filmov
tv
How to build a Pressure Cooker Pot Still
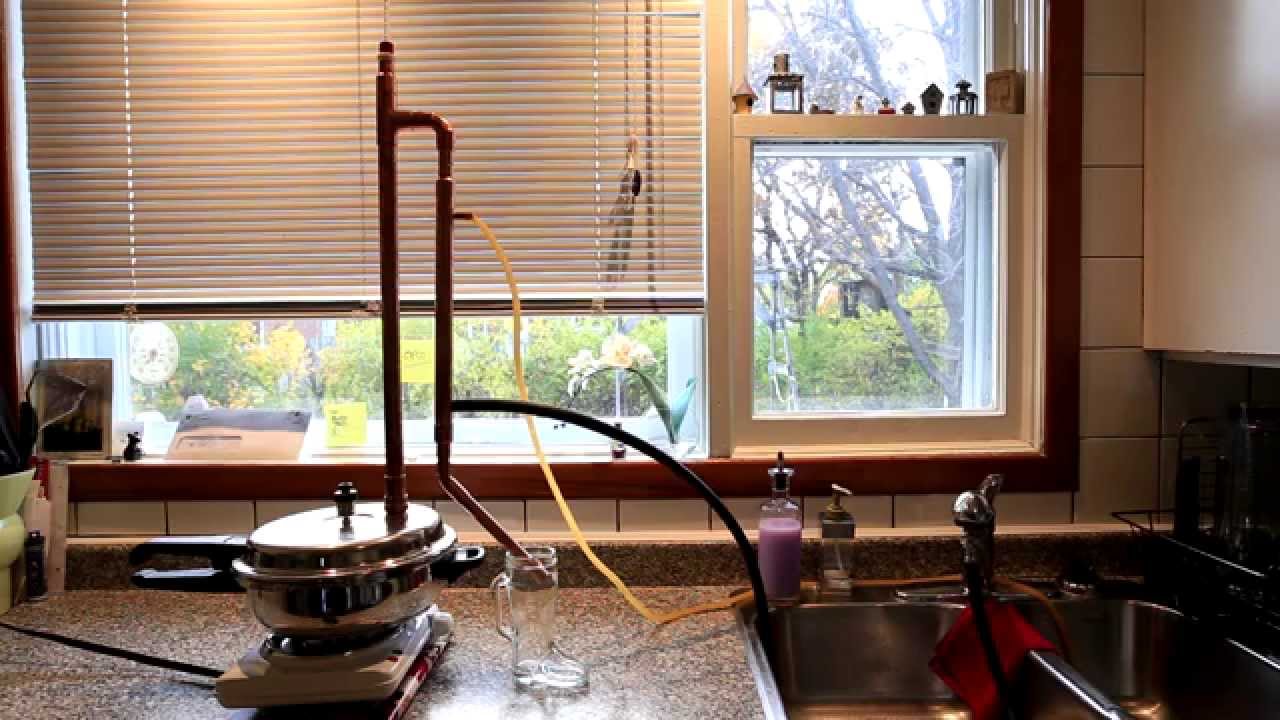
Показать описание
Warning: This is not a video on distillation, but I still I warn you not to distill flammable solvents in a poorly ventilated area!
In this video I will be showing you how I went about building my own pot still. The purpose of this video is to give an idea of what goes into making one. Keep in mind that this is my own design and there are bound to be design flaws. There are definitely improvements that can be made.
In this video I will be showing you how I went about building my own pot still. The purpose of this video is to give an idea of what goes into making one. Keep in mind that this is my own design and there are bound to be design flaws. There are definitely improvements that can be made.
How to build a Pressure Cooker Pot Still
How Air Pressure Can Screw Up Your Home: the House of Pressure
Assemble your own pressure washer from random parts
Build Your Own Pressure Sensor / Velostat / Scamp3
How to build a Pressure Sensor
DIY Water Tower - Amazing Pressure!!
How to Plumb a Pressure Washing Trailer & Soft Wash Setup
DIY Pressure Chamber & Safety Considerations
The CHEAPEST Pressure Washing Trailer Build
Slow Air Pressure Build Up
Plumbing and assembly for a pressure tank
Diy pressure pot for resin casting with test casting
DIY !! Making an powerful pressure washer & home-made BUILD
How to build a pressure or soft washing truck.
How To Build a Water Pressure Rocket With a Parachute
$3000 Budget Pressure Washing Trailer Build
Slow Air-pressure Build-up Rate | ELITE TRUCK DRIVING ACADEMY | 2022 | Brampton ON
HOW TO BUILD A PRESSURE WASHING TRAILER $500-$1000 A DAY
How to build DIY vacuum and pressure chamber at home
How To Adjust a Pressure Switch
How To Fix Your Low Water Pressure Problem
DIY: How to build Pressure Vessels with Reinforcement for Water Rockets
DIY Pressure Pot for resin casting
Reasons your Instant Pot WON'T Come to Pressure--And how to fix it!
Комментарии