filmov
tv
How much extruder traction do we really need?
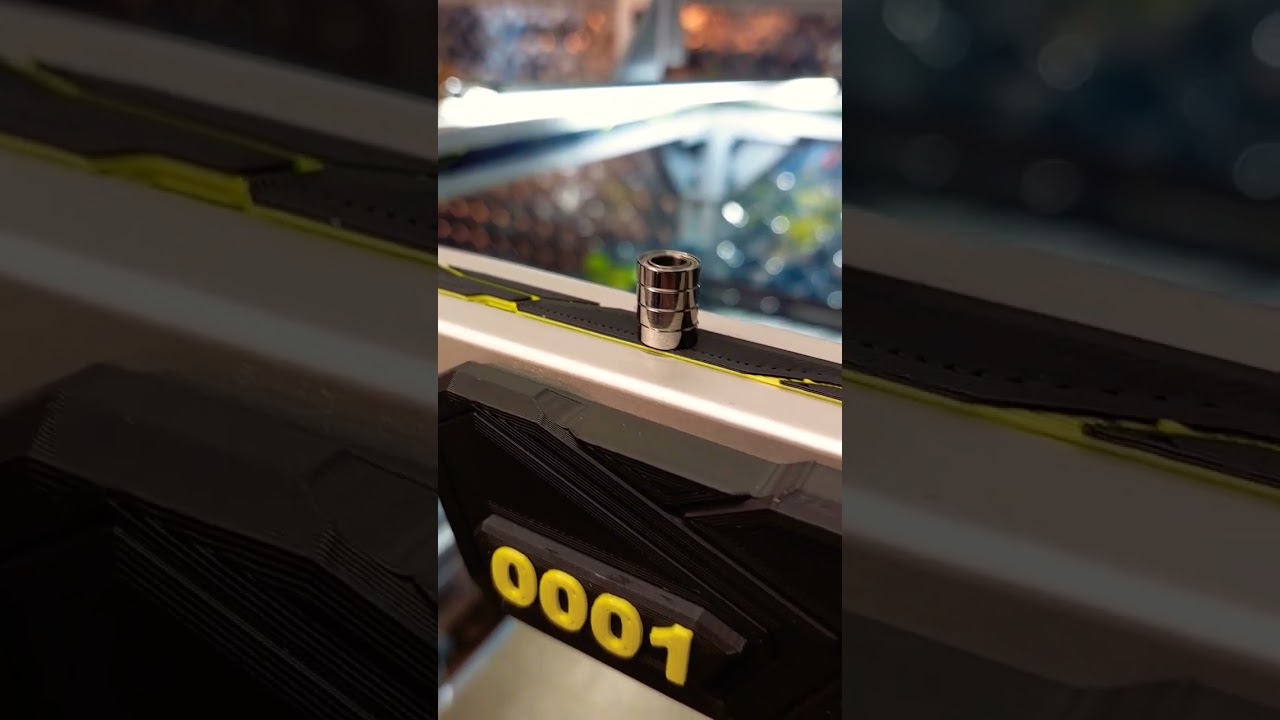
Показать описание
Idler hobb gear has an impact on extrusion consistency.
Do we REALLY need a second driven hobb gear in a direct drive extruder?
You want to learn and contribute to the HevORT project?
Do we REALLY need a second driven hobb gear in a direct drive extruder?
You want to learn and contribute to the HevORT project?
How much extruder traction do we really need?
Hevort with Mellow / cannon extruder , test printing with an LSD hot end
3d Printing Consumable Extruder
Cost effective 3D printer for granular materials screw extruder
Extruder dwell
Getting away from testing to do some actual printing feels good!
Cold end Traction extruder (belt driven extrusion), Part 1
Ender 3 Filament Feed Issue - Solved
Will this NEW extruder gear solve the issue?
Rolling Thread Extruder Pulling test
Extruder Arm Distance and Speed Adjustment/Test
Spiral extruder progress
Lightweight Nema 8 Direct drive Extruder Prototype for High flow Dragon hotend V1 #3dprinting #3d
Effect of extrusion FLOW RATE to the strength of 3D printed object
Choosing the Right Manufacturing Equipment for Aluminum Extrusion
Choosing the Right Manufacturing Equipment for Aluminum Extrusion
Revolutionizing 3D Printing: Prusa's Game-Changing Nextruder
Rolling Thread Extruder - 3dprinter original Extruder done with bearings thread mechanism prototype.
how to operate plastic pipe extruder ? hows the plastic tube extrusion machine running ?
small extruder with VDE-100 blade drive
Choosing the Right Manufacturing Equipment for Aluminum Extrusion
Small Extruder Three Roll Calender
Choosing the Right Manufacturing Equipment for Aluminum Extrusion
Testing 3DQF ABS
Комментарии