filmov
tv
This did not go smoothly
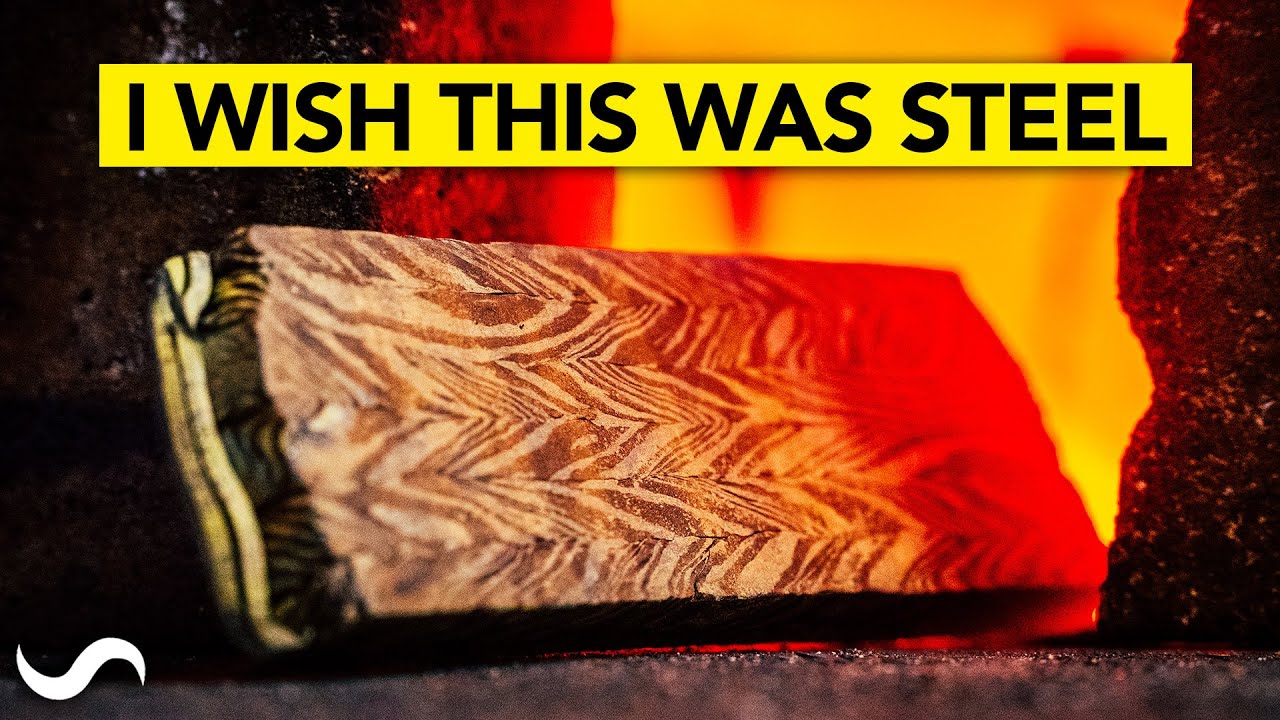
Показать описание
My name is Alec Steele. I am a blacksmith, amateur machinist and all-round maker of all-things metal. We make videos about making interesting things, learning about craft and appreciating the joy of creativity. Great to have you here following along!
MUSIC:
-signing up at this link supports the show!
- signing up at this link supports the show!
------------------------------------------------
AMAZON AFFILIATE LINKS TO GEAR I LIKE, buying here supports us:
--------------
This did not go smoothly
This project did not go smoothly
Well, it did not go as planned #shorts #funny
This did not go smoothly!!
This did not go well 😅 #shorts
That didnt go well…💀😂 #shorts #viral
This Did NOT Go Smoothly | Our First Calving Experience…
This one did not go well
this did not go well 😭
This did not go well…
GMFU #countryhuman #usa #edit edit: bro the animation did not go smoothly
His first day of school did not go well for some reason 😅
This Did Not Go Well... 😭😂
Things are not going well for Inter at all. 🤕
This did not go well….. #shorts #youtube #youtubeshorts #trending #trend #fyp #funny #relatable #yt...
This Christmas card didn’t go well 😂
This did not go well 😂
How to move off smoothly in a manual car #drivingtesttips
This did NOT go well for her 😟
Emptying the swimming pool didn’t go well 😂
This did NOT go smoothly - Vlogmas Day 14
This Did Not Go Well For Nintendo...
GI Joe and Vintage Star Wars trade ! ( THIS DID NOT GO WELL!)
I published my first book at 15...it did not go well.
Комментарии