filmov
tv
Only 1 in 100 Shops Would Find This Problem
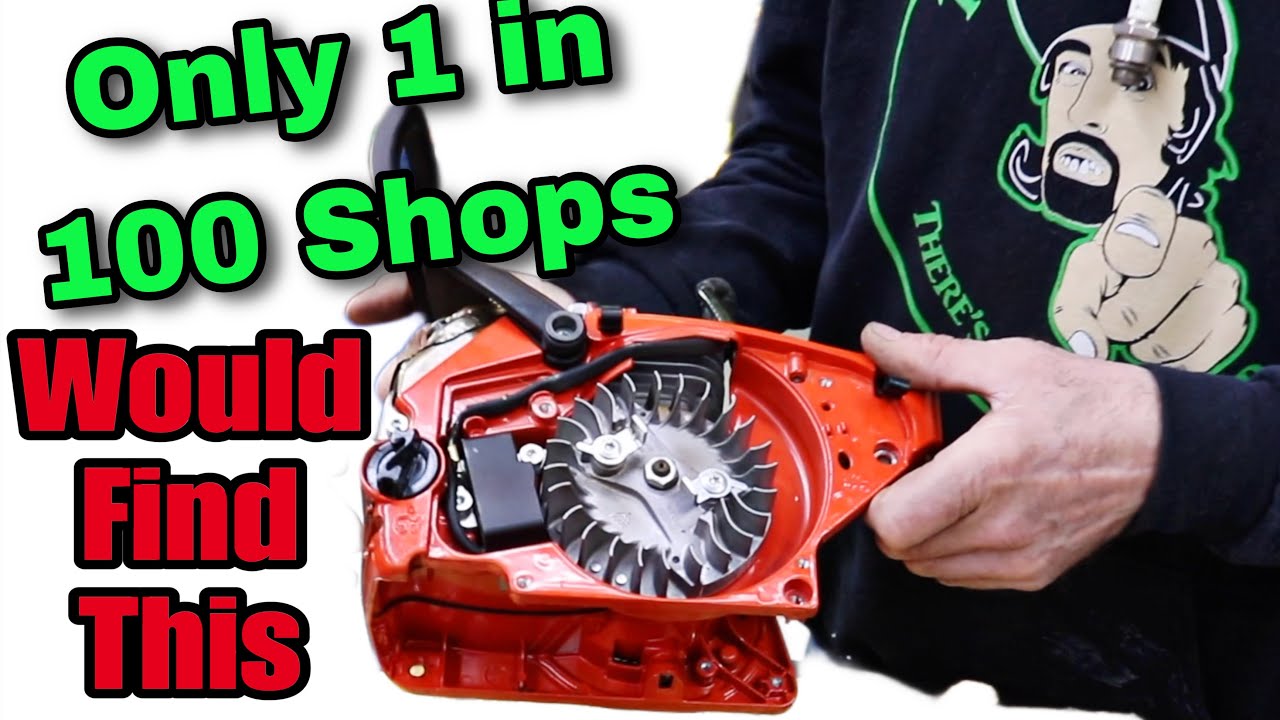
Показать описание
Taryl's got more outside-the-box problem solving when working on these here small engines. Not very many shops at all would go to this length to find the issue with this almost-new chainsaw. What's going on with it? Why is it bogging out? Taryl's got the answers in another informative how-to video. Now There's Your Dinner!!
Subscribe Today for all the latest videos! (Click 'Subscribe' on this channel!)
Get Your Parts From
#tarylfixesall #grassratsgarage #dolmar #chainsaw #troubleshooting #fix #repair #howto #diagnose #troubleshoot #smallenginerepair #mechanic
Subscribe Today for all the latest videos! (Click 'Subscribe' on this channel!)
Get Your Parts From
#tarylfixesall #grassratsgarage #dolmar #chainsaw #troubleshooting #fix #repair #howto #diagnose #troubleshoot #smallenginerepair #mechanic
Only 1 in 100 Shops Would Find This Problem
WE SPENT $100 AT OUR FAVORITE STORES SHOPPING CHALLENGE 🤑🛍 @HallieOnStage114 @agset211
Just Inazuma's Regular Souvenir Shop
Minecraft but there's Only One Shop Block
Products starting from just Rs.5/- 😯 #shopsy #shopsybyflipkart #shopping #shorts
a tokyo guide to shopping, best gachapon shops and convenience store food
Shop with me for *PURPLE ONLY* Mystery Toys Challenge!!😱🦄☂️🙆🏻♀️🍇💜 *JACKPOT!!🫢* | Rhia Official♡...
only buying PINK items at ulta *no budget SHOPPING SPREE!!!*
✨GLITTER ONLY✨ FIDGET SHOPPING CHALLENGE! 💖🌟🪄💍
Shop Largest Hair Topper Only on 1hs.com | Made with 100% Human Hair |
BUYING ONLY CINNAMOROLL AT MINISO! Shop with Me No Budget Challenge! #sanrio #miniso #shopping
DOG MAN | Official Trailer
Bootcut lower just in ₹350 #trendingreels #bootcut #shopping #bestlower
I visited 1 of only 11 Razer gaming stores! @razer
UNDER THE SEA ONLY FIDGET SHOPPING CHALLENGE 🐬🦀🐡
NEW 100 REROLL CODE JUST DROPPED in Anime Last Stand (EXPIRES SOON)
BUYING ONLY SANRIO AT MINISO! (Shop with me, Unlimited Budget #miniso)
Formal pants just 100rs Hill Road bandra #subscribe #shorts #shopping #pant #fashion
Grocery shopping with only $100 didn’t end well
TURQUOISE ONLY FIDGET SHOPPING CHALLENGE 👗🧼🧤
Shop with me for *RED ONLY* Mystery Toys Challenge!!😱🍓🎈🌹⁉️ *JACKPOT!!😍* | Rhia Official♡...
I Built a Gaming Setup With ONLY Tiktok Shop…
soft#toys#shop#sarojini#nagar#market#delhi#only#just₹100💃💃😊
MYTHICAL CREATURES ONLY FIDGET, SLIME, & SQUISHMALLOW SHOPPING CHALLENGE! 🦄🐲🧜🏼♀️✨...
Комментарии