filmov
tv
Bend Almost Anything With This DIY Finger Brake Press
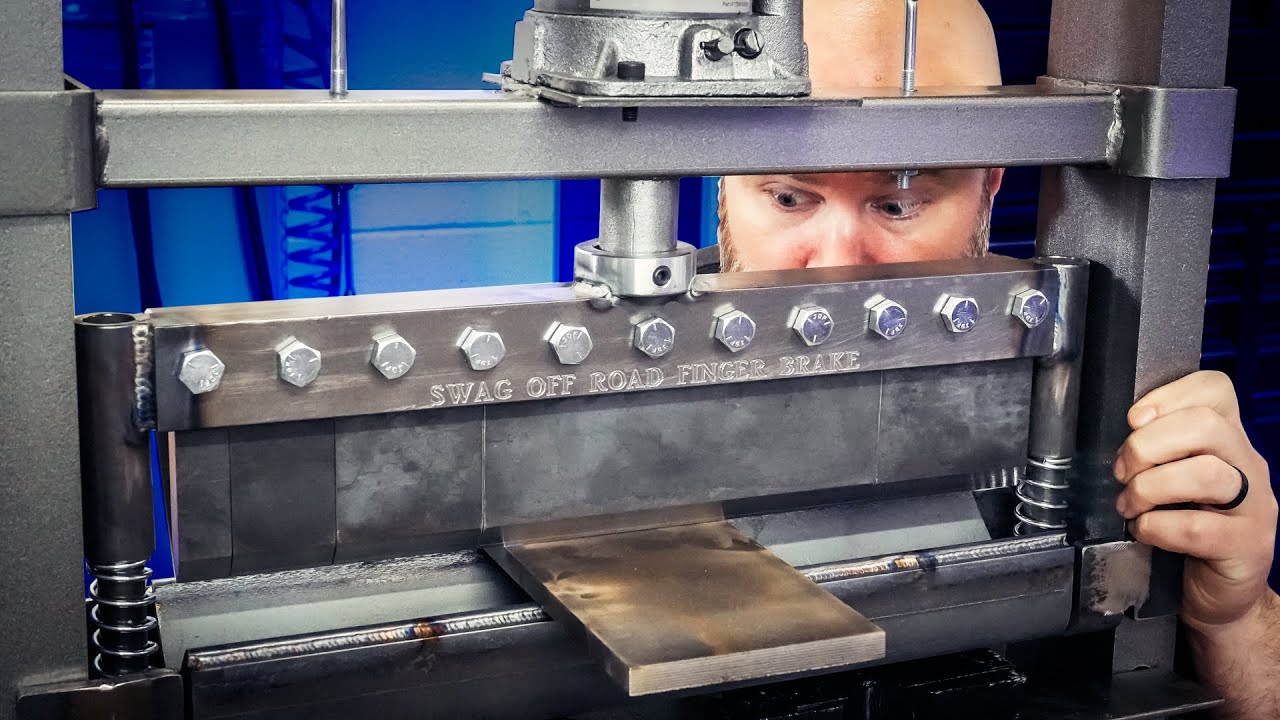
Показать описание
Turn Your Harbor Freight 20 Ton Press Into a Heavy Duty Finger Brake with this kit from SWAG Off Road. TIG or MIG Weld Yourself.
Brought to you by Everlast Welders:
Everlast Links
Socials:
Brought to you by Everlast Welders:
Everlast Links
Socials:
Bend Almost Anything With This DIY Finger Brake Press
This man can bend anything! 😮💪 - 🎥 armandofogaca_
Steel plate bending equipment- Good tools and machinery make work easy
The MOST flexible man in the WORLD 😱
Welcome to Snake's Bend
This Ancient Teaching Will Bend Your Reality (Almost Banned!)
Bend The Bar, Win $100
Bend Press 20 ton Benchtop Press Brake at Trick-Tools!
Eric Clapton's Unusual String Bending Technique Revealed
Move Almost Anything With This Tool!
Kinneret - No Wind Resistance! (Official Video)
Absolutely Anything by CG5 (feat. OR3O) [ORIGINAL Music Video]
Under The Hood of One of The Fastest Swings in Golf
Bad Omens - The Death Of Peace Of Mind (Lyrics) 🎵
Kinneret - No Wind Resistance (sped up/tiktok remix) Lyrics | i've been here 60 years
This Ancient Teaching Will Bend Your Reality (Almost Banned!)
Minecraft but You Can BEND Anything...
Thin plate overflat bending on hydraulic press brake!
This Ancient Secret Will Bend Your Reality (Almost Banned!)
DIY Hydraulic Press Brake PART 1 - Repeatable Bends using Limit Switches
Want To Be Able To Fix Almost Anything? Then Learn How To Weld With Brass!
I Can Move My Body Like Anything | Movement Song for Kids | Jack Hartmann
Bend anything Harbor Freight press
Awesome And Amazing Metal Bending Techniques #shorts
Комментарии