filmov
tv
Welding with 7014 rods
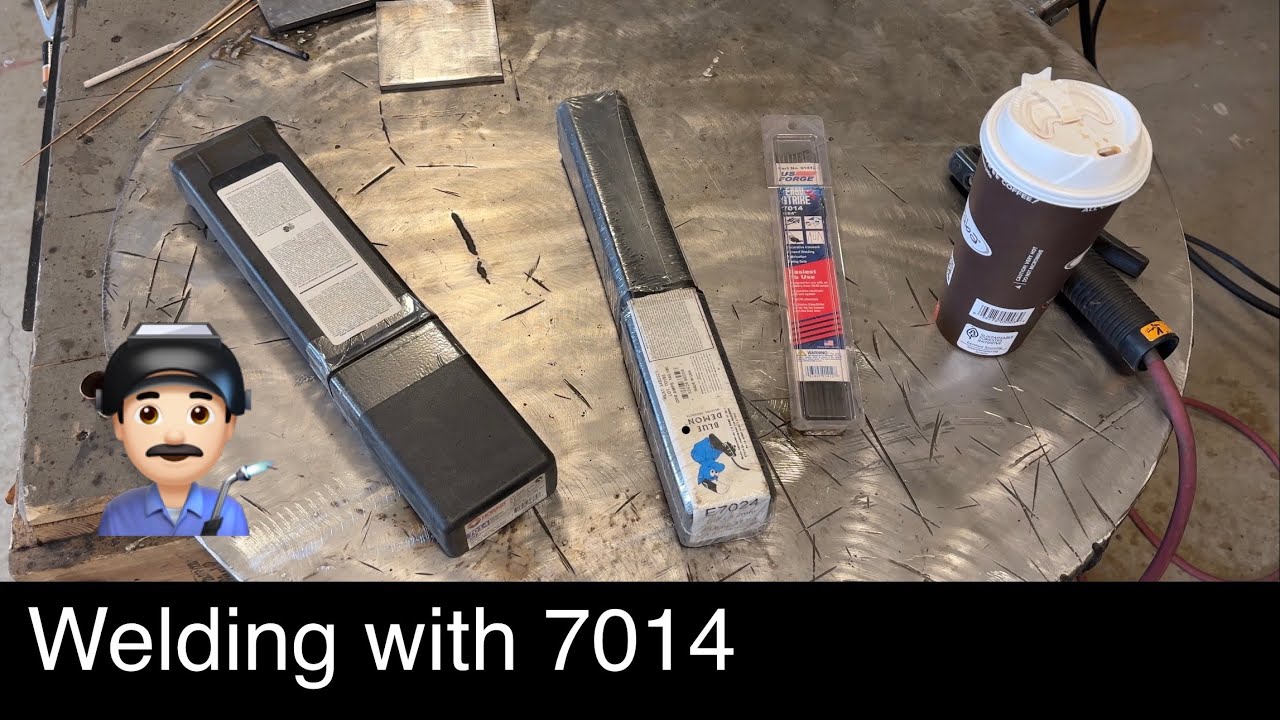
Показать описание
In this episode we we tackle welding with 7014 with mixed results.
For more info on the 7018 vs 7014 storage requirements
0:00:00 intro
0:01:33 7014 vs 7024
0:05:40 let’s weld
0:10:41 overview
0:12:58 vertical up
0:28:43 lap weld
For more info on the 7018 vs 7014 storage requirements
0:00:00 intro
0:01:33 7014 vs 7024
0:05:40 let’s weld
0:10:41 overview
0:12:58 vertical up
0:28:43 lap weld
Stick Welding with 7014 Electrodes
7014 - SHOULD YOU WELD WITH IT - STICK WELDING WITH THIS ELECTRODE
Welding with 7014 rods
Learning to Weld with 6013 and 7014 Electrodes
Stick Welding Easy Tack Welds: Use 7014 Rods
Blue Demon E7014 Carbon Steel Electrodes
My First Time Welding With 7014
7014 vs 7018 weld break test
How To Run 7014 Rods
Stick Welding Rod Overview
7014 Stick Welding Multi Pass T Joint practice
Are Harbor Freight Welding Rods Any Good?
How to weld with 7014: Second attempt
Welding 7014 1/8' rods.
Harbor Freight Welding Electrodes 1/16 E7014
7014 vs. 7018 stick electrodes
Retesting 7014 results from “Stick rod shootout”
amazing welding method of Pakistani welder #welding #shorts
Stick Welding: Which rod is my favorite?
How to choose the correct amperage for Stick Welding
Stick Welding: #1 Beginner Mistake and How to Fix It
Running a 7014 rod #welding #shorts
Stick Welding: How to Read the Puddle
What's a 7014 Electrode?
Комментарии