filmov
tv
CONTINUOUS CARBON FIBER vs PLA vs PETG
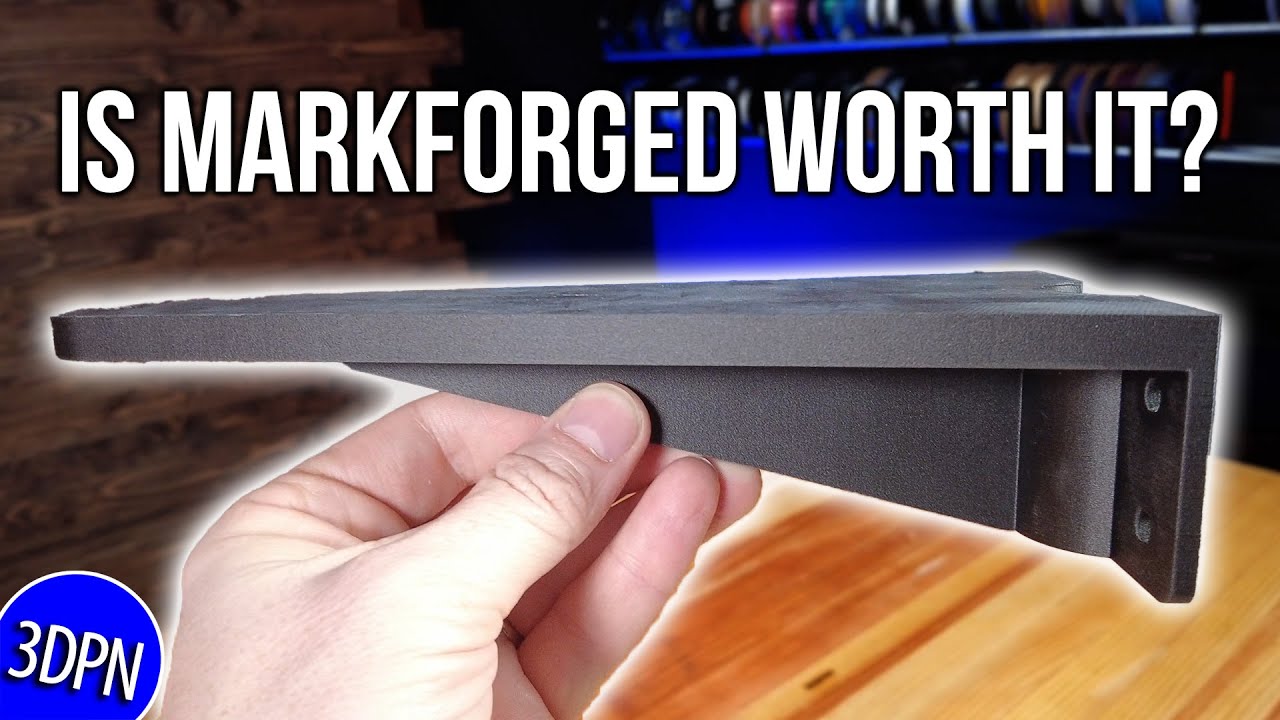
Показать описание
Is @markforgedworth it? Let's get an answer to that question! I designed and printed a bracket for my @VarlaScooter Eagle scooter!
#3dprinting #practicalprinting #additivemanufacturing
Markforged's 3D printers use a unique process called continuous fiber printing, which involves embedding continuous strands of composite materials, such as carbon fiber, Kevlar, and fiberglass, into a thermoplastic base material. This creates parts that are incredibly strong, durable, and lightweight.
Markforged also offers a cloud-based software platform, called Eiger, which allows users to design, optimize, and manage the production of 3D-printed parts. The platform includes a range of features, such as automatic part orientation, strength analysis, and slicing, which help to streamline the design and printing process and ensure high-quality, functional parts are produced every time.
SUPPORT! 😍
GEAR! 🎥🎦📷
MATERIALS 🦇
THE TEAM! 🤟
--------------------------------
Find Me Socially!
--------------------------------
--------------------------------
Want to send me something?
--------------------------------
3D Printing Nerd
PO Box 55532
Shoreline, WA 98155
USA
Music in Episodes Comes From:
FTC Disclaimer: A percentage of sales is made through Affiliate links
#3dprinting #practicalprinting #additivemanufacturing
Markforged's 3D printers use a unique process called continuous fiber printing, which involves embedding continuous strands of composite materials, such as carbon fiber, Kevlar, and fiberglass, into a thermoplastic base material. This creates parts that are incredibly strong, durable, and lightweight.
Markforged also offers a cloud-based software platform, called Eiger, which allows users to design, optimize, and manage the production of 3D-printed parts. The platform includes a range of features, such as automatic part orientation, strength analysis, and slicing, which help to streamline the design and printing process and ensure high-quality, functional parts are produced every time.
SUPPORT! 😍
GEAR! 🎥🎦📷
MATERIALS 🦇
THE TEAM! 🤟
--------------------------------
Find Me Socially!
--------------------------------
--------------------------------
Want to send me something?
--------------------------------
3D Printing Nerd
PO Box 55532
Shoreline, WA 98155
USA
Music in Episodes Comes From:
FTC Disclaimer: A percentage of sales is made through Affiliate links
Комментарии