filmov
tv
CoreXY explained: Comparison + strengths & weaknesses
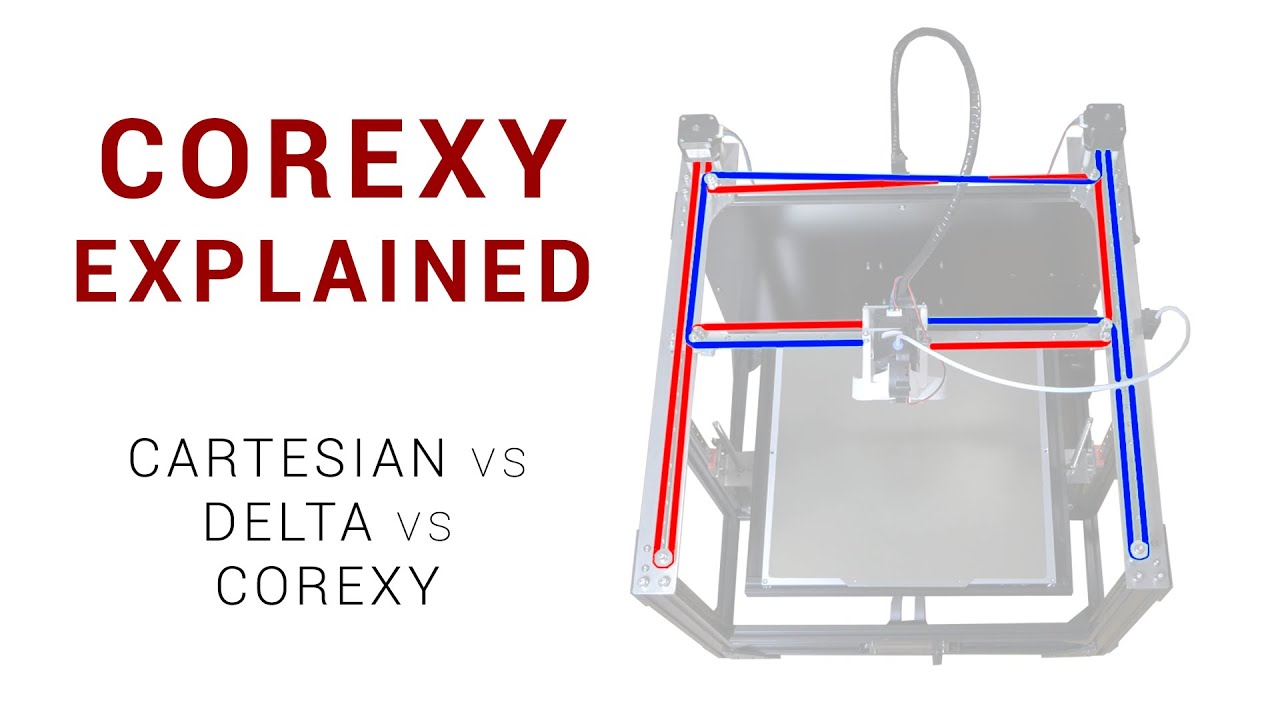
Показать описание
CoreXY seems quite popular at the moment, with a range of printers now available from manufacturers. This is on top of great designs such as the Hypercube on Thingiverse. In this video, a comparison between CoreXY, various cartesian and the delta motion system is made, exploring the strengths and weaknesses of each.
A summary for CoreXY:
-Space efficient
-Rigid cube frame (typically)
-Two stepper motors sharing X/Y movement 99% of the time
-Fast and precise when used with a light print head, which is generally inherent with no moving bed for X and Y
-Belt tension is critical
-A rigid frame and pulley system is critical
-Getting these wrong may ruin the output of the printer, getting them right may raise the cost.
Thanks to Seckit3DP and Tronxy for responding to my question during the making of this video.
Take a look around and if you like what you see, please subscribe.
A summary for CoreXY:
-Space efficient
-Rigid cube frame (typically)
-Two stepper motors sharing X/Y movement 99% of the time
-Fast and precise when used with a light print head, which is generally inherent with no moving bed for X and Y
-Belt tension is critical
-A rigid frame and pulley system is critical
-Getting these wrong may ruin the output of the printer, getting them right may raise the cost.
Thanks to Seckit3DP and Tronxy for responding to my question during the making of this video.
Take a look around and if you like what you see, please subscribe.
Комментарии