this integrated solution. Ancra contributes to lowering food waste, transforming the food supply chain, keeping food fresher, improving the safety of loading & unloading, increasing the dock flow and saving a great deal of manpower.
For shuttle transport between a food facility and the fully automated temperature-controlled warehouse (1-5 Celsius), located 5 miles further.
From the food production facility, two stationary chain conveyor loading systems will be integrated in the docks which are connected to their automated production line. The stationary chain loading systems are equipped with four chain conveyors for loading GMA pallets (40 x 48”). The stationary chain conveyor systems are automatically loaded by the buffer conveyor.
A back-up chain loading system in the third dock is available for manual feeding with forklift truck in the event of a jam in the production line.
There are three shuttle 53ft trailers that transfer the pallets to the warehouse. On arrival, the trailer is guided into a positioning frame installed in front of the loading bay to align the trailer position correctly.
The shuttle trailers are equipped with Ancra’s chain track systems. These chain tracks work together with the stationary system to allow for fully automatic loading in just 3 minutes. The tree trailers are driven between two locations Multiple times per hour, 7 days per week.
Unloading
When the truck arrives at the temperature-controlled warehouse, the trailer is docked, then the pallets unload onto the stationary chain conveyor systems fully automatic, in just three minutes as well.
This temperature-controlled warehouse receives pallets 24/7 without any warehouse personnel on the ground since the unloading is being done by Ancra’s ATLS system, in combination with other material handling equipment.
With Ancra’s modified cargo spaces ATLS solution, the overall loading or unloading cycle can be reduced from ± 35 minutes to 3 minutes with as result that a single dock door can handle up to four full trailers per hour.
Ancra is very excited to be part of this integrated solution. Ancra contributes to lowering food waste, transforming the food supply chain, keeping food fresher, improving the safety of loading & unloading, increasing the dock flow and saving a great deal of manpower.