filmov
tv
Alimak raise climber
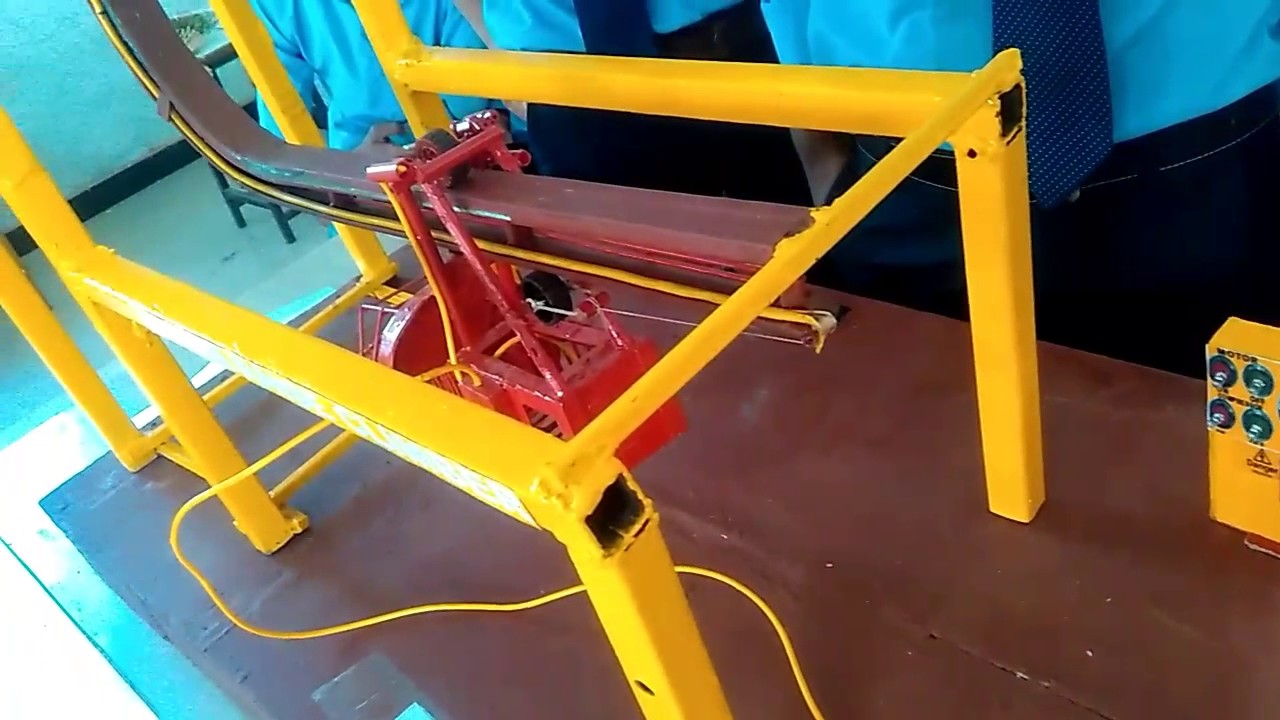
Показать описание
Raise Climber Mining Conditions
This type of mining is best suited to tabular narrow vein ore bodies with enough dip for gravity ore flow.
There is often considerably less waste development with raise mining than with regular open stoping. A narrow vein ore body has less ore to soak up waste development costs, making the raise mining method an obvious choice.
It is better if the ore body is continuous over several hundred feet vertically. Experience has shown that raises from 75 to 150 metres length are the most economical.
The method works best if the ore boundaries can be interpolated between adjacent raises. This allows the drill planning to be done before the production drill is set up in the raise. This is less important in sulphides, where the driller can tell if the bit is in ore by the colour of the cuttings.
Raise Climber Mining Method Details
The raise climber mining method will generally be comprised of the following steps:
Development
Bottom Sill: Access and haulage: These drifts are driven from the shaft or established mining areas to the new ore zone. The drifts are commonly sized to accommodate the large scooptrams used for production mucking and are often driven with jumbos.
Drawpoints and Climber Nest: Drawpoints can be driven from either footwall or hangingwall, depending on how the ore zone is accessed. The climber nests are always in the hangingwall. The climbers require about 4.3 metres (14') width, 2.7 metres (9') of height and 12 metres (39') of length with extra added on for "Alicabs" and/or for low angle raises. The nest will be slashed out of the drawpoint backs if development is from the hangingwall side.
Top Sill Access: These drifts are also driven from the shaft or existing development but, unless there is another lift, they often need only be large enough for the movement of supplies.
Raises
Raise Development: Raises must be driven big enough that a 2.4 metre (8') drill can be rotated within them, or about 2.7 x 2.7 metres (9' x 9') horizontally.
Raise Rehabilitation: After the raise is driven it often must be rehabilitated, subject to ground conditions, for the safety of production crews.
Hangingwall Support: Where required, the stope hangingwall can be supported with deformed strand resin-grouted cable bolts in a regular pattern along the raise. This is very cost effective as the raise is centred in the stope, which concentrates the support where it is needed most.
Production
Drilling: Drill holes extend to just less than half way to the next raise and are oriented slightly down from horizontal. The down dip helps the toes break to the stope wall. Hole diameters are often fairly small to avoid hangingwall / footwall damage in narrow veins.
Loading & Blasting: The holes are most often mechanically loaded with either ANFO or an emulsion explosive. The blasts are timed to slash down, with the footwall holes often the last to fire. It is safest to take a few rings per blast, so that miss-holes or other blasting problems are accessible for correction.
Mucking Swell: It is often best to leave ore in the stopes while blasting because of the support it gives. The broken ore often compacts slightly, resulting an effective swell of about one third its unbroken volume.
Final Mucking: This step is done once the stope is completely blasted.
This type of mining is best suited to tabular narrow vein ore bodies with enough dip for gravity ore flow.
There is often considerably less waste development with raise mining than with regular open stoping. A narrow vein ore body has less ore to soak up waste development costs, making the raise mining method an obvious choice.
It is better if the ore body is continuous over several hundred feet vertically. Experience has shown that raises from 75 to 150 metres length are the most economical.
The method works best if the ore boundaries can be interpolated between adjacent raises. This allows the drill planning to be done before the production drill is set up in the raise. This is less important in sulphides, where the driller can tell if the bit is in ore by the colour of the cuttings.
Raise Climber Mining Method Details
The raise climber mining method will generally be comprised of the following steps:
Development
Bottom Sill: Access and haulage: These drifts are driven from the shaft or established mining areas to the new ore zone. The drifts are commonly sized to accommodate the large scooptrams used for production mucking and are often driven with jumbos.
Drawpoints and Climber Nest: Drawpoints can be driven from either footwall or hangingwall, depending on how the ore zone is accessed. The climber nests are always in the hangingwall. The climbers require about 4.3 metres (14') width, 2.7 metres (9') of height and 12 metres (39') of length with extra added on for "Alicabs" and/or for low angle raises. The nest will be slashed out of the drawpoint backs if development is from the hangingwall side.
Top Sill Access: These drifts are also driven from the shaft or existing development but, unless there is another lift, they often need only be large enough for the movement of supplies.
Raises
Raise Development: Raises must be driven big enough that a 2.4 metre (8') drill can be rotated within them, or about 2.7 x 2.7 metres (9' x 9') horizontally.
Raise Rehabilitation: After the raise is driven it often must be rehabilitated, subject to ground conditions, for the safety of production crews.
Hangingwall Support: Where required, the stope hangingwall can be supported with deformed strand resin-grouted cable bolts in a regular pattern along the raise. This is very cost effective as the raise is centred in the stope, which concentrates the support where it is needed most.
Production
Drilling: Drill holes extend to just less than half way to the next raise and are oriented slightly down from horizontal. The down dip helps the toes break to the stope wall. Hole diameters are often fairly small to avoid hangingwall / footwall damage in narrow veins.
Loading & Blasting: The holes are most often mechanically loaded with either ANFO or an emulsion explosive. The blasts are timed to slash down, with the footwall holes often the last to fire. It is safest to take a few rings per blast, so that miss-holes or other blasting problems are accessible for correction.
Mucking Swell: It is often best to leave ore in the stopes while blasting because of the support it gives. The broken ore often compacts slightly, resulting an effective swell of about one third its unbroken volume.
Final Mucking: This step is done once the stope is completely blasted.
Комментарии