filmov
tv
Compliant Mechanisms that Roll Like GEARS!?! -- #VeritasiumContest
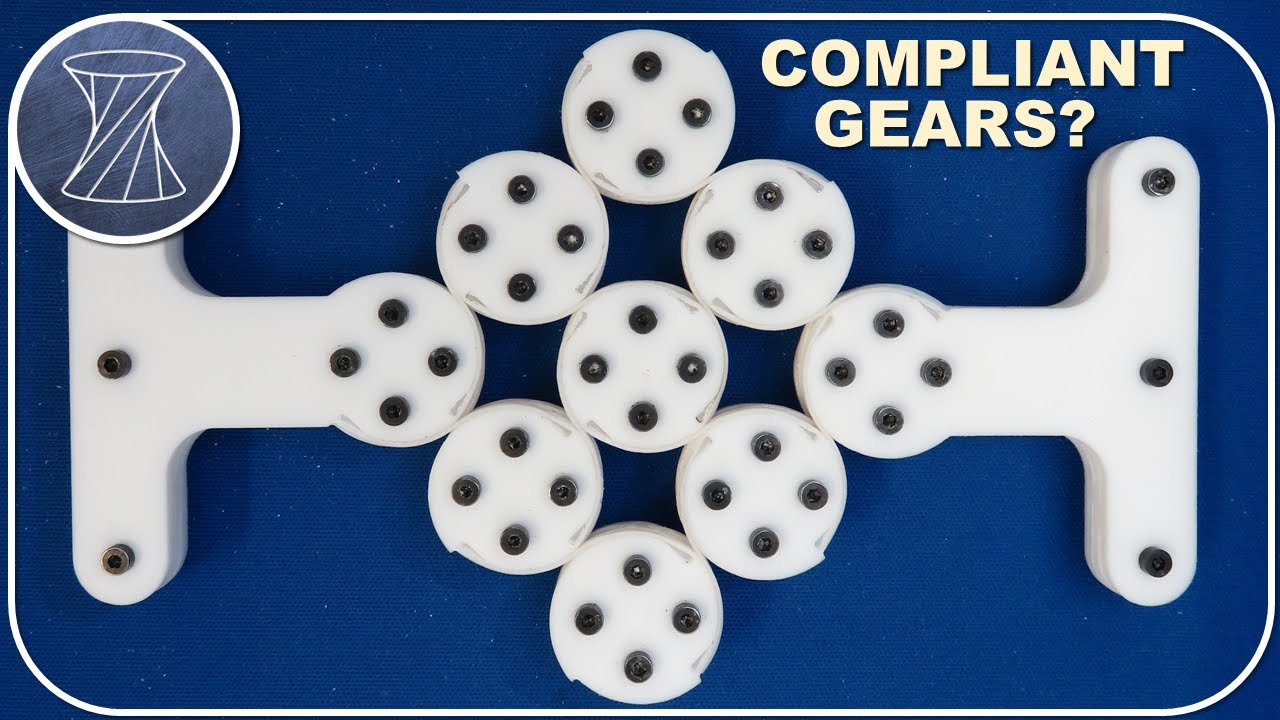
Показать описание
#VeritasiumContest
Since the prize money is coming from a UCLA professor who lost a physics bet to Derek from Veritasium, this is my attempt as a fellow UCLA professor to redeem my university’s reputation.
This video is about how compliant rolling-contact joints can be used to counter intuitively create compliant lattices of gears. Compliant rolling-contact joints consist of crisscrossing flexures that are deformed around cams. They achieve large ranges of deformation without increasing in stress and achieve near zero stiffness about the desired axis of rotation while maintaining high stiffness in all other directions. 2D and 3D lattices of many shapes can be designed.
My work pertaining to these lattices, which are called ‘Compliant Rolling-contact Architected Materials’ (i.e., CRAMs), is previously published in the journal Nature Communications at the following link:
If you are interested in learning more about compliant mechanisms in general, check out my YouTube Channel, “The FACTs of Mechanical Design”
and be sure to check out Veritasium’s video on the topic as well:
Acknowledge: This work would not have been possible without the help of my students, Luke Shaw, Samira Chizari, Matt Dotson, and Adam Song!
Donate to help support my channel:
If you’d like to make a one-time donation, you can use the following link:
Thank you for your support! It is much appreciated and helps enable me to make more content.
Disclaimer: Responsibility for the content of this video is my own. The University of California, Los Angeles is not involved with this channel nor does it endorse its content.
Since the prize money is coming from a UCLA professor who lost a physics bet to Derek from Veritasium, this is my attempt as a fellow UCLA professor to redeem my university’s reputation.
This video is about how compliant rolling-contact joints can be used to counter intuitively create compliant lattices of gears. Compliant rolling-contact joints consist of crisscrossing flexures that are deformed around cams. They achieve large ranges of deformation without increasing in stress and achieve near zero stiffness about the desired axis of rotation while maintaining high stiffness in all other directions. 2D and 3D lattices of many shapes can be designed.
My work pertaining to these lattices, which are called ‘Compliant Rolling-contact Architected Materials’ (i.e., CRAMs), is previously published in the journal Nature Communications at the following link:
If you are interested in learning more about compliant mechanisms in general, check out my YouTube Channel, “The FACTs of Mechanical Design”
and be sure to check out Veritasium’s video on the topic as well:
Acknowledge: This work would not have been possible without the help of my students, Luke Shaw, Samira Chizari, Matt Dotson, and Adam Song!
Donate to help support my channel:
If you’d like to make a one-time donation, you can use the following link:
Thank you for your support! It is much appreciated and helps enable me to make more content.
Disclaimer: Responsibility for the content of this video is my own. The University of California, Los Angeles is not involved with this channel nor does it endorse its content.
Комментарии