filmov
tv
Reducing Downtime with 3 Innovative Upgrade Approaches
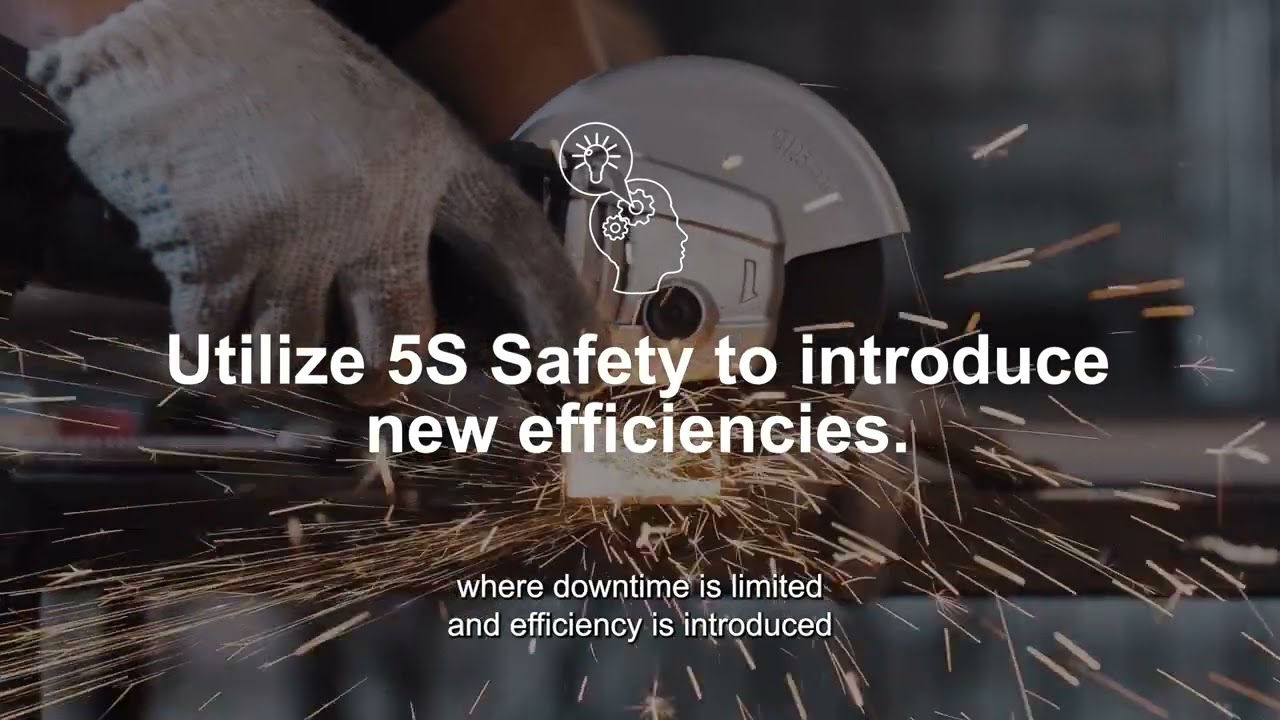
Показать описание
Downtime in manufacturing is one of the most costly problems in the industry. Recent studies show that downtime in manufacturing can cost up to an average of $260,000 an hour, with an average downtime of 800 hours per year. That’s over $200 million dollars in losses of revenue every year!
This includes loss of production, wasted labor, and depleted inventory, majorly caused by process or equipment failures, unforeseen accidents, or shortage of raw material.
Although downtimes are usually unpredictable, it’s important to plan ahead in case these events take place. A way to prevent major losses due to downtime is by scheduling and planning a maintenance and downtime session to reduce the chances of unprecedented problems.
Often times, downtime is considered a part of the project planning process. When planned right, it can be effectively managed to have the least amount of damage or impact on the manufacturing line. It’s important to make sure that all pieces of equipment are properly maintained to decrease the probability rate of equipment failures. Understanding the Overall Equipment Effectiveness (OEE) will be beneficial for both the management and engineering processes. In addition, maintaining all required Personal Protective Equipment (PPE) as well as machine guarding precautions in the plant is a must-do.
This includes loss of production, wasted labor, and depleted inventory, majorly caused by process or equipment failures, unforeseen accidents, or shortage of raw material.
Although downtimes are usually unpredictable, it’s important to plan ahead in case these events take place. A way to prevent major losses due to downtime is by scheduling and planning a maintenance and downtime session to reduce the chances of unprecedented problems.
Often times, downtime is considered a part of the project planning process. When planned right, it can be effectively managed to have the least amount of damage or impact on the manufacturing line. It’s important to make sure that all pieces of equipment are properly maintained to decrease the probability rate of equipment failures. Understanding the Overall Equipment Effectiveness (OEE) will be beneficial for both the management and engineering processes. In addition, maintaining all required Personal Protective Equipment (PPE) as well as machine guarding precautions in the plant is a must-do.