filmov
tv
Making A Universal Tailstock Die Holder Part 2
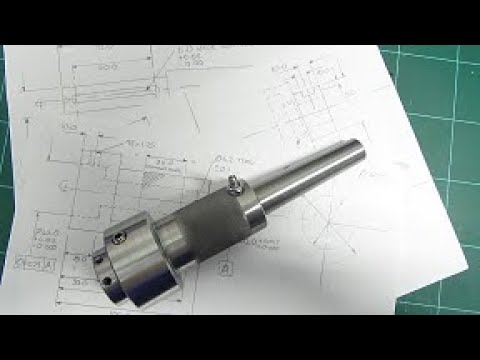
Показать описание
Part 2 of the Tailstock Die Holder - turning the Morse taper and milling a slot (first job on the mill since the re-build of the head)
Making A Universal Tailstock Die Holder Part 1
Making A Universal Tailstock Die Holder Part 5
Making A Universal Tailstock Die Holder Part 2
Making A Universal Tailstock Die Holder Part 3
Making A Universal Tailstock Die Holder Part 6
Making A Universal Tailstock Die Holder Part 7
Making a Threading Die Holder (Free Plans)
Live Free or DIE HOLDER
Tailstock die holder made from odds and sods.
Tailstock Die Holder Modification
Building A Tailstock Die Holder For The Lathe
Tailstock Die Holder Build
Making a UNIVERSAL Tap Follower || INHERITANCE MACHINING
Tailstock Threading Die Holder Tool
Machining A Threading Die Holder For My Lathe Tailstock
Easy Threading on the Metal Lathe with a Floating Die Holder
Finishing the bigboy tailstock die holder
Tailstock Tap and Die Holder (Tap Follower For Optimum OPTi turn lathe TU 2004V)
Tailstock Floating Die Holder Set
MHW Episode 98 - Tail Stock Button Die Holder
Cutting the Morse Taper with your compound for a Tailstock Die Holder
SNNC 320 P2 Door Number , Tailstock Die Holder Mod
Mini Lathe Tailstock Die Holder, 3D Printed Die Holder
Tailstock Die Holder MT3/ Sliding tailstock die holder
Комментарии