filmov
tv
CAD vs Slicer. What to rely on when mass producing a part with 3D Printing.
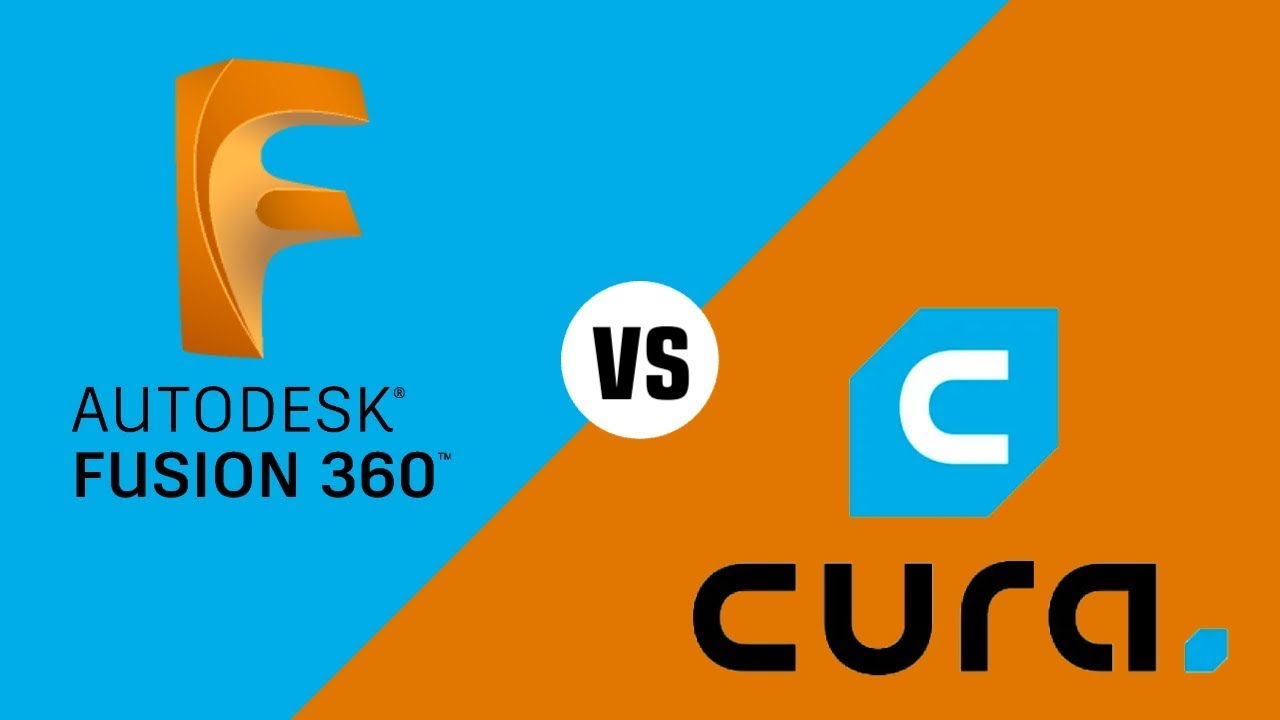
Показать описание
Discover the benefits of using CAD instead of a slicer for 3D printed parts engineering in mass production. Learn how CAD gives you more control, allowing you to optimize the manufacturing process and achieve the perfect result. Don't forget to like, share, and subscribe for more expert 3D printing tips!
#additivemanufacturing #3dprintfarm #productdesign
🔗 IMPORTANT LINKS 🔗
About Slant 3D
🏭 High-Volume 3D Printing: Scalability Meets Flexibility
Slant 3D's Large-Scale 3D Print Farms utilize 1000's of FDM 3D printers working 24/7 to offer limitless scalability and unparalleled flexibility. Whether it's 100 or 100,000 parts, our system can handle it reliably, while still allowing for real-time design updates, ensuring products evolve with the times. This adaptability is key in today's fast-paced world.
🌿 Sustainable Manufacturing: Eco-Friendly Efficiency
Embrace a system that drastically reduces carbon emissions by eliminating carbon-intensive steps in the supply chain, such as global shipping and warehousing. Our approach minimizes this footprint, offering a more sustainable manufacturing option.
⚙️ Digital Warehouses: Parts On-Demand
Think of print farms as a "Digital Warehouse", meaning we can store your parts digitally on a server rather than physically on a shelf. parts are available on-demand, reducing the need for extensive physical inventory.
Produced by Slant Media
*As an Amazon Associate, I earn commission from qualifying purchases.*
Produced by Slant Media
#additivemanufacturing #3dprintfarm #productdesign
🔗 IMPORTANT LINKS 🔗
About Slant 3D
🏭 High-Volume 3D Printing: Scalability Meets Flexibility
Slant 3D's Large-Scale 3D Print Farms utilize 1000's of FDM 3D printers working 24/7 to offer limitless scalability and unparalleled flexibility. Whether it's 100 or 100,000 parts, our system can handle it reliably, while still allowing for real-time design updates, ensuring products evolve with the times. This adaptability is key in today's fast-paced world.
🌿 Sustainable Manufacturing: Eco-Friendly Efficiency
Embrace a system that drastically reduces carbon emissions by eliminating carbon-intensive steps in the supply chain, such as global shipping and warehousing. Our approach minimizes this footprint, offering a more sustainable manufacturing option.
⚙️ Digital Warehouses: Parts On-Demand
Think of print farms as a "Digital Warehouse", meaning we can store your parts digitally on a server rather than physically on a shelf. parts are available on-demand, reducing the need for extensive physical inventory.
Produced by Slant Media
*As an Amazon Associate, I earn commission from qualifying purchases.*
Produced by Slant Media
Комментарии