filmov
tv
Diamond Insert Turning Acrylic Rod in my small cnc lathe. Includes cuts with carbide insert
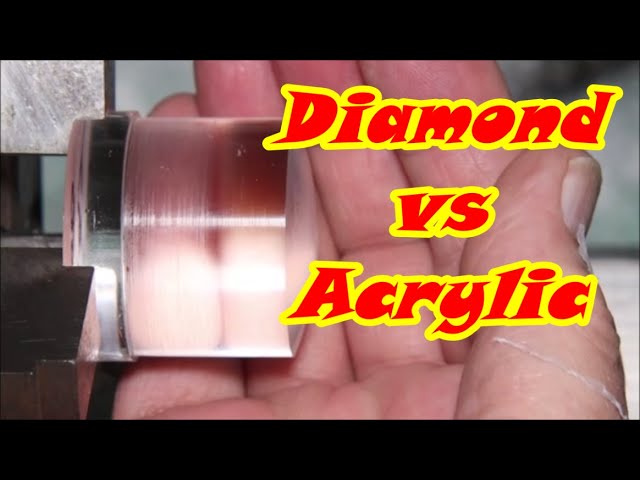
Показать описание
Diamond turning of acrylic.
I have not used Diamond inserts before, which will probably be obvious to folks that have! Changing the lathe gearing to reach 4000 rpm, using 40ø acrylic, I try a few options. 40ø at 4000 rpm is still only giving a surface speed of 500m/min and the recommended would be 1000m/min. I tried to get 80ø but it was just too expensive.
I have not used Diamond inserts before, which will probably be obvious to folks that have! Changing the lathe gearing to reach 4000 rpm, using 40ø acrylic, I try a few options. 40ø at 4000 rpm is still only giving a surface speed of 500m/min and the recommended would be 1000m/min. I tried to get 80ø but it was just too expensive.
Diamond Insert Turning Acrylic Rod in my small cnc lathe. Includes cuts with carbide insert
Machining acrylic rod
Diamond turning a small acrylic dome.
lathe turning, threading n cutting on acrylic rod. rotating at 750 rpm.
CNC Machining Acrylic parts
Diamond turning an acrylic disc 2
Diamond turning an acrylic dome
#acrylic #cnc #machining #turning #9723780036 @cnclathe
Single Point Diamond Turning: Direct cutting on plastic and steel
The most satisfying machining - Diamond turning plastic
Precision Machining——Diamond Ultra Precision Tools
PCD Diamond Insert Part1. Turning Aluminium with Carbide and Diamond inserts.
PCD Diamond Insert Part 3. Turning Aluminium 6061, with Diamond insert at 3900rpm,
Monocrystalline Diamond Tools
Diamond turning a flat acrylic disc
Double-head synchronous processing of acrylic pen holder machining lathe source strength manufacture
Aluminum diamond turning
Machining lenses for our spike lights from Acrylic round bar
Diamond turning sine waves into acrylic
WORLDIA ManaNova Universal PCD Insert - DCGW
Milling the top flat and the center out of an acrylic rod.
Turning Acrylic|Gang Type CNC Lathe Machine
CNC lathe processing acrylic example
polishing acrylic rod/stick/tube automatically
Комментарии