filmov
tv
Solar Panel Manufacturing Process - Bluebird Solar
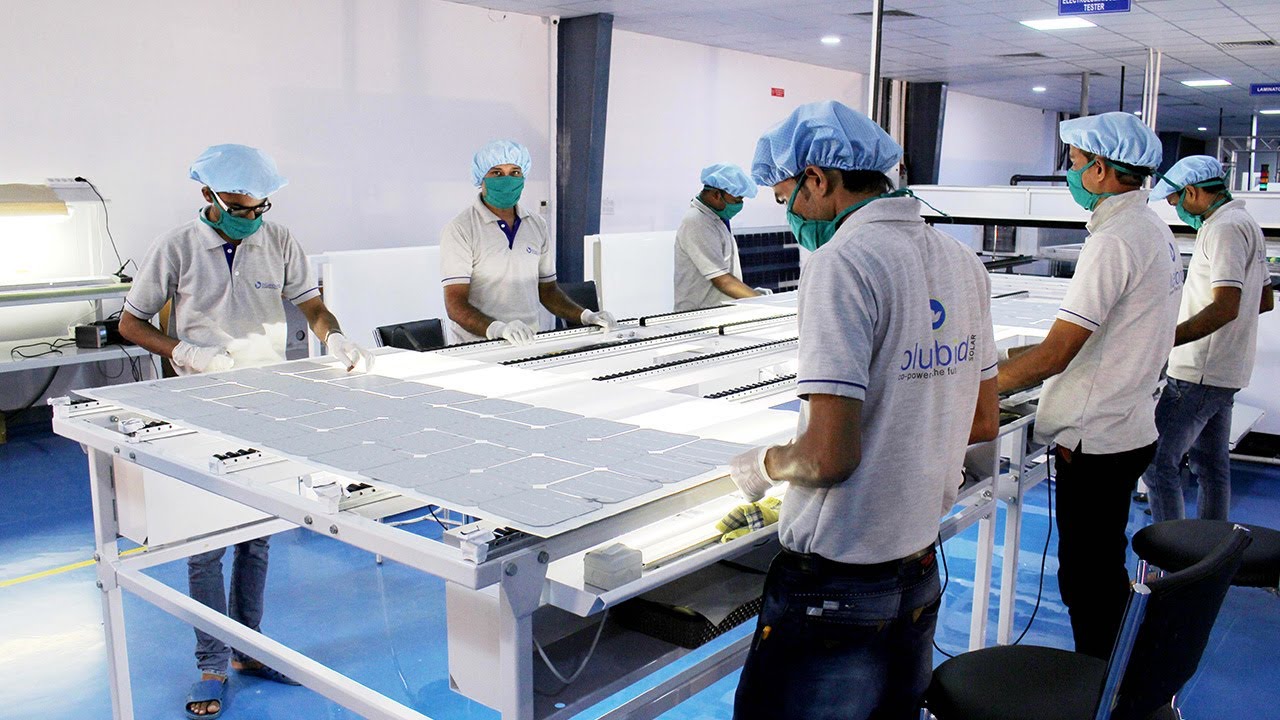
Показать описание
The process with which solar panels are manufactured and the way quality is controlled determines the quality of the solar photovoltaic module, which in turn is very crucial to achieve the maximum possible efficiency & output. We use A Grade Solar cells and other raw materials are also procured from Tier one suppliers. Following steps are involved in manufacturing of solar panels:
1. Cell Testing & Cutting
Solar cells are checked and inspected using advanced optical or imaging sensors to ensure all the components are located correctly and the cells wafers, which are very delicate, are not damaged or cracked. and with the help of a laser machine they cut into different dimension depending on the wattage of Solar Panel. Cutting is skipped where full size cell is required.
2. Tabbing & Stringing
To make a solar cell array the first step is tabbing and stringing. Multiple ribbons are first soldered to the front and back surfaces of individual PV cells (tabbing). After tabbing the stringer subsystem which solders the front side ribbons of a first PV cell to the back side ribbons of the neighboring PV cell to form strings of PV cells wired in series.
3. Lay-up & Bussing
In this process the solar cell strings from the stringer are placed on layup table above EVA-covered glass. A small pieces of adhesive tape is applied the on the cells to hold them in place. This process is called lay-up. Now second layer of EVA sheet, polymer back-sheet is placed on solar cell array. The bus wire is soldered with tab wires .
4. Visual Inspection
Visual inspection of a PV module performed before the module has been subjected to environmental, electrical, or mechanical stress testing in the laboratory. This visual inspection is done by looking at the glass underneath to check the PV module alignment, cell matrix and presence of dust particle or other element on cell.
5. Electroluminescence Testing
Bluebird solar panels are 100% EL tested. Electroluminescence technology allows asset us to clearly identify the defects in the modules that are invisible otherwise like cell damage / microcracks in the inner structures of the solar cells that can cause underperformance or hot spots in the future. This also checks inactive strings, cell breakage and fissures.
6. Lamination
The encapsulation of the solar cells through lamination is a crucial step in solar panel manufacturing. It ensures longevity of the solar cells of the PV Module. During the lamination process, the prepared 5-layer module is placed in the lamination machine and heated to max. 135°C for 20 -25 minutes. The laminate that comes out is completely sealed and is left for 10-15 minutes to cool down till it reaches room temperature.
7. Framing
Solar panel framing refers to the process of attaching protective and strengthening aluminum frames to the PV laminates of a solar panel. The frame that slides around the laminate will be filled with silicon adhesive. Then, the frame will be pressed around the laminate. The holes on the back of a PV frame make it easy to install the panels on a mounting structure.
8. Sun Simulation Testing
Sun SimulatorTest or Flash Test measure the output performance of a solar PV module. During a flash test the PV module is exposed to a short (1ms to 30 ms), bright (100 mW per sq. cm) flash of light whose output spectrum is as close to the spectrum of the sun as possible. Module parameters are measured at standard test conditions (STC). The results of the flash test are compared to the data specifications of the PV module type which are then printed on the label and pasted at the back of solar panel.
9. Fixing Junction Box
An IP68 rated PV junction box is attached to the back of the solar panel with silicon adhesive. It is the output interface of the solar panel. The diodes inside the junction box keeps the power flow going in one direction, and prevent current from feeding back into the panels when there's no sunshine. it is connected to MC4 connectors with the help of 4mm cables.
10. Cleaning & Packing
The module is then wiped to remove any traces of dust, foreign particles or extra sealant. Being high-priced products, we cannot ignore the significance of correct, safe and efficient packaging of the solar panels. So, Bluebird solar panels are then are then stacked in a boxes. Separators are placed between each module and extra protections are added to the four corners of each module stack. In some cases, modules are also packed in individual cartons boxes to be packed into a large master carton box. Palette packing is also done on demand from customer or on basis of order quantity .
#solarpanels #renewableenergy
1. Cell Testing & Cutting
Solar cells are checked and inspected using advanced optical or imaging sensors to ensure all the components are located correctly and the cells wafers, which are very delicate, are not damaged or cracked. and with the help of a laser machine they cut into different dimension depending on the wattage of Solar Panel. Cutting is skipped where full size cell is required.
2. Tabbing & Stringing
To make a solar cell array the first step is tabbing and stringing. Multiple ribbons are first soldered to the front and back surfaces of individual PV cells (tabbing). After tabbing the stringer subsystem which solders the front side ribbons of a first PV cell to the back side ribbons of the neighboring PV cell to form strings of PV cells wired in series.
3. Lay-up & Bussing
In this process the solar cell strings from the stringer are placed on layup table above EVA-covered glass. A small pieces of adhesive tape is applied the on the cells to hold them in place. This process is called lay-up. Now second layer of EVA sheet, polymer back-sheet is placed on solar cell array. The bus wire is soldered with tab wires .
4. Visual Inspection
Visual inspection of a PV module performed before the module has been subjected to environmental, electrical, or mechanical stress testing in the laboratory. This visual inspection is done by looking at the glass underneath to check the PV module alignment, cell matrix and presence of dust particle or other element on cell.
5. Electroluminescence Testing
Bluebird solar panels are 100% EL tested. Electroluminescence technology allows asset us to clearly identify the defects in the modules that are invisible otherwise like cell damage / microcracks in the inner structures of the solar cells that can cause underperformance or hot spots in the future. This also checks inactive strings, cell breakage and fissures.
6. Lamination
The encapsulation of the solar cells through lamination is a crucial step in solar panel manufacturing. It ensures longevity of the solar cells of the PV Module. During the lamination process, the prepared 5-layer module is placed in the lamination machine and heated to max. 135°C for 20 -25 minutes. The laminate that comes out is completely sealed and is left for 10-15 minutes to cool down till it reaches room temperature.
7. Framing
Solar panel framing refers to the process of attaching protective and strengthening aluminum frames to the PV laminates of a solar panel. The frame that slides around the laminate will be filled with silicon adhesive. Then, the frame will be pressed around the laminate. The holes on the back of a PV frame make it easy to install the panels on a mounting structure.
8. Sun Simulation Testing
Sun SimulatorTest or Flash Test measure the output performance of a solar PV module. During a flash test the PV module is exposed to a short (1ms to 30 ms), bright (100 mW per sq. cm) flash of light whose output spectrum is as close to the spectrum of the sun as possible. Module parameters are measured at standard test conditions (STC). The results of the flash test are compared to the data specifications of the PV module type which are then printed on the label and pasted at the back of solar panel.
9. Fixing Junction Box
An IP68 rated PV junction box is attached to the back of the solar panel with silicon adhesive. It is the output interface of the solar panel. The diodes inside the junction box keeps the power flow going in one direction, and prevent current from feeding back into the panels when there's no sunshine. it is connected to MC4 connectors with the help of 4mm cables.
10. Cleaning & Packing
The module is then wiped to remove any traces of dust, foreign particles or extra sealant. Being high-priced products, we cannot ignore the significance of correct, safe and efficient packaging of the solar panels. So, Bluebird solar panels are then are then stacked in a boxes. Separators are placed between each module and extra protections are added to the four corners of each module stack. In some cases, modules are also packed in individual cartons boxes to be packed into a large master carton box. Palette packing is also done on demand from customer or on basis of order quantity .
#solarpanels #renewableenergy
Комментарии