filmov
tv
The Ingenious guy Connected Broken Input-shaft Very Nicely / Pk process
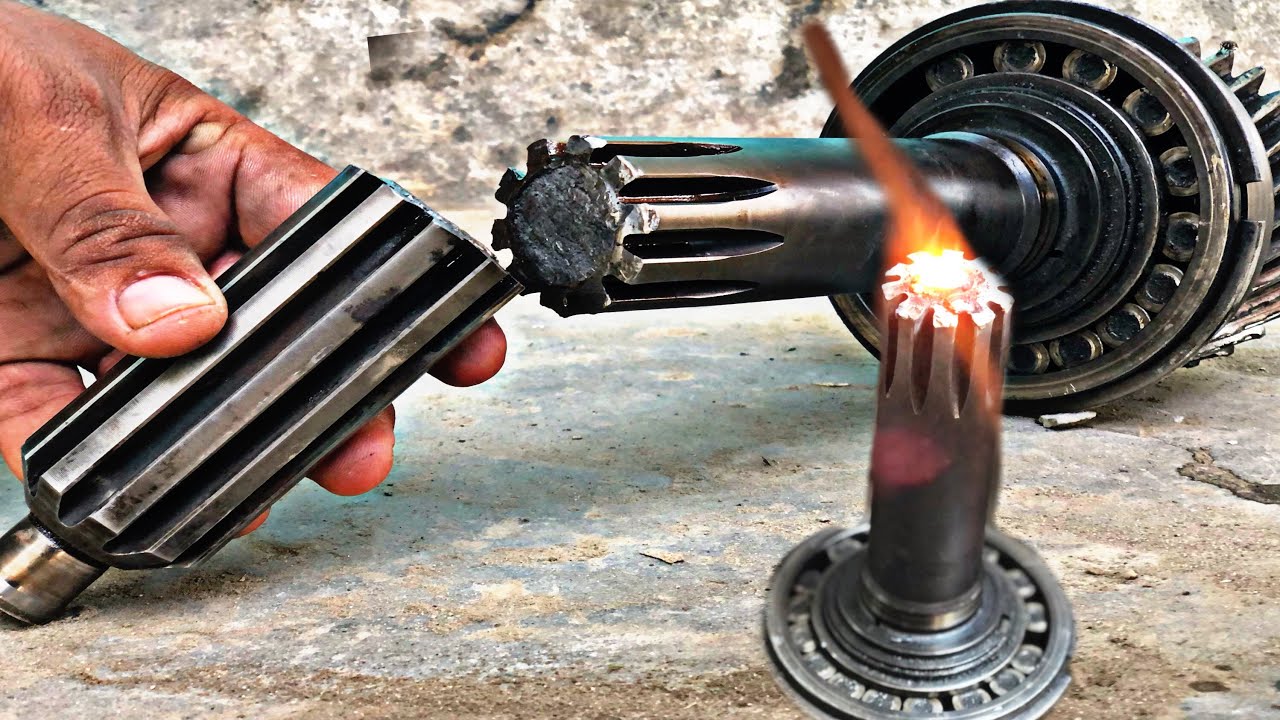
Показать описание
The Ingenious guy Connected Broken Input-shaft Very Nicely / Pk process
#brokeninputshaft
#ingeniousman
#pkprocess
The top gear which was broke due to overload was very well attached
#brokeninputshaft
#ingeniousman
#pkprocess
The top gear which was broke due to overload was very well attached
The Ingenious guy Connected Broken Input-shaft Very Nicely / Pk process
The Ingenious guy Connected Broken Crankshaft Very Nicely // Super Mechanic
The Ingenious Guy Connected Broken Input-shaft Very Nicely Truck parts repairing
The best ingenious Guy Connected of Broken Main Shaft Very Nicely Repair
The Ingenious guy Connected Broken Input shaft Very nicely Restoration | Unique repairing on lathe
The Ingenious guy Connected Broken 18 Seater Toyota Hiace Wheel Axle Very Nicely ,,,,,,,
New Logical Process!The Ingenious Guy Connected Broken Input Shaft Very Nicely
The Ingenious guy Connected Broken Input-shaft Very Nicely / Amazing process
OLHA O QUE ELE FEZ COM UM CÂMBIO VELHO The Ingenious guy Connected Broken Input-shaft Very Nicely
This Ingenious Guy Connected Broken Differential Gear Ring Very Nicely
Ingenious guy Connected Broken Input-shaft Very Nicely
Technically Done by Ingenious Guy Connected Broken Input-Shaft || Restoration of Broken Input Shaft|
the best ingenious broken main shaft
The Ingenious Guy Connected Broken input shaft very nicely repair | Massey ferguson tractor repair
The Ingenious guy Repair broken Input-Shaft Very Nicely
The INGENIOUS Man Connected Broken INPUT Shaft Amazing
Ingenious Guy Repaired Broken Input Shaft Very Nicely And Connected broken Shaft
How Ingenious Mechanic Connected Broken 2 pieces Gear MainShaft Very Nicely // Ultimate Process
Ingenious way to repair broken plastic
How to Connect a Broken Tractor Axle Shaft with Ingenious Skills #TractorAxleRepair
amazing technology process
The Ingenious guy connected Broken Input shaft
The gear transmission turned out to be connected to a broken input shaft and pickup mechanism.
we connected broken crankshaft
Комментарии