filmov
tv
Motion Control with BeagleBone Black or Raspberry Pi and ClearPath-SC Servos
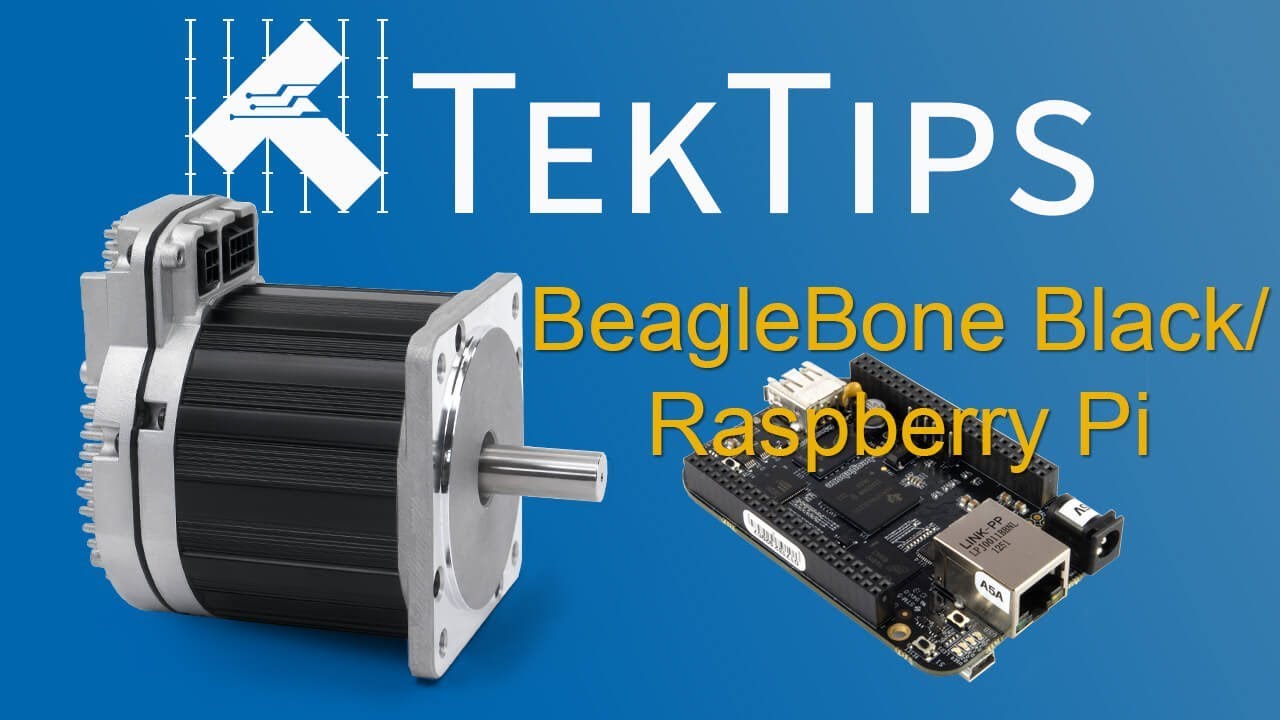
Показать описание
Watch this video to learn about using ClearPath SC (Software Control) with single board computers such as BeagleBone Black or Raspberry Pi.
ClearPath-SC blends a sophisticated, networked motion controller into the already compact ClearPath all-in-one servo motor system. Using ClearPath SC, your single board computer, and C++ libraries provided by Teknic, you can coordinate up to 48 axes or more. This system also gives you access to features such as g-Stop tuning, head-tail moves, conditional torque limiting, position capture, and more.
Teknic wants your feedback. Like this video? Give it a thumbs up! Be sure to comment with any questions about motion control and let us know what you did or did not like about the video.
For more information on Teknic ClearPath servos, subscribe to our channel and visit Teknic's website.
ClearPath SC is controlled via a host application in software. SC gives customers greater flexibility to meet the needs of conditional and complex applications. The SC does not use a third party indexer like the SD series nor input triggers like on the MC series. Everything is written and moves are commanded using your C++ application codes and Teknic's API.
ClearPath-SC blends a sophisticated, networked motion controller into the already compact ClearPath all-in-one servo motor system. Using ClearPath SC, your single board computer, and C++ libraries provided by Teknic, you can coordinate up to 48 axes or more. This system also gives you access to features such as g-Stop tuning, head-tail moves, conditional torque limiting, position capture, and more.
Teknic wants your feedback. Like this video? Give it a thumbs up! Be sure to comment with any questions about motion control and let us know what you did or did not like about the video.
For more information on Teknic ClearPath servos, subscribe to our channel and visit Teknic's website.
ClearPath SC is controlled via a host application in software. SC gives customers greater flexibility to meet the needs of conditional and complex applications. The SC does not use a third party indexer like the SD series nor input triggers like on the MC series. Everything is written and moves are commanded using your C++ application codes and Teknic's API.
Комментарии