filmov
tv
The Anatomy of a Roll Forming Line: Complete Process from Coil to Crate
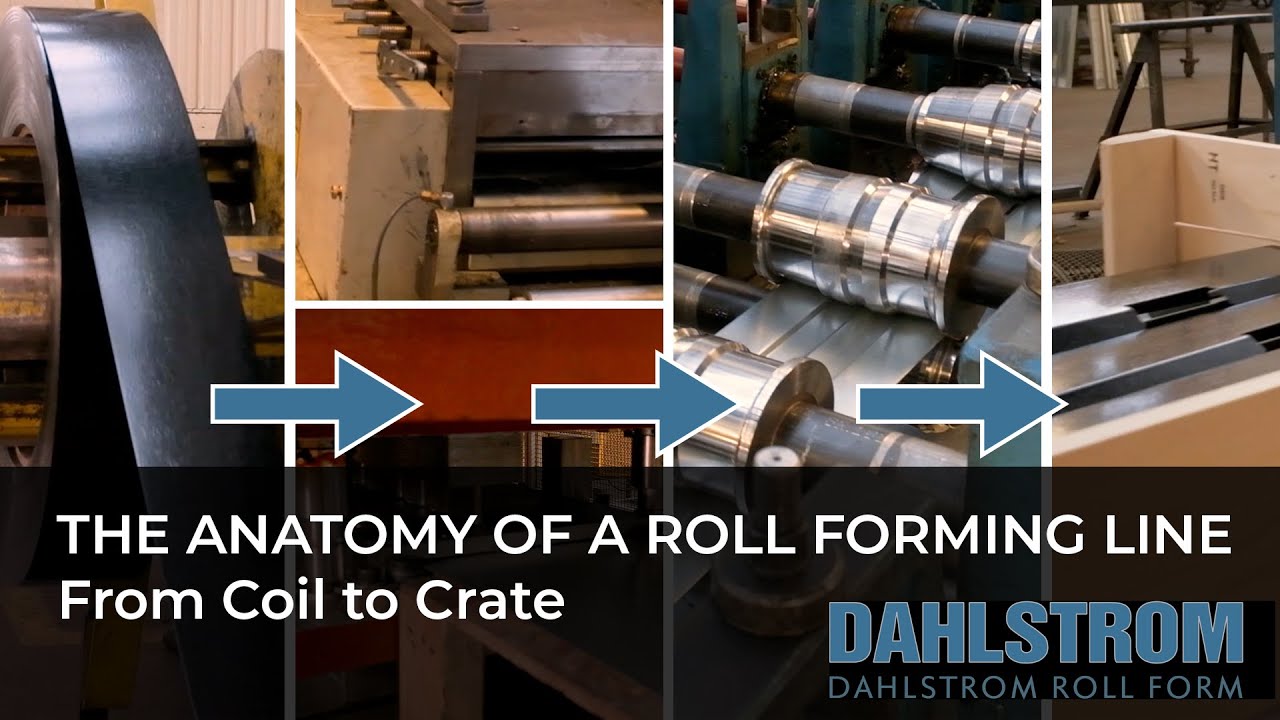
Показать описание
The roll forming process beings with a coil of metal and ends with a finished part in a shipping crate. This video explains each step along the way. The complete process includes 4 parts:
0:00-3:23 Coil & Uncoiler
3:24-7:58 Straightening & Pre-punch Press
7:59-13:19 Roll Forming Mill & Roll Forming Tool Setup
13:20-16:43 Cutoff and Secondary Operations
Part 1 of 4: The first step in the continuous roll forming line is loading a metal coil onto the uncoiler machine. The uncoiler operation is controlled by a laser loop system that detects slack in the strip and feeds downstream machines at the optimum speed. Dahlstrom Roll Form’s specialized uncoiling capabilities: powered uncoilers, unpowered uncloilers, dual spindle uncoilers, and coil cradles can accommodate the full range of materials, gauges, and weights. Industry-leading AMS controls ensure the process is always running at maximum speed and precision.
Part 2 of 4: The second step in the continuous roll forming line is leveling and straightening the metal with coil processing equipment. The straightener removes defects such as bow, camber, and twist. After coil straightening, a pneumatic punch press feeder pulls the strip into a pre-punch press. The servo controlled feeder is accurate to 0.001”. In the pre-punch press, a die punches specifically designed holes through the strip. The holes punched by the die will be used to detect cutoff times down the line.
Part 3 of 4: The third step in the continuous roll forming line is setting up the roll forming mill and tooling. The roll forming machine setup is the most important part of the process and often takes 5-9 hours to complete. The roll forming tools are placed precisely in the machine with feeler gauges. Electric motors and gearing drive the force through the tooling shafts to form the strip.
Part 4 of 4: The final step in the continuous roll forming line is the cutoff process and secondary operations. A linear encoder records the speed of a metal strip through the roll form mill. The speed is synced with a sensor, which detects pre-punched holes and triggers the cutoff press. Once the strip is cut, end bending or other secondary operations take place. The completed roll formed part is then packaged in a crate for shipping.
Dahlstrom Roll Formed Parts & Decorative Metal Mouldings
0:00-3:23 Coil & Uncoiler
3:24-7:58 Straightening & Pre-punch Press
7:59-13:19 Roll Forming Mill & Roll Forming Tool Setup
13:20-16:43 Cutoff and Secondary Operations
Part 1 of 4: The first step in the continuous roll forming line is loading a metal coil onto the uncoiler machine. The uncoiler operation is controlled by a laser loop system that detects slack in the strip and feeds downstream machines at the optimum speed. Dahlstrom Roll Form’s specialized uncoiling capabilities: powered uncoilers, unpowered uncloilers, dual spindle uncoilers, and coil cradles can accommodate the full range of materials, gauges, and weights. Industry-leading AMS controls ensure the process is always running at maximum speed and precision.
Part 2 of 4: The second step in the continuous roll forming line is leveling and straightening the metal with coil processing equipment. The straightener removes defects such as bow, camber, and twist. After coil straightening, a pneumatic punch press feeder pulls the strip into a pre-punch press. The servo controlled feeder is accurate to 0.001”. In the pre-punch press, a die punches specifically designed holes through the strip. The holes punched by the die will be used to detect cutoff times down the line.
Part 3 of 4: The third step in the continuous roll forming line is setting up the roll forming mill and tooling. The roll forming machine setup is the most important part of the process and often takes 5-9 hours to complete. The roll forming tools are placed precisely in the machine with feeler gauges. Electric motors and gearing drive the force through the tooling shafts to form the strip.
Part 4 of 4: The final step in the continuous roll forming line is the cutoff process and secondary operations. A linear encoder records the speed of a metal strip through the roll form mill. The speed is synced with a sensor, which detects pre-punched holes and triggers the cutoff press. Once the strip is cut, end bending or other secondary operations take place. The completed roll formed part is then packaged in a crate for shipping.
Dahlstrom Roll Formed Parts & Decorative Metal Mouldings
Комментарии