filmov
tv
Converting Engineering to True stress-strain curve Tutorial
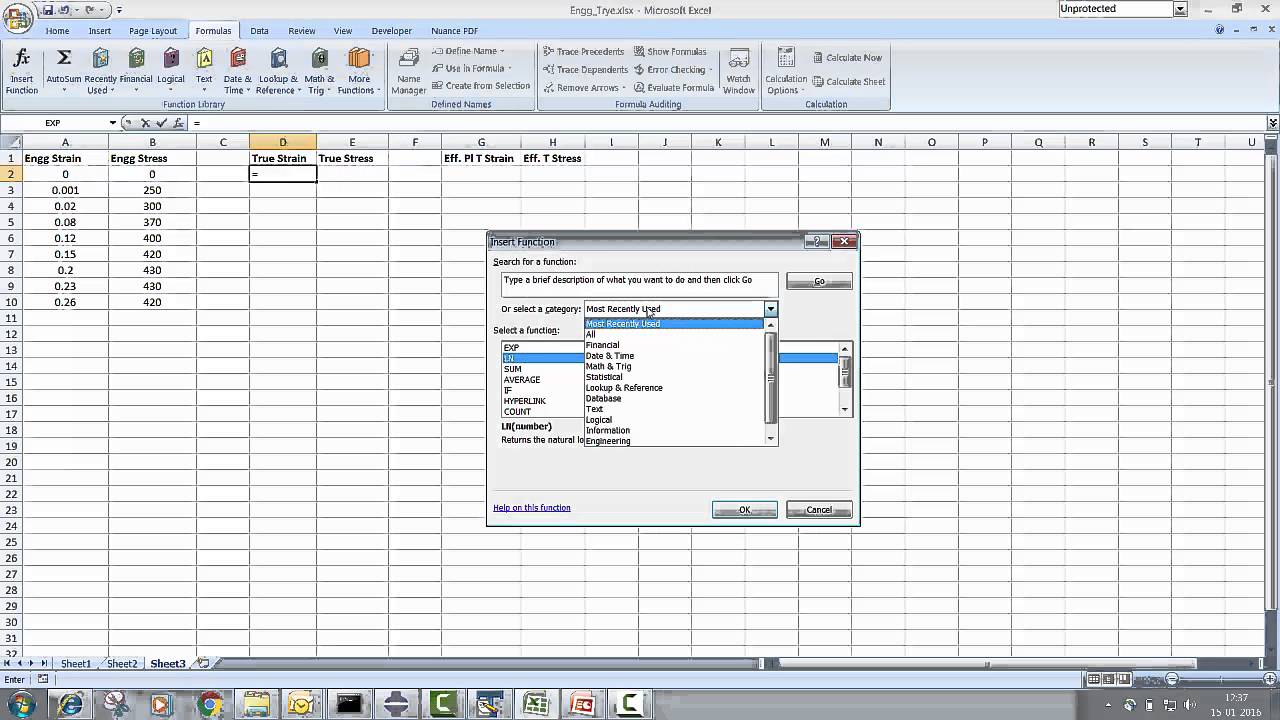
Показать описание
This video describes on how to convert Engineering stress – strain curve to True stress-strain curve. For FE model for accounting material non-linearity we need to feed True stress-strain curve with minor modification to effective plastic strain. Formulas for conversion along with Excel sheet use has been demonstrated to carry out this exercise quick error free and this video also shows copying this data to AbaqusCAE window and editing input Textpad file.
Converting Engineering to True stress-strain curve Tutorial
Abaqus Utility:Converting Engineering to True stress-strain curve Tutorial
Understanding True Stress and True Strain
Converting Engineering to True stress-strain curve using Excel and Abaqus
Conversion of Stress-Strain from Engineering to True values
SolidThinking Compose #4: Convert Engineering to True Stress Strain
#33 ABAQUS Tutorial: Metal Plasticity | Engineering to True Stress-Strain Conversion
True stress and Strain and Engineered Stress and Strain - Worked example.
Converting Engineering stress-strain to True stress-strain curve to Plastic strain:Tutorial
Tutorial: Two methods to convert the engineering stress strain curve to the true stress strain curve
Relationship between Engineering vs. True Stress-Strain Diagram
ABAQUS tutorial EP002 | How to make True stress - True strain preparation using ABAQUS
Difference between Engineering Stress-Strain vs True Stress-Strain Response
Metals 101-8 Engineering Stress vs True Stress
Tensile test: Engineering and true stress vs. engineering, true and plastic strain curves
True Stress-Strain Vs Engineering Stress-Strain || How to use Tension Test data for ABAQUS?
Engineered Stress and Strain versus True Stress and Strain
Convert Engineering Stress & Strain to True Stress and Strain
Derive True Stress and strain
Combining True Stress and Strain Data Set for ENGR270 Lab 4
Mechanisms of Deformation & True Stress-Strain
True stress and True Strain
True stress, true strain and work hardening
TRUE Strain vs. ENGINEERING Strain in 2 Minutes!
Комментарии