filmov
tv
Sculptural Wood Joints
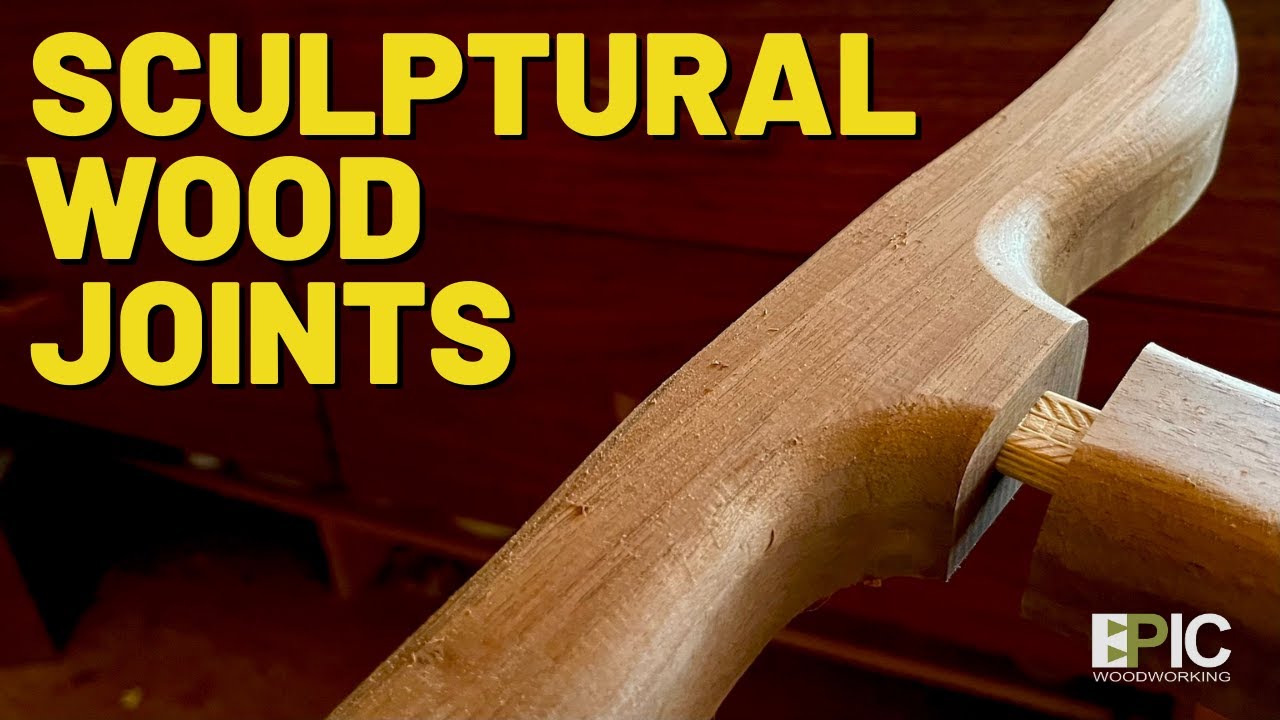
Показать описание
⚙️ SHOW NOTES - EPISODE #190: After recently seeing the works of Sam Maloof and Wharton Esherick up close, I am inspired to explore the art and structure of sculptural wood joints. In this episode I share my best methods and techniques while we make a contoured wood joint, an element that just might generate fresh ideas for an upcoming project.
⚙️ RELATED VIDEO RESOURCES
⚙️ EPISODE LINKS
⚙️ SUBSCRIBE here and CLICK THE BELL to be notified of future live events and video uploads.
⚙️ SOCIALS
• Instagram: @tommclaughlin10
• Facebook: @EpicWoodworking
• Twitter: @EpicWoodworking
• YouTube: @EpicWoodworking
~~~~~~~
LIVE EVENTS are filmed in the shop of Tom McLaughlin, host of TV's Classic Woodworking and Shop Night Live. Tom loves to pass on the craft of woodworking by creating projects to present in live video form backed by his over 30-years of experience making fine custom furniture.
~~~~~~~
FTC Disclosure: In general, the links we provide through Amazon are affiliate links, which means we will receive a small commission if you purchase something using that link. Affiliate arrangements are not a focus for us, but we do want you to be aware of this one.
⚙️ RELATED VIDEO RESOURCES
⚙️ EPISODE LINKS
⚙️ SUBSCRIBE here and CLICK THE BELL to be notified of future live events and video uploads.
⚙️ SOCIALS
• Instagram: @tommclaughlin10
• Facebook: @EpicWoodworking
• Twitter: @EpicWoodworking
• YouTube: @EpicWoodworking
~~~~~~~
LIVE EVENTS are filmed in the shop of Tom McLaughlin, host of TV's Classic Woodworking and Shop Night Live. Tom loves to pass on the craft of woodworking by creating projects to present in live video form backed by his over 30-years of experience making fine custom furniture.
~~~~~~~
FTC Disclosure: In general, the links we provide through Amazon are affiliate links, which means we will receive a small commission if you purchase something using that link. Affiliate arrangements are not a focus for us, but we do want you to be aware of this one.
Комментарии