filmov
tv
Another DIY CNC router, part 5 (laser cut plates lookover, test cuts with MDF mockup)
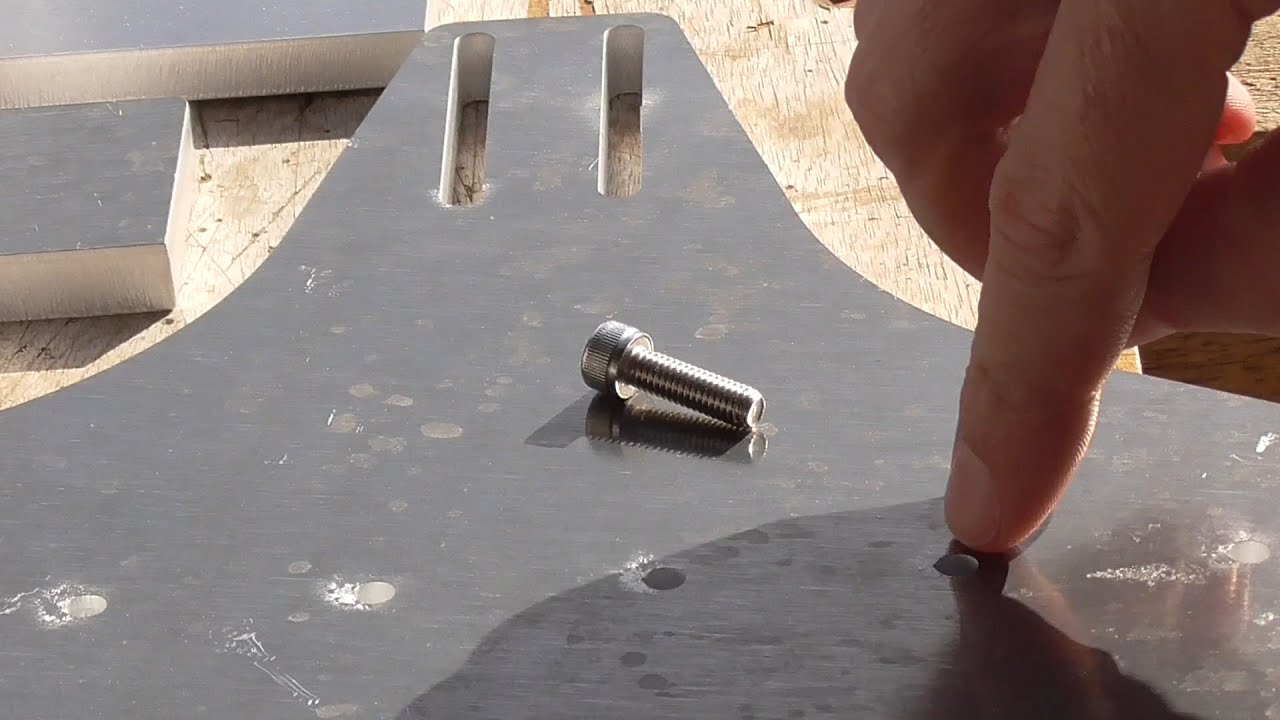
Показать описание
0:00 Laser cut parts lookover
8:48 Used 6mm plate stock
13:36 Surfacing with MDF mockup
14:44 Test cuts in aluminium with MDF mockup
I clamped the X rails to the bench temporarily to try some cuts. It's going well so far, but seriously needs tramming. Not sure if I can be bothered :)
8:48 Used 6mm plate stock
13:36 Surfacing with MDF mockup
14:44 Test cuts in aluminium with MDF mockup
I clamped the X rails to the bench temporarily to try some cuts. It's going well so far, but seriously needs tramming. Not sure if I can be bothered :)
Another DIY CNC router, part 2 (MDF mockup, steel bench construction, electronics enclosure started)
Another DIY CNC router, part 14 (conversion to RaspberryPi and weenyPRU)
DIY CNC Router Part 1 // Building a Small CNC Router
DIY CNC Router Part 2 // Building a Small CNC Router
Building a CNC Mill/Router - Part 3
Homemade CNC Router Part 2 - Building the Torsion Box
DIY CNC Machine - Frame Build | Part 1/2
DIY CNC Router - Part 1 Building the Frame
Cabinet makers rely on ShopSabre for perfect parts & exceptional edges
Making a DIY CNC machine with limited tools
HOMEMADE CNC ROUTER.
Making a CNC Router - Part 3
Making a CNC Router - Part 1
DIY CNC Router - Part 2 Linear Rails
DIY CNC Router Rebuild Part 1
Building a 5'x10' CNC Router from CNC Router Parts
V-Grooving Letters for Sign Making on CNC
Easily Set Zero Positions on CNC
Epoxy Creates a Huge Mess!
DIY CNC Machine - Electronics | Part 2/2
DIY CNC Router Build! Part:1
Making a CNC Router - Part 2
DIY CNC Router for Under $900 - Free Plans Available
Woodworking cnc router machine
Комментарии