filmov
tv
1857 How To Make Super Strong 3D Printed Parts
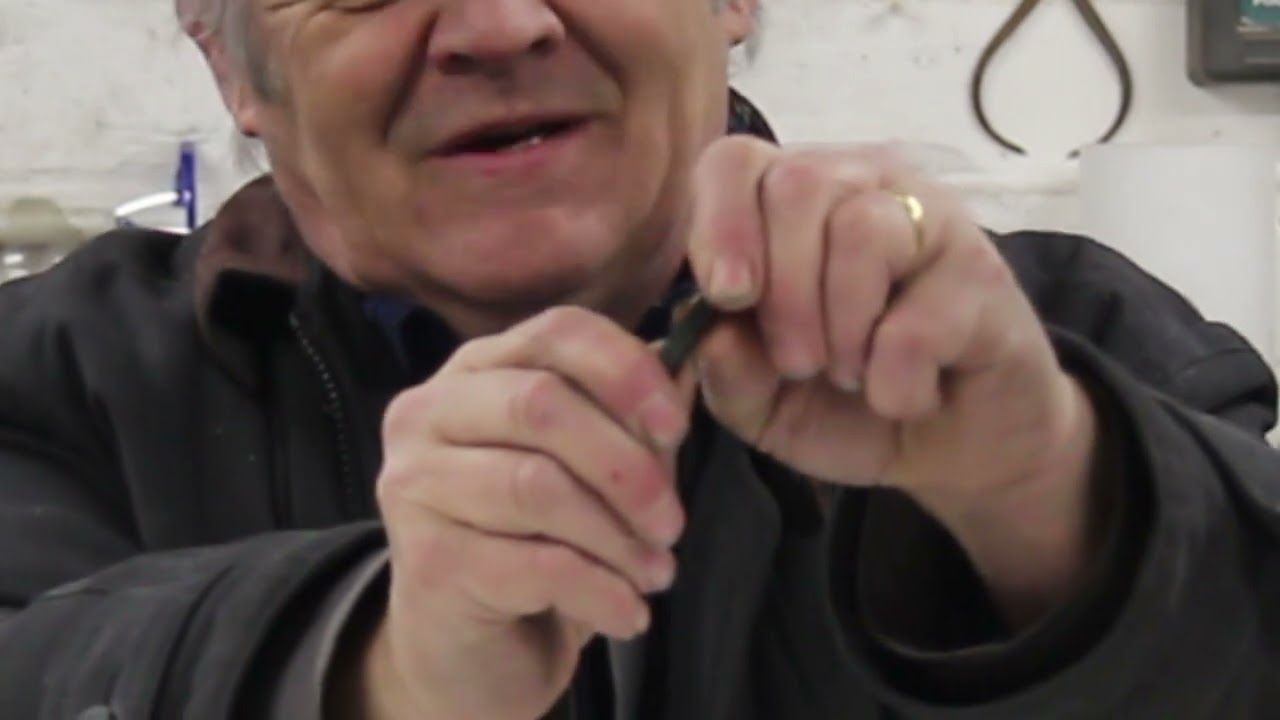
Показать описание
1857 How To Make Super Strong 3D Printed Parts
Man Born in 1853 Talks About Childhood in the 1860s- Enhanced Video & Audio [60 fps]
Can you solve this 150 years old puzzle? #shorts
Germany’s Oldest Street-Legal Car | 1894 Benz Victoria | German Cars
Revolt of 1857 | Major Causes | Political Causes | Administrative | Discontent among Sepoys | Socio
This Type of Bullet Caused an Entire Uprising!
THE HISTORY OF INDIA in 12 Minutes - Part 1
How the British Empire Became the Biggest in the World
Trapped In Year 1851, Modern Chef Cooks MCDONALD Surprising Queens & Kings
Mercedes-Benz ACTROS - Restoration Abandoned Semi Trailer Truck
Soch Stories Ep3: Chapati movement in 1857, explained
Making of Super Duper Hit show-Gadar 1857
Can WELDING really make you BLIND? (3D Animation) #Shorts
Crash Course Modern history India 1857 - 1947 | Polity UPSC, IAS, CDS, NDA, SSC CGL
ANTES de COMPRA una AIR FRYER mira ESTE VÍDEO | Guía de compra freidoras de aire
GE Profile Built-In Side by Side Refrigerator - Turbo Cool Setting
Play Time's Over || Paulsen vs Morphy (1857) || 1st American Chess Congress
Aged Steak's Amazing Transformation (2 Weeks to 160 Days) | Bon Appétit
1st Tractor of world | history of tractor | invention of tractor
#1857 Super Hit Classic Movie | Surendra, Suraiya
In Memoriam - Jallianwala Bagh Massacre | Indian History with BYJU'S
Easy Jhansi ki Rani Laxmi bai Drawing from Letter // Freedom Fighter Drawing // Easy Drawing
Don’t oversimplify Mormon history | Response to Johnny Harris
Why was India split into two countries? - Haimanti Roy
Комментарии