filmov
tv
How SpaceX Mastered Starship’s Welding
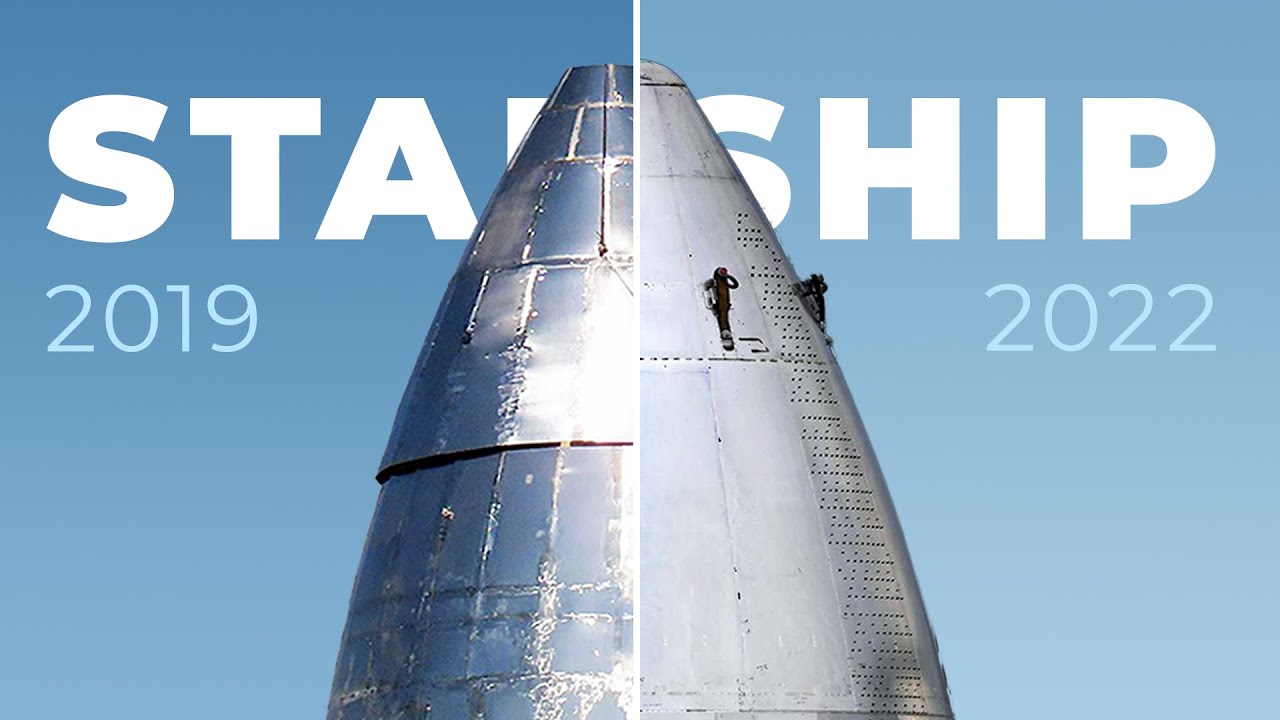
Показать описание
Since SpaceX first started building Starship back in 2018, we’ve seen it go from looking rough and weak to a very sophisticated rocket. This video looks at how SpaceX developed their welding technique for Starship and how it led to a stronger and better looking rocket.
Thanks to these awesome people for their resources:
Special thanks to Chris Nash, Nicholas Queiroz and Riley Mannion for their expertise on welding.
References:
Thanks for watching this Primal Space video. If you enjoyed it, let me know in the comments below and don't forget to subscribe so you can see more videos like this!
Support Primal Space by becoming a Patron!
Music used in this video:
» Vaculator Blues - The Mini Vandals
» Sprightly Pursuit - Cooper Cannell
» Sunset Trails - DJ Williams
» Double You - The Mini Vandals
» Marianas - Quincas Moreira
Credits:
#SpaceX #Starship #ElonMusk
How SpaceX Mastered Starship’s Welding
How SpaceX Mastered Starship’s Welding
How Spacex Developed Their Welding Technique For Starship
Welding Wonders: How SpaceX Achieved Flawless Starship Construction
Elon Musk: 'INSANE! This is How SpaceX Mastered Starship’s Welding!'
How SpaceX Mastered Space Suits
What SpaceX just did with Starship's Welding shocked the entire industry!
How SpaceX Gained Mastery of Starship’s Welding Technique.
SpaceX INSANE UPGRADE on Starship's welding SHOCKS The Entire Space Industry!
SpaceX's NEW UPGRADE On Starship's Welding is unlike any other!
SpaceX’s Starship Launch Attempt. Repost from @weldmoney(TikTok) #yeswelder #shorts #welding #weld
SpaceX's HUGE UPGRADE on Starship's welding will blow your mind!
Spacex Smooth Starship Welding Is A Game Changer
What SpaceX just did with Starship's Welding shocked the entire industry!
Crafting the Future: How SpaceX Perfected Welding to Forge Starship's Triumph!
How Does SpaceX Build Starships at Starbase? From Steel to Starship.
SpaceX's New Upgrade On Starship's Welding Will Change Everything
SpaceX Starship Is MASTER Rocket Manufacturing
The Entire Rocket Industry Was Astonished by Starship's welding from SpaceX team
SpaceX MADE Incredible Adjustments to solve Heatshield Tiles falling during Starship Liftoff
SpaceX's Unbelievable Upgrade for Starship Welding – You Won't Believe What It Is!
It's mind-blowing! What SpaceX just did with Starship's Welding&Nosecone shocked the e...
Asteroid Hitting The Moon🌒💥#lunarsurface #telescope #moon #asteroid #nasa #space #shorts
SpaceX Starship - How landing works #shorts
Комментарии