filmov
tv
Shredding Aluminum on the HAAS VM3!
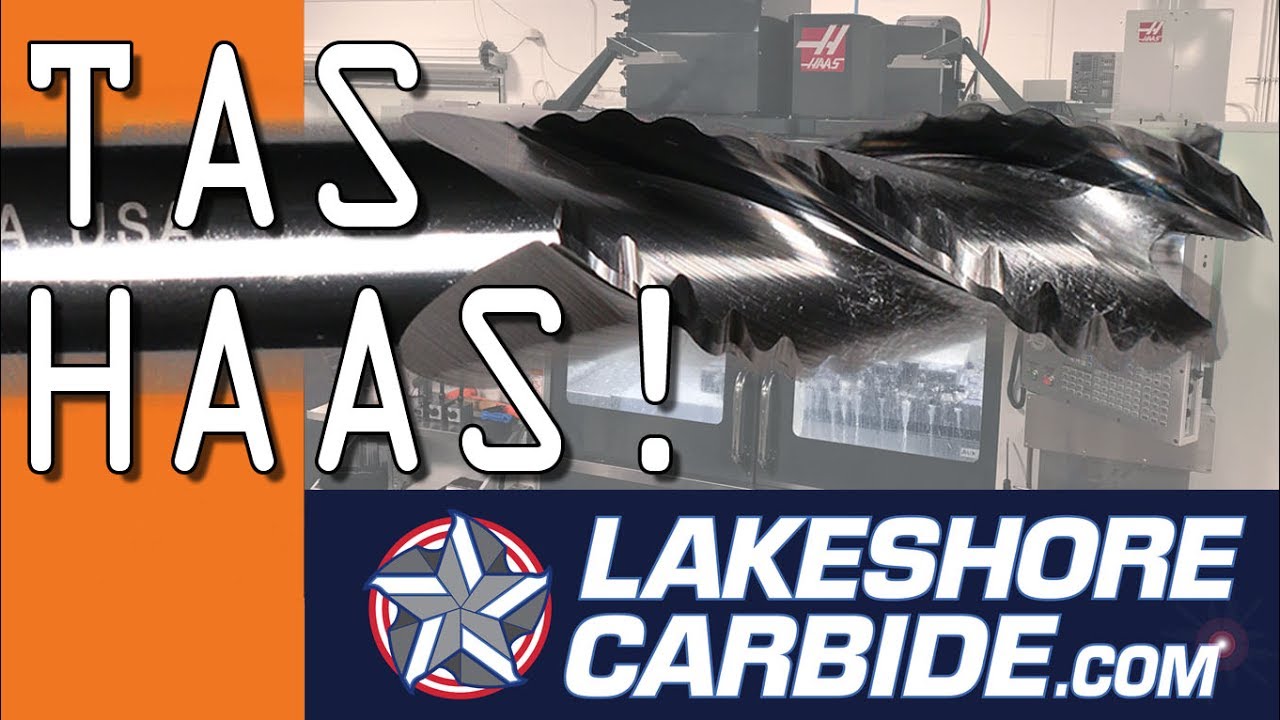
Показать описание
Testing out the Lakeshore Carbide TAS Roughing End Mill on the HAAS VM3 CNC Mill using Fusion 360 Adaptive CAM strategy.
Shredding Aluminum on the HAAS VM3!
HAAS VF2SS SHREDS Aluminum
🤯 TORMACH VS HAAS #cncmaching #tormach #haas #vf2ss
CNC Vertical Mill - Haas VF6 Chip Cleanout after aluminum machining.
WI GL2180 Two Shaft Shredder - Shredding Full Aluminium Cans (Product Trial)
CAMEC Aluminium and Non-Ferrous Metals Shredding Plant with TR4A
THIS is why machining is so impressive! 🤯
WEIMA G.200 Recycling press drains and compresses aluminum cans @Custom Recycling
Haas - Tyron 2000XL 2.0 - Shredder working on various waste streams
Aluminum bales recycling | MTB
Single shaft shredder and hammer mill processing aluminium - Broyeur à marteaux -
Hammel VB 750DK Long Version Shredder - Shredding Aluminium
Lathe Machine Actual video accidents #shorts #short
Destroying Metal with our Favorite Tools!
8ton per hour Aluminum Can Recycling Machine | Aluminum Vertical Shredder
GME - Aluminium Recycling Complete Line - Shredding & Sorting
Arjes VZ 750 on shredding laminated aluminum
aluminum beverage can shredder aluminum berrel shredder
HAAS TYRON Shredding Hen Cages
Cast Aluminum Scrap Crusher for Recycling
Machining a HUGE part on our HAAS VM3!
Scrap aluminum waste .Double shaft shredder machine #fante #shredding #shredded
HAAS TYRON | Green Waste Shredding
supply alloy rim crusher / aluminum bike rim shredder for recycling use
Комментарии