filmov
tv
Learn An Old Timer's Secrets To Mig Weld Aluminum Without A Spoolgun
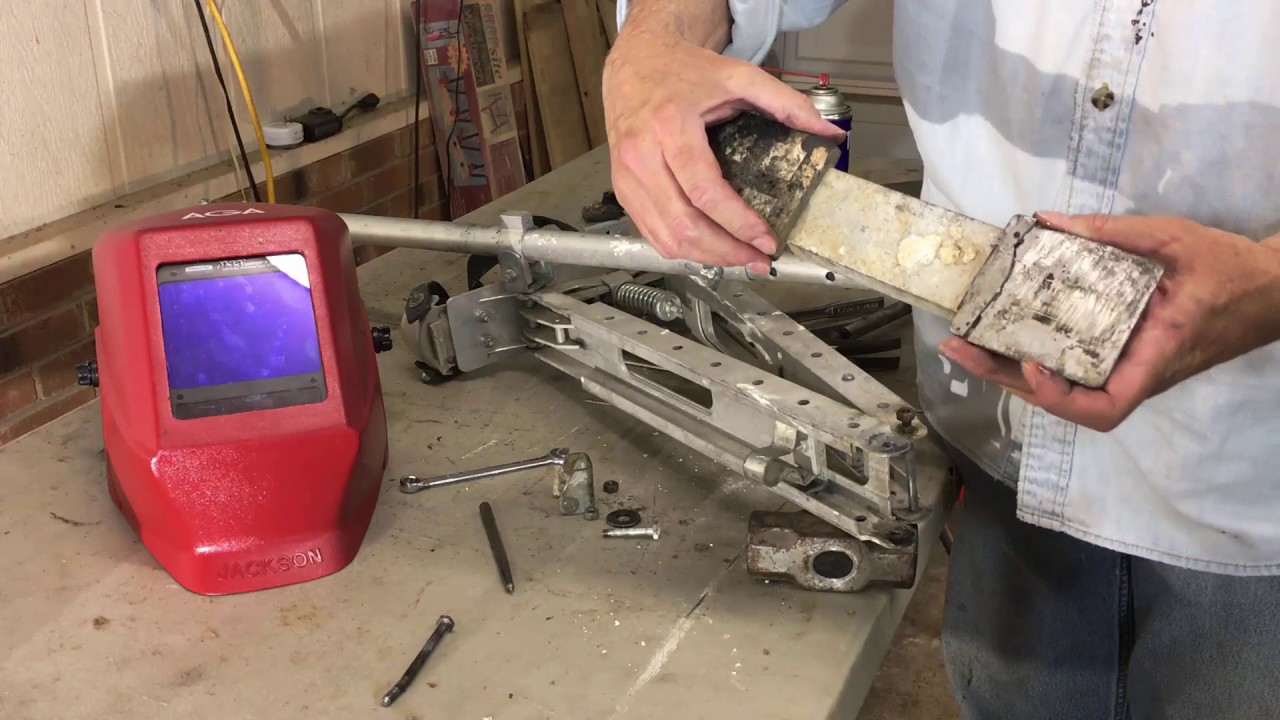
Показать описание
Did you ever wonder how they weld aluminum with a Mig Welder? It can be very difficult, if not impossible. Usually, they use an expensive Spool Gun that is an attachment to a Mig Welder. That allows a welder to get smooth aluminum welds. But, who has that kind of money to spend on a Spool Gun? This video shows how to weld aluminum without any add-ons. With a few tricks and secrets, aluminum can actually be welded with a 110 volt Mig Welder.
__________________________________________________________
What I have in my kit:
________________________________________________________
Some of the items used in this video:
Welding Equipment:
Video Equipment used to make this video:
- iPhone 6, no longer available as New
For Informational Purposes Only. Don't attempt to Mig Weld or do any other type of welding without Certified Welding Training. With or Without that Certified knowledge, welding can be hazardous, and by welding you do so at your own risk.
NEVER open up a welding machine as it can still have dangerous voltage built-up in the electronics.
Whenever changing out consumables on a Mig Welder, first TURN OFF the machine and unplug it, also.
DISCLAIMER: This video and description contains affiliate links, which means that if you click on one of the product links, I’ll receive a small commission. This helps support the channel and allows us to continue to make videos like this. Thank you for the support!
__________________________________________________________
What I have in my kit:
________________________________________________________
Some of the items used in this video:
Welding Equipment:
Video Equipment used to make this video:
- iPhone 6, no longer available as New
For Informational Purposes Only. Don't attempt to Mig Weld or do any other type of welding without Certified Welding Training. With or Without that Certified knowledge, welding can be hazardous, and by welding you do so at your own risk.
NEVER open up a welding machine as it can still have dangerous voltage built-up in the electronics.
Whenever changing out consumables on a Mig Welder, first TURN OFF the machine and unplug it, also.
DISCLAIMER: This video and description contains affiliate links, which means that if you click on one of the product links, I’ll receive a small commission. This helps support the channel and allows us to continue to make videos like this. Thank you for the support!
Комментарии