filmov
tv
High Speed Steel End Mills are Better than CARBIDE
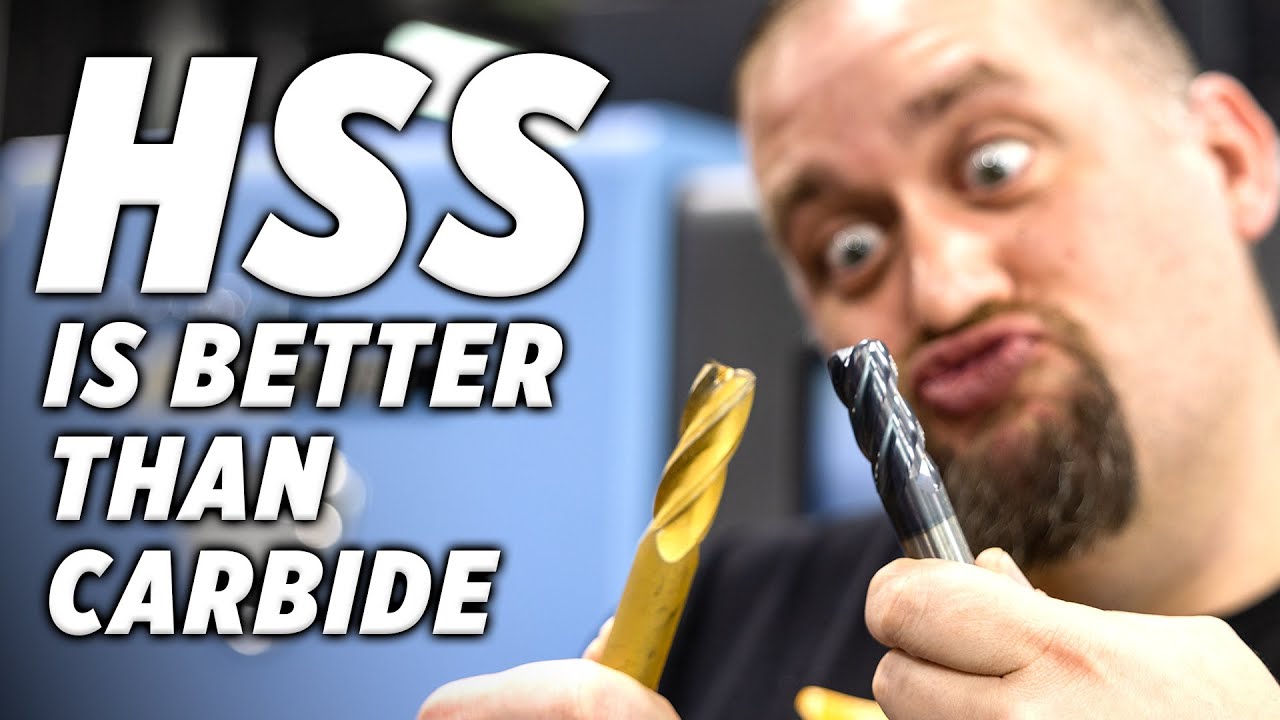
Показать описание
Help us fund FREE Education by purchasing tools seen in our videos here:
FREE CNC Machining Academy:
FREE Aerospace Academy:
___
___
FREE CNC Machining Academy. Join the Revolution:
Follow us on Instagram:
Like us on Facebook:
Join the conversation on our Facebook Group:
Connect with us on LinkedIn:
___
___
THANK YOU to our Partners who make this content possible:
#CNC #Machining #Machinist
FREE CNC Machining Academy:
FREE Aerospace Academy:
___
___
FREE CNC Machining Academy. Join the Revolution:
Follow us on Instagram:
Like us on Facebook:
Join the conversation on our Facebook Group:
Connect with us on LinkedIn:
___
___
THANK YOU to our Partners who make this content possible:
#CNC #Machining #Machinist
My HSS End Mill Will Machine Circles Around Your Carbide Tools
Guhring RF 100 end mills demonstrating high speed machining
High Speed Steel End Mills are Better than CARBIDE
NEW End Mill Cuts Through Stainless Steel Like BUTTER
Which is Better? High Speed Steel or Carbide Cutting Tools?
High Speed Steel Corner Rounding End Mill Sharp and wear-resistant CNC milling cutter
UKO End Mills – machining of hardened steel up to 68 HRC
SPEED TIGER 600Plus series HIGH Performance End Mills
Milling machining with YG-1 Only One end mill
KOR™ Series End Mills - Dynamic Milling Vs. Conventional Milling
A look at cheap Chinese end mills - carbide vs hss
HSS End Mill Titanium Coated CNC Router Bit 4 Flute Milling Bit
Carbide End Mills -U slot with high performance
SPEED TIGER END MILL- FHP+ High Performance, Heavy Duty
HRC60 Fine Pitch 4 Flutes Roughing End Mill for Stainless Steel
HRC65 CARBIDE END MILL FOR stainless steel
HRC 65 End Mill | 2023 End Mills for Carbon Steel, Alloy Steel and Cast Iron From Original Factory
HSS End Mill 1-30mm
Carbide Square End Mill
stainless steel endmill
ZLY Solid Carbide Endmill For Stainless Steel 4mm Carbide End Mill Face Milling Cutter#shorts #cnc
End mill breaking at 20,000 FPS
BFL Solid Carbide 6 Flutes High Speed End Mill For Aluminum
High performance carbide endmill
Комментарии