filmov
tv
Calculating EOQ - Economic Order Quantity (Inventory Costs & Purchasing Costs)
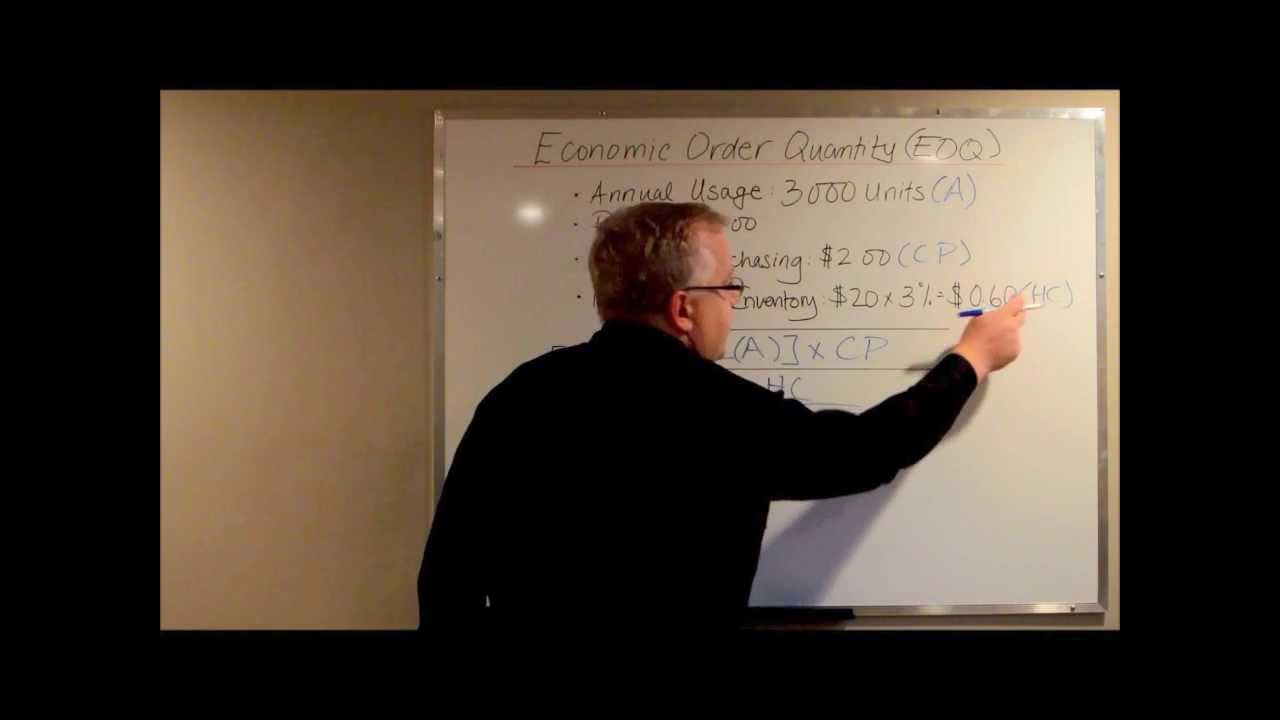
Показать описание
This video explains how to calculate economic order quantity using the time-tested Wilson EOQ formula.
The video provides a step-by-step process to defining the economic order quantity for any company. It takes into consideration the company's annual or yearly consumption, the price it pays for each unit it purchases for its inventory, the cost to make that purchase and finally, the company's costs to hold inventory on a monthly basis.
Determining the annual or yearly consumption is fairly straightforward. Simply take a total of all the inventory of a given part used in a year. Next, take the amount your company pays for that part or raw material.
Determining your company's costs to purchase doesn't merely involve totaling your total volume multiplied by price. Instead, it's more about defining what it costs your company to make a purchase. How much does it cost your company to purchase from a vendor?
Your costs to purchase include time spent to approve and sign purchase requisitions. It also includes the time spent placing that order and sending it to your vendor. Next, the costs of inspecting the order are accounted for and finally, the costs of paying your vendor.
The Wilson EOQ formula involves doubling your yearly consumption total and multiplying it by your company's cost to purchase. This amount is then divided by the sum of the raw material or part's price multiplied by its inventory holding costs.
The Wilson EOQ formula is an excellent tool for making sure your company doesn't buy too much or too little.
Комментарии