filmov
tv
Make Your Own Optical Lenses
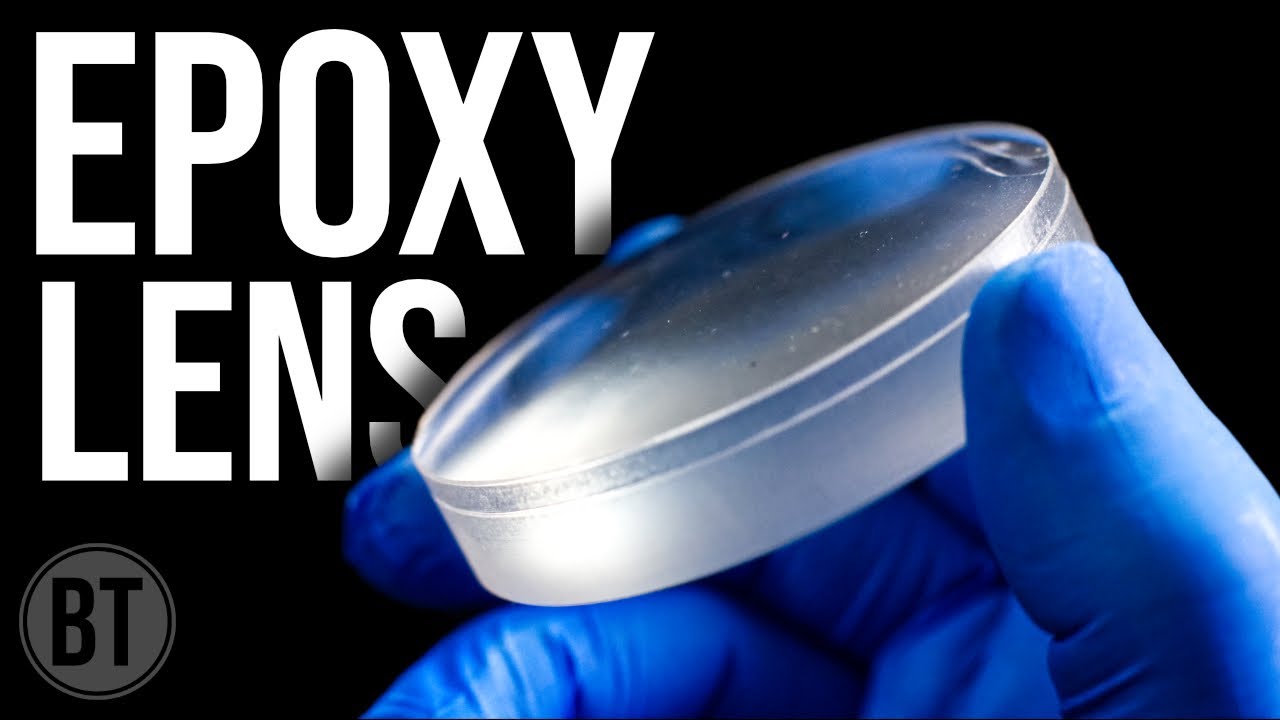
Показать описание
Today we're making lenses with epoxy, using a replication molding technique. It... mostly works 😇
CONSIDER SUBSCRIBING 🥰
==== Details ====
We can replicate lenses using silicone molds and optical epoxy resin. But there are a lot of caveats to this technique, and little hiccups that will ruin the optical finish. To achieve an optical finish, you need surface roughness and figure deviation in the nanometer range. This means curing temperature and shrinkage become major sources of error.
Residual stress in the molded parts can be assessed with polarized light and a polarizer in front of the camera.
==== Prior Videos ====
==== Materials ====
Mold material: Smooth-On Mold Max XLS ii
Optical resin: Smooth-On Epoxacast 690 clear
==== Analysis Equipment ====
Phenom XL SEM from Thermo
Gwyddion for AFM post-processing
Blender for 3D AFM rendering
==== Timeline ====
0:00 Intro
1:09 Replication Molding
3:04 Alternative mandrel material
3:37 Molding and casting technique
4:30 Fabricated lens examples
7:26 Molding priorities
9:38 Molding materials and considerations
10:49 Mold release difficulties
14:30 Shrinkage difficulties
16:04 Effect of Temperature
17:20 Internal stress and polarized light
18:51 Mechanical difficulties
19:40 Alternatives to silicone?
20:40 Direct molding off mandrel?
21:45 Refinement for future work
23:45 Concluding remarks
CONSIDER SUBSCRIBING 🥰
==== Details ====
We can replicate lenses using silicone molds and optical epoxy resin. But there are a lot of caveats to this technique, and little hiccups that will ruin the optical finish. To achieve an optical finish, you need surface roughness and figure deviation in the nanometer range. This means curing temperature and shrinkage become major sources of error.
Residual stress in the molded parts can be assessed with polarized light and a polarizer in front of the camera.
==== Prior Videos ====
==== Materials ====
Mold material: Smooth-On Mold Max XLS ii
Optical resin: Smooth-On Epoxacast 690 clear
==== Analysis Equipment ====
Phenom XL SEM from Thermo
Gwyddion for AFM post-processing
Blender for 3D AFM rendering
==== Timeline ====
0:00 Intro
1:09 Replication Molding
3:04 Alternative mandrel material
3:37 Molding and casting technique
4:30 Fabricated lens examples
7:26 Molding priorities
9:38 Molding materials and considerations
10:49 Mold release difficulties
14:30 Shrinkage difficulties
16:04 Effect of Temperature
17:20 Internal stress and polarized light
18:51 Mechanical difficulties
19:40 Alternatives to silicone?
20:40 Direct molding off mandrel?
21:45 Refinement for future work
23:45 Concluding remarks
Комментарии