filmov
tv
Traditional vs Advanced Framing - Details
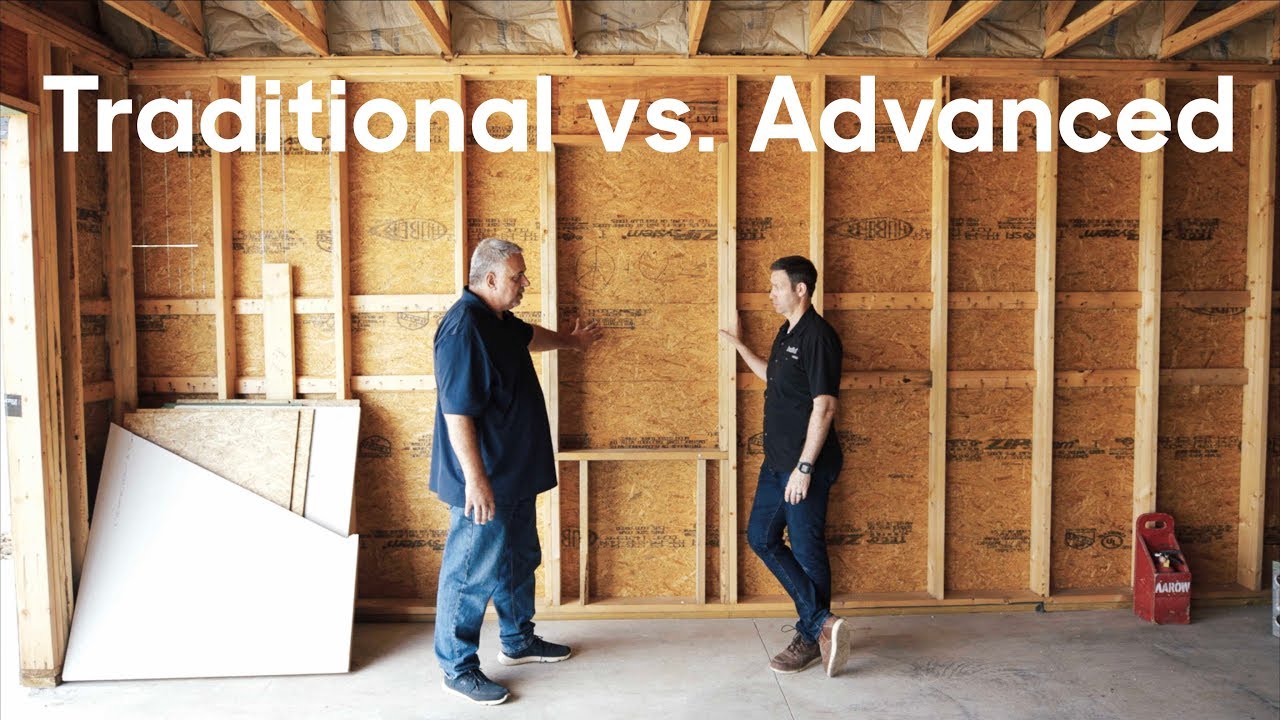
Показать описание
A well-framed house Is the start of a well-built house. That’s why it’s so important to ask: are we framing on 16 or 24 inch centers? Matt is on the scene with architect Steve Baczek to dive into the differences. First and foremost, Baczek wants us to stop calling this “advanced framing,” Instead, he refers to it as “smart” framing. Every house is unique and requires best-fit decision-making. So, it’s not necessarily about saving lumber or money, it’s about being smart from the start.
And what’s some of the best advice Steve has heard from an admired building scientist? When asked: what’s the best wall I can build? The answer is simple: Put as much insulation on the outside of the house as possible.
Huge thanks to our Show sponsors Polywall, Huber, Dorken Delta, Prosoco, Rockwool & Viewrail for helping to make these videos possible! These are all trusted companies that Matt has worked with for years and trusts their products in the homes he builds. We would highly encourage you to check out their websites for more info.
Комментарии