filmov
tv
WHAT'S INSIDE? -BLOW THROUGH CARBS
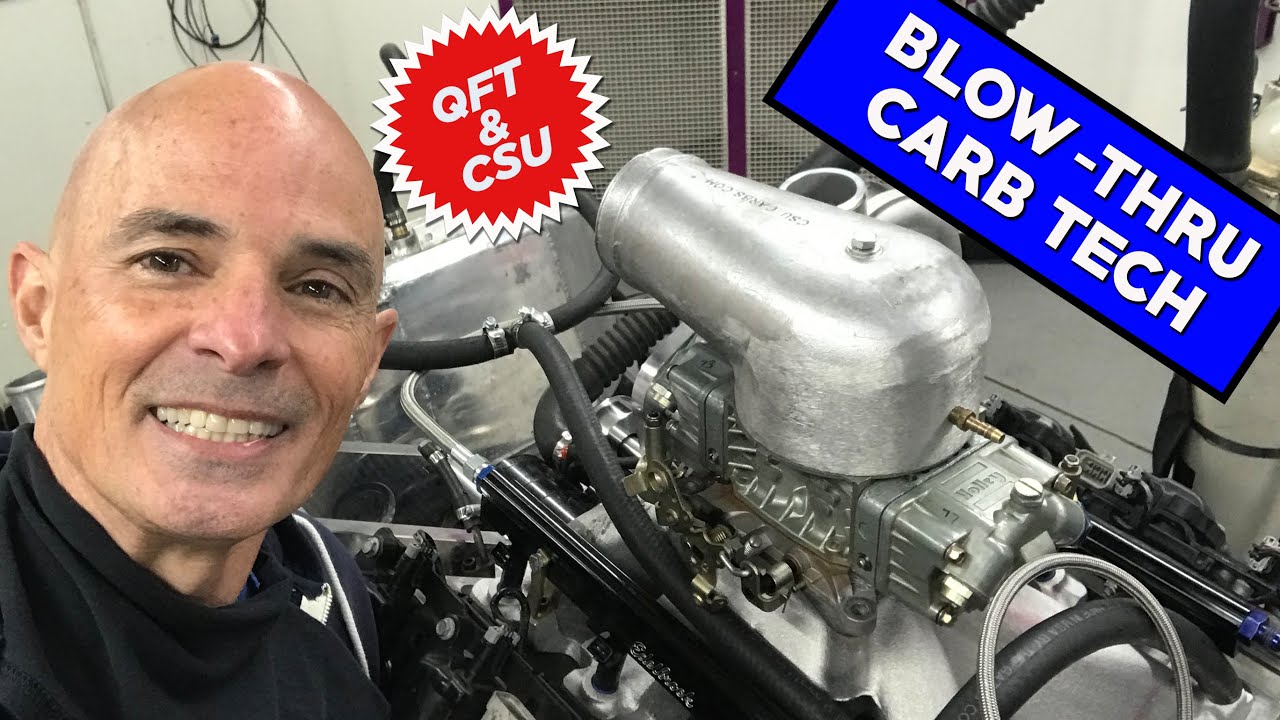
Показать описание
CSU & QUICK FUEL-WE LOOK INSIDE BOTH! Kevin from CSU steps up to help our twin-TorqStorm 6.0L with customer carb. Trying to run two superchrgers with an E85 blow-through carb. Check out what happens when we throw the kitchen sink at it! We look inside the Quick Fuel and CSU carbs to see what makes them tick.
WHAT'S INSIDE? -BLOW THROUGH CARBS
BLOW THROUGH CARB SECRETS. Inside Billy The Kid’s CSU 750
How To Turbo A Carbureted Engine Easily! |Blow Through Holley Carb Tuning | Carbureted Turbo LS
How Blow Through Carb Systems Work. It makes too much power!
What Makes a Demon Blow Through Carburetor Special?
No Body Remembers This Forgotten Draw Through Turbocharger VS Blow Thru Turbo | Carbureted Turbo LS
Switching From EFI To A BLOW THROUGH CARB! - Here's What We Got
misconceptions of a blow through carburetor. taking a look in a 750 C&S Billet aerosol carburet...
How to build A Budget Blow Through Carburetor
Inside a 1000 Horsepower E85 blow through carburetor for my 400 SBC Supercharged S10!
Tuning Blow-Though Carburetor
LET'S TALK TECH-BLOW THROUGH CARBS
Basic Holley Carburetor Modifications for Blow Through
CARBS, CAMS & TURBOS!! DOES IT WORK?
Blow Thru Carb Talk!
Everything You Need To Know About Edelbrock Carbs In A Minute
Edelbrock VRS-4150 for Blow Through Applications: Everything You Need to Know
DIY Carbureted Turbo Idle, stage 1 cam | DIY blowthrough carb
FAST Blowthrough Carb Replacement - New Product at SEMA 2015
Blow Through Carburetor Gen 1 SBC
Plumbing Wastegate and Blow Off Valve Explained on a Blow-Thru Carburetor
Ebay Turbo+Weber Carb = WIN! ...and fail
Building A Blowthrough #1 - Selecting the right carb
DIY Blow Through Carburetor Build For The Budget Turbo Carbureted LS | Part 1 | Proform Race Series
Комментарии