filmov
tv
Handpowered Sawmill - Log to Timber with HandTools
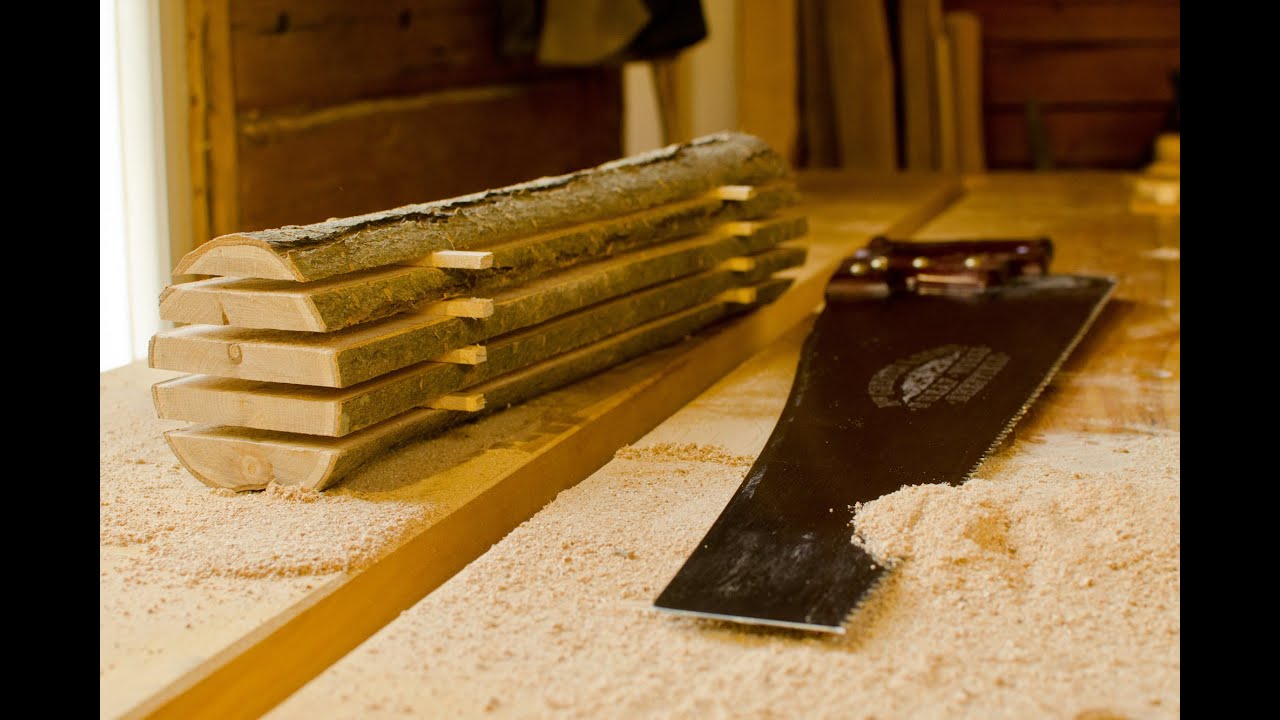
Показать описание
Cutting logs or branches into timber / lumber with handtools only in a small apartment workshop. Possible? Yes it is! No need for a saw mill, machines or other high-tech. Just a Ripcut Saw and some nice (not too big) logs or branches of your favourite wood.
For more INFORMATION, please open the full description!
------------------------------------
- Can you explain this method in words?
First it is important to mark accurately. The shown method will help to cut straight and flat, instead of 'twisted'.
Second it is not easy to cut straight along the mark, specially while cutting with the grain or when cutting irregular wood. That is why, i cut on the mark only on the side towards me. Then, when the saw is about 45° i turn the wood. Now i guide the back of the saw (the side towards me) along the mark, while the other end is guided by the already cutted ‘rail’. You can see in the video that it goes amazingly well.
- Hungarian Lilac, where did you get this special wood from?
I found it in a town park after the town-workers maintained the trees and bushes. This wood would have gone to be burned and they allowed me to take all what i wanted :-)
- What saw are you using?
It is a Ripcut Saw with 4,5 TPI. I sometimes also use my self-made Bucksaw with a similar blade. But for intensive cutting i prefer this kind of handsaw.
- Is it better to dry the wood before cutting or afterwards?
All in all, it is better to cut it fresh!
In some cases there might be an advantage to cut it after drying:
In the case of this video i did not want to cut the Lilac before knowing what i'll do out of it and so know how thick to cut it. I have so little of it, that i wanted to make less waste as possible. So drying before cutting was the only option. There comes the problem of checks. To avoid them it can be useful to keep the bark and wax the ends (if no wax available, the ends can be covered with plastic. Make sure to turn it regularly and remove when it is not 'sweating' anymore). This avoid checks, but might not work out with any wood.
I used this method also to get wood for my screws out of branches. It is possible to get roundwood dry with the heart inside and without checks. What is usually kept as not possible.
It is bit work and takes lots of time, but in some cases it might be worth to try it out.
For more INFORMATION, please open the full description!
------------------------------------
- Can you explain this method in words?
First it is important to mark accurately. The shown method will help to cut straight and flat, instead of 'twisted'.
Second it is not easy to cut straight along the mark, specially while cutting with the grain or when cutting irregular wood. That is why, i cut on the mark only on the side towards me. Then, when the saw is about 45° i turn the wood. Now i guide the back of the saw (the side towards me) along the mark, while the other end is guided by the already cutted ‘rail’. You can see in the video that it goes amazingly well.
- Hungarian Lilac, where did you get this special wood from?
I found it in a town park after the town-workers maintained the trees and bushes. This wood would have gone to be burned and they allowed me to take all what i wanted :-)
- What saw are you using?
It is a Ripcut Saw with 4,5 TPI. I sometimes also use my self-made Bucksaw with a similar blade. But for intensive cutting i prefer this kind of handsaw.
- Is it better to dry the wood before cutting or afterwards?
All in all, it is better to cut it fresh!
In some cases there might be an advantage to cut it after drying:
In the case of this video i did not want to cut the Lilac before knowing what i'll do out of it and so know how thick to cut it. I have so little of it, that i wanted to make less waste as possible. So drying before cutting was the only option. There comes the problem of checks. To avoid them it can be useful to keep the bark and wax the ends (if no wax available, the ends can be covered with plastic. Make sure to turn it regularly and remove when it is not 'sweating' anymore). This avoid checks, but might not work out with any wood.
I used this method also to get wood for my screws out of branches. It is possible to get roundwood dry with the heart inside and without checks. What is usually kept as not possible.
It is bit work and takes lots of time, but in some cases it might be worth to try it out.
Комментарии