filmov
tv
Inspecting some HBM ER25 Collets and trying out some bue nano inserts
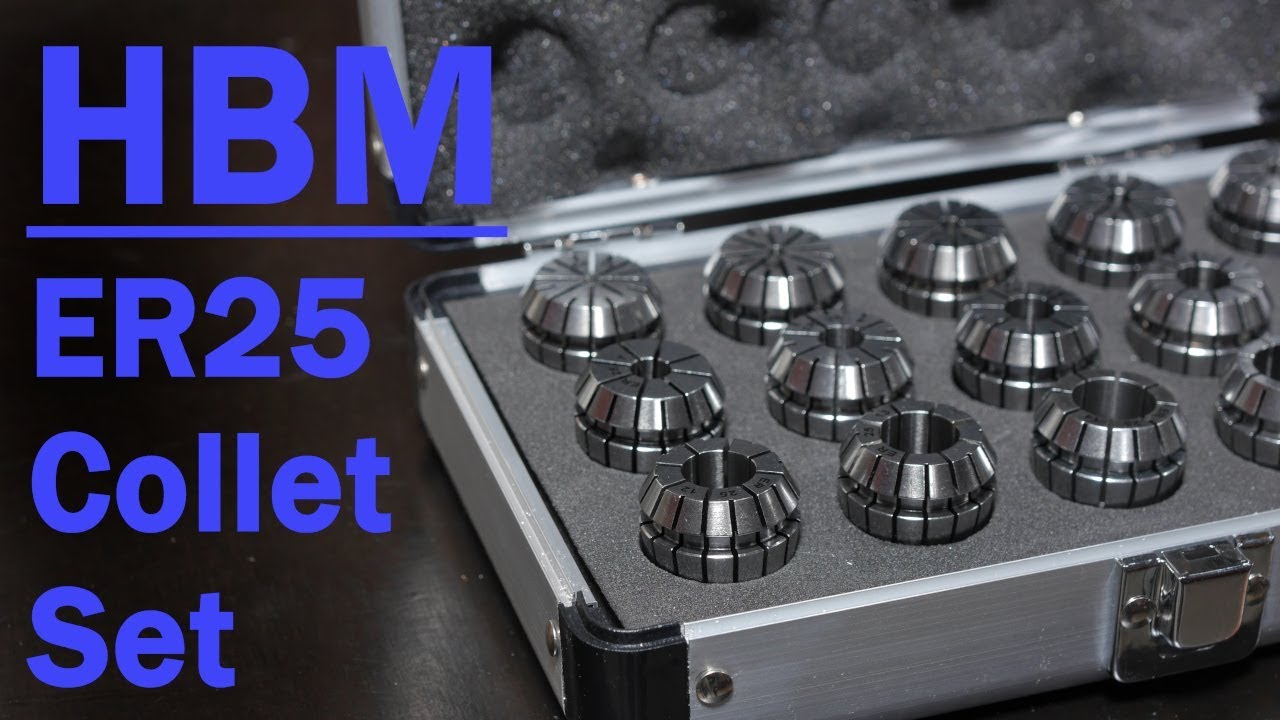
Показать описание
To celebrate my 3 year channel birthday I bought myself a set of ER25 collets from Dutch reseller HBM. In this video I try to find out if they are good enough to keep, for when I start machining my own collet chuck for on my vintage Karger lathe. Oh, and I also start testing some blue nano ccmt inserts in this video.
FYI: I am trying to make a little money for my youtube hobby through the Banggood affiliates program. Follow the link below, buy something you NEED and I'll earn some commission. Doesn’t cost you anything extra. You're basically taking money out of Banggood's pockets and putting it in mine :)
FYI: I am trying to make a little money for my youtube hobby through the Banggood affiliates program. Follow the link below, buy something you NEED and I'll earn some commission. Doesn’t cost you anything extra. You're basically taking money out of Banggood's pockets and putting it in mine :)
Inspecting some HBM ER25 Collets and trying out some bue nano inserts
ER25 collet
ER Collets | 5 Things to Know for Beginners
Fitting the ER25 collet chuck from RDG on my ELS equipped Myford S7
ERG Collets
Rego-Fix ER25 Collet Set ø2-16mm
BBT-ER tool holders BT40-ER32 Collets chucks ER25 ER32 collets tool holder OLICNC
Collet ER 25 ColletER 25 Collet Chuck Arbor Colet Milling ER25 N21-005
ER25 Patronbefogó a HBM 450 kisesztergán!
Banggood ER25 HOLDER Chuck MT3 with collet
DIN69893 High Precision HSK63F ER25 ER32 Collet Chuck
spantang HSPF 40
12 sided ER40 collet chuck runout
Arbor BT30 ER25 100L Collet ER25 Collet Chuck ER25 Holder Tool Milling
B21-068 COLLET ER25 13 CHUCK ARBOR MILLING
Collet Nut ER11A Nut ER16 Nut ER20 Nut ER25 Nut ER32 Nut ER40 inpertek TeknikLOAK
Robust ER-25 Collet Handle Review
B14-086 ARBOR MTB2 ER25 ARBOR BEKAS MTB2 HOLDER TOOL MILLING MULUS MT2
Best High Precise MT2 ER25 M10 collet chuck handle Morse milling chuck handle
Home made ER40 Collet Chuck test
Tool Review protractor and ER32 collets
Smart Collet Pullers Collets
ER Collets and Collet Chucks
Frezen van een snelwisselbeitelhouder deel-1
Комментарии