filmov
tv
Mini Lathe compound angle adjustment modification
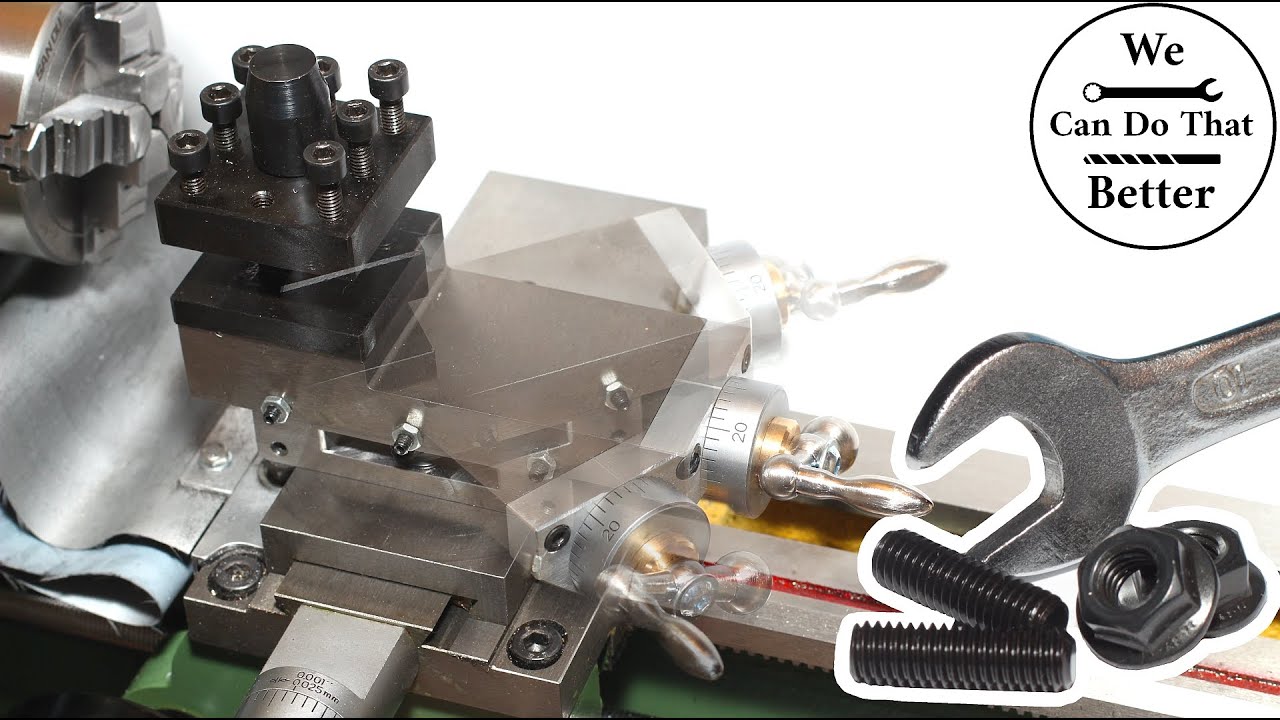
Показать описание
My solution for the annoying mini lathe compound slide angle adjustment problem.
Changing the compound slides angle on the mini lathe is incredible time-consuming and annoying. You have to wind the compound slide back and forth to reach the screws underneath the top of the compound slide.
There are some ways out here to get rid of this problem, but none I found satisfying enough. Some just drilled holes in the top part of the compound, to reach the screws at a certain position through the compound, some clamped from the side and lose the little rest of rigidity the compound has, some built a complicated lever mechanism.
I wanted to keep things simple (which does not mean, it's fast to built) and decided to copy "real" lathes and go for a bolt and nuts instead of screws for clamping and mill slots into the compounds base for reaching the nuts from the side.
This way I can clamp the compound in any position easily and maintain hopefully as much rigidity as possible.
Keep in mind, due to very limited resources, I have to improvise a lot and go unconvenient ways which may upset some of the "real machinists" out here.
Hope - with some creativity - in the end come to good resoults anyway.
Hope you enjoy. Feel free to like and subscribe to the channel. Thank you!
Changing the compound slides angle on the mini lathe is incredible time-consuming and annoying. You have to wind the compound slide back and forth to reach the screws underneath the top of the compound slide.
There are some ways out here to get rid of this problem, but none I found satisfying enough. Some just drilled holes in the top part of the compound, to reach the screws at a certain position through the compound, some clamped from the side and lose the little rest of rigidity the compound has, some built a complicated lever mechanism.
I wanted to keep things simple (which does not mean, it's fast to built) and decided to copy "real" lathes and go for a bolt and nuts instead of screws for clamping and mill slots into the compounds base for reaching the nuts from the side.
This way I can clamp the compound in any position easily and maintain hopefully as much rigidity as possible.
Keep in mind, due to very limited resources, I have to improvise a lot and go unconvenient ways which may upset some of the "real machinists" out here.
Hope - with some creativity - in the end come to good resoults anyway.
Hope you enjoy. Feel free to like and subscribe to the channel. Thank you!
Комментарии