filmov
tv
The PLC Is Dead ? Industrial Digitalization Era
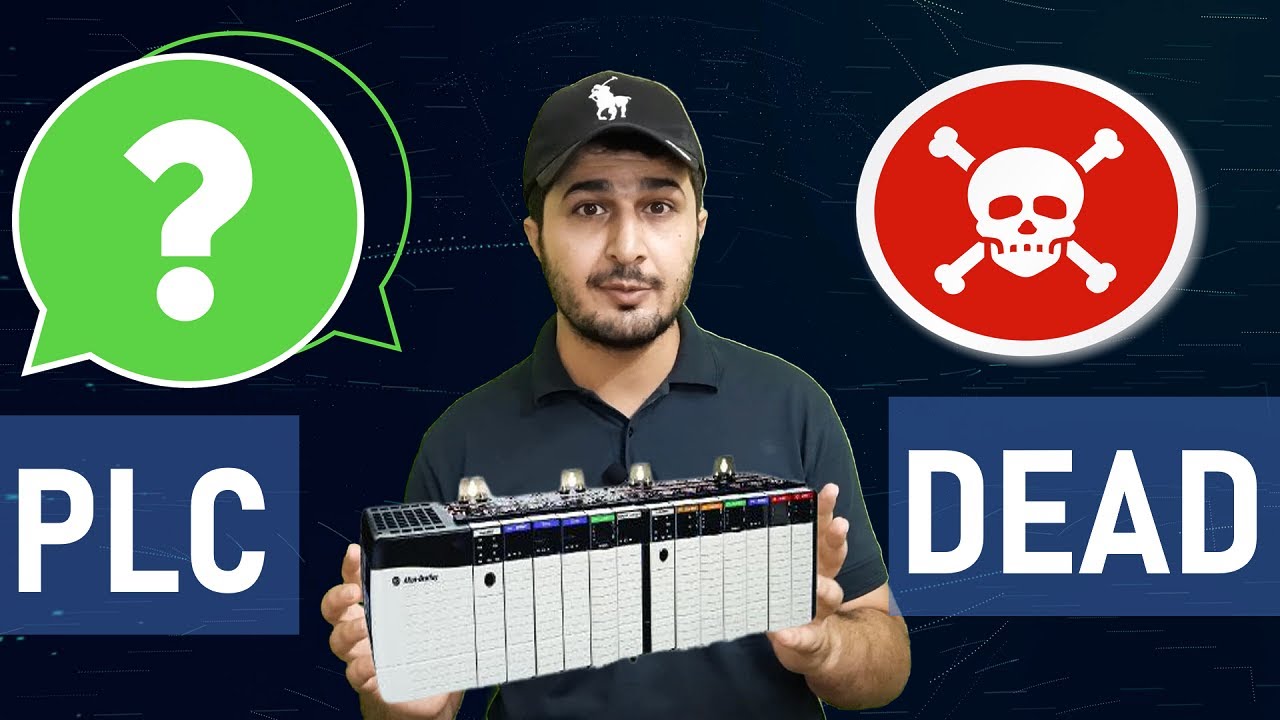
Показать описание
Is PLC Dead ? Industrial Digitalization Era
Instagram: noumanofficialvlogs
There is buzz out there, PLC or programmable logic controller will die soon…. What my view on that today’s video is all about that..
With advancement in industrial IOT , industry 4.0 and Industrial digitization , some people believe it will soon kill PLC, as edge server( Computer PC with high specification RAM and redundancy features,) implementations are on rise.
PLCs are, and will continue to be used heavily in industrial sectors, automation, manufacturing, and public infrastructure (like wastewater treatment, electric utilities, gas utilities, traffic control systems, bridge and railroad controls, etc). PLCs are a popular option because of a few key points
1: PLC Technology is rapidly improving, latest PLC from siemens, Rockwell, GE are other brands like PLC next made cloud connectivity so easy than ever.
2: They are robust to withstand harsh environments commonly found in an industrial setting, such as widely varying temperatures, humidity, electromagnetic interference (EMI) noise, current flows, and shocks and vibration. Most PC based systems would not stand well in this kind of environment.
3: PLCs are dedicated controllers meant to run the specific application code for the machines task and in real time. In a PC based system, there may be a delay from when an input is given, until a desired output is achieved. A PLC is meant to process information in real-time and adjust or react to the process very quickly, usually within milliseconds (mS). In a motion controlled or process controlled environment, missing an input or not actuating an output in time could mean the end of a critical manufacturing process, loss of profits, life, or a major event like a fire, overflow of a tank, or an explosion.
4: PLCs do not freeze up like PCs do. The PLC is meant to just loop through all of the code endlessly and is dedicated to that specific task. PLCs may halt due to a major or minor error, that may stop the processor from executing code (this is usually due to poor programming, such as a math overflow, infinite loop, watchdog scantime error, or buffer overflow). When this halt happens, there is other code that can be programmed to help properly shut down the process in a safe manner.
5: The PLC does the dirty work on the manufacturing floor or an industrial environment, the SCADA server or PC sits in a nice clean Server room/
6: PLCs will continue to remain popular because a large sum on the code is written in ladder logic and is very familiar with most of the technicians and electricians that can read ladder logic and electrical blueprints. It gives them enough of a tool to go online with a processor with at least read access and troubleshoot why a process is not working, such as seeing a sensor is not on or a motor contactor is not starting. It is more cost effective to have a team of technicians rather than full time engineers to open the program every time there is a problem. PLCs support is also heavily invested in by various manufacturers of industrial hardware, such as supporting add on code and instructions and drivers to specific PLCs.
Finally, depending on the model you chose, some PLCs may be very economical and cost effective for controlling a small machine rather than the cost of paying 5–10 times more for a PC based system, that would also require additional hardware to interface with hardwired IO systems.
Instagram: noumanofficialvlogs
There is buzz out there, PLC or programmable logic controller will die soon…. What my view on that today’s video is all about that..
With advancement in industrial IOT , industry 4.0 and Industrial digitization , some people believe it will soon kill PLC, as edge server( Computer PC with high specification RAM and redundancy features,) implementations are on rise.
PLCs are, and will continue to be used heavily in industrial sectors, automation, manufacturing, and public infrastructure (like wastewater treatment, electric utilities, gas utilities, traffic control systems, bridge and railroad controls, etc). PLCs are a popular option because of a few key points
1: PLC Technology is rapidly improving, latest PLC from siemens, Rockwell, GE are other brands like PLC next made cloud connectivity so easy than ever.
2: They are robust to withstand harsh environments commonly found in an industrial setting, such as widely varying temperatures, humidity, electromagnetic interference (EMI) noise, current flows, and shocks and vibration. Most PC based systems would not stand well in this kind of environment.
3: PLCs are dedicated controllers meant to run the specific application code for the machines task and in real time. In a PC based system, there may be a delay from when an input is given, until a desired output is achieved. A PLC is meant to process information in real-time and adjust or react to the process very quickly, usually within milliseconds (mS). In a motion controlled or process controlled environment, missing an input or not actuating an output in time could mean the end of a critical manufacturing process, loss of profits, life, or a major event like a fire, overflow of a tank, or an explosion.
4: PLCs do not freeze up like PCs do. The PLC is meant to just loop through all of the code endlessly and is dedicated to that specific task. PLCs may halt due to a major or minor error, that may stop the processor from executing code (this is usually due to poor programming, such as a math overflow, infinite loop, watchdog scantime error, or buffer overflow). When this halt happens, there is other code that can be programmed to help properly shut down the process in a safe manner.
5: The PLC does the dirty work on the manufacturing floor or an industrial environment, the SCADA server or PC sits in a nice clean Server room/
6: PLCs will continue to remain popular because a large sum on the code is written in ladder logic and is very familiar with most of the technicians and electricians that can read ladder logic and electrical blueprints. It gives them enough of a tool to go online with a processor with at least read access and troubleshoot why a process is not working, such as seeing a sensor is not on or a motor contactor is not starting. It is more cost effective to have a team of technicians rather than full time engineers to open the program every time there is a problem. PLCs support is also heavily invested in by various manufacturers of industrial hardware, such as supporting add on code and instructions and drivers to specific PLCs.
Finally, depending on the model you chose, some PLCs may be very economical and cost effective for controlling a small machine rather than the cost of paying 5–10 times more for a PC based system, that would also require additional hardware to interface with hardwired IO systems.
Комментарии