filmov
tv
A Cable Robot 3D-Printer
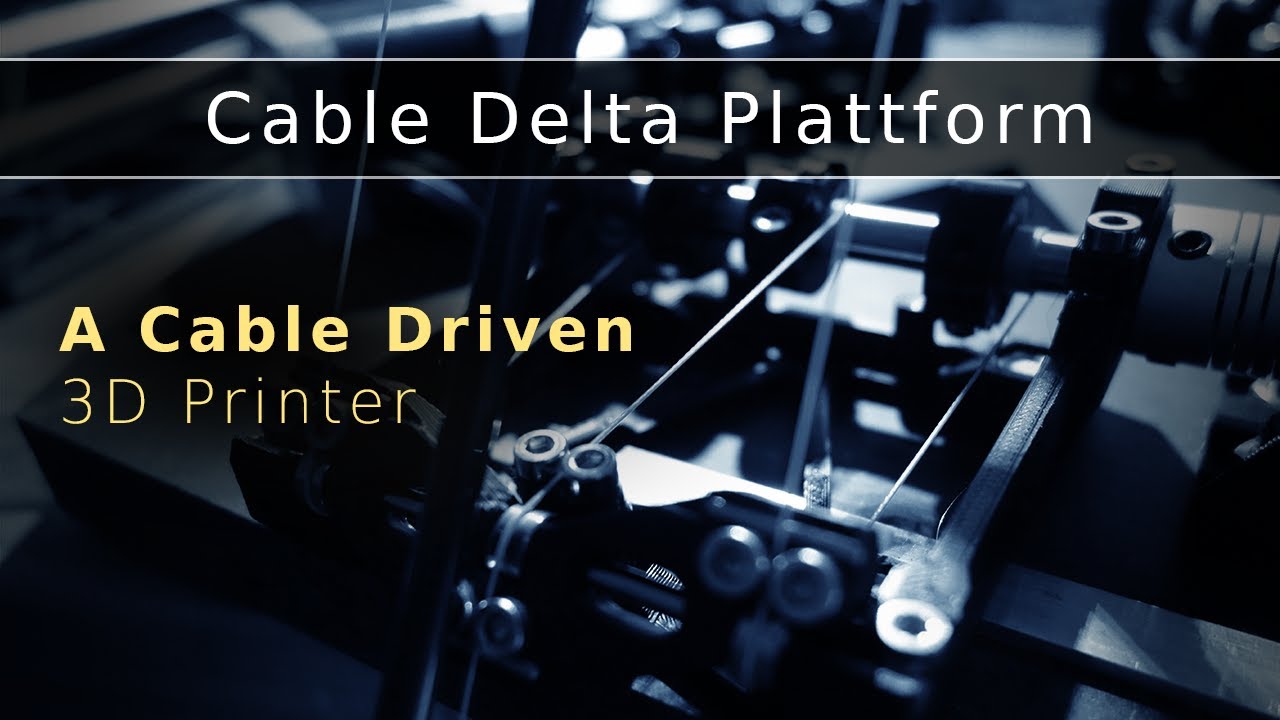
Показать описание
The video presents a cable driven 3D-Printer, based on the parallel kinematic delta plattform. The machine uses dyneema fishing line as cables and a custom kinematic model running on the 'smoothieboard' printer board.
Carbon fiber preloading rods are used to keep the cables under tension, providing the necessary stiffness and allowing for rapid accelartion.
The parallel kinematic design has potential benefits for large workspaces.
Carbon fiber preloading rods are used to keep the cables under tension, providing the necessary stiffness and allowing for rapid accelartion.
The parallel kinematic design has potential benefits for large workspaces.
A Cable Robot 3D-Printer
On-site 3D printing using cable-driven robots
3D-Printed LIMS2-AMBIDEX Style Robotic Joint
Hang Printer - Clerck Cable Driven Hanging 3D printer overview - Chris's Basement
Flexible Motion of a Cable-Driven Parallel Robot on 3D Curved Surface
Marionette: another new 3D printer kinematic - progress.
Extreme Fast Cable-Driven Parallel Robot
Reconfigurable Cable Driven Parallel Robot Test 1
Food Container STEM Robot - Build
Cable-driven Parallel Robot for 3D Structure Printing
PIX 3D Printed Chassis Platform -- Robot Platform
Vivedino Formbot Raptor 2.0 Unboxing and Build
Cable-Driven Parallel Robot With Articulated Reconfigurable Moving Platform for Schönflies Motions
3D Printed RC Crane - DIY
$26 Million Robot Arm: Real 3D Printed Products
7 Cool 3D Printed Things To Upgrade Your Desk / Gaming Setup - Printed on the Anycubic Kobra 2 Pro
Which 3D Scanner is Best for 3D Printing?
3D Printing is SLOW?| FLSUN V400
Best 3D Printers of 2023! A Guide for Beginners, Budgets, & More!
Hexbot all in one Robot Arm Desktop 3D printer Laser engraver and everything in between
TOP 10 BEST 3D PRINTERS 2023
Bizer CTC 3D Printer Unboxing
How to Build a Cool & Cheap 3D Printed Mini Drone
Robo 3D R1+ 3D Printer - Review - Chris's Basement
Комментарии