filmov
tv
Coat ANYTHING in METAL: Magnetron Sputtering Machine Build
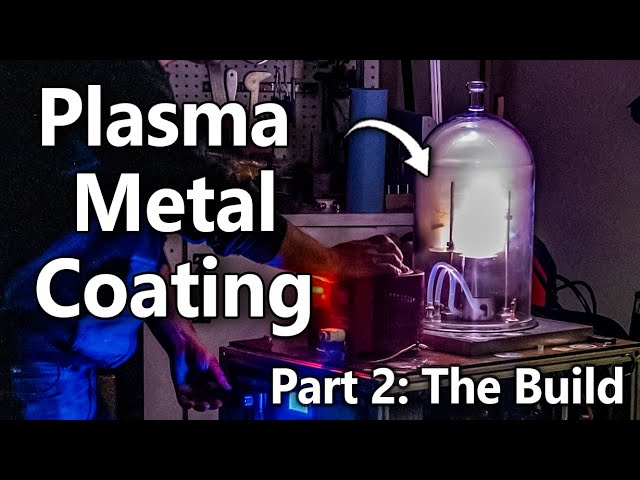
Показать описание
__________________________________________________________________________
This machine, is as close to magic as we've come as a species. It takes a sheet of metal, turns it into plasma and then can coat literally anything in that metal. Today we discuss how we built this incredible machine!
Ben's amazing videos:
________________________________________________________________
Chapters:
0:00 Intro
3:33 Sourcing materials
4:30 Cart
6:20 Base PLate
7:45 Choosing vacuum materials
10:40 Baffle
13:20 Sputter Head
17:20 Rotary Couplings
19:11 High Current Feedthrough
20:34 Gas Flow Valves
21:40 Sponsor
22:36 Next Time Sneak Peek
____________________________________________________________________
Support the show and future projects:
______________________________________________________
Our Social Media Pages:
_____________________________________________________
This machine, is as close to magic as we've come as a species. It takes a sheet of metal, turns it into plasma and then can coat literally anything in that metal. Today we discuss how we built this incredible machine!
Ben's amazing videos:
________________________________________________________________
Chapters:
0:00 Intro
3:33 Sourcing materials
4:30 Cart
6:20 Base PLate
7:45 Choosing vacuum materials
10:40 Baffle
13:20 Sputter Head
17:20 Rotary Couplings
19:11 High Current Feedthrough
20:34 Gas Flow Valves
21:40 Sponsor
22:36 Next Time Sneak Peek
____________________________________________________________________
Support the show and future projects:
______________________________________________________
Our Social Media Pages:
_____________________________________________________
Coat ANYTHING in METAL: Magnetron Sputtering Machine Build
Coat ANYTHING in Metal with Plasma!
My First Successful Metal Coating Machine - Magnetron Sputtering
METAL COATING by PLASMA Bombardment - Magnetron Sputtering
Breaking Down My Magnetron Design - DIY Metal Coating
Plasma Metal Coating... In a Jam Jar
Magnetron sputtering coating machine for metal coatings
METAL in MICROWAVE Oven Is NOT That Dangerous
hybrid vacuum PVD magnetron sputtering multi arc deposition for applying harden protective coatings
Sputtering: What is it and how does sputter deposition work?
ZHENHUA magnetron sputtering coating machine for stainless steel product
Metal Coating using PLASMA (Part 1 - How it works)
Inside the vacuum chamber during magnetron sputtering PVD coating
Three target magnetron sputtering coating
ZEIT Magnetron Sputtering Coating Machine
PVD Magnetron Sputtering Coating Machine For Plastic Parts
PVD Coating Animation
Magnetron sputtering system with single target and fiber winding
Magnetron Sputtering Coating System for Preparing thin films
Magnetron Sputtering Cathode for PVD Coating Sputtering Source катод для магентронного напыления...
Magnetron Sputtering PVD coating for Dark Black color
#1 Making a Sputtering Magnetron
Cátodo De Magnetrón Para Revestimiento De PVD/Magnetronkathode/Magnetron Sputtering Cathodes Test
Multi Arc+MF+DC Plane Magnetron Sputtering PVD Coating Machine
Комментарии