filmov
tv
I keep issuing discipline to Maintenance Employees -- Is this the right answer?
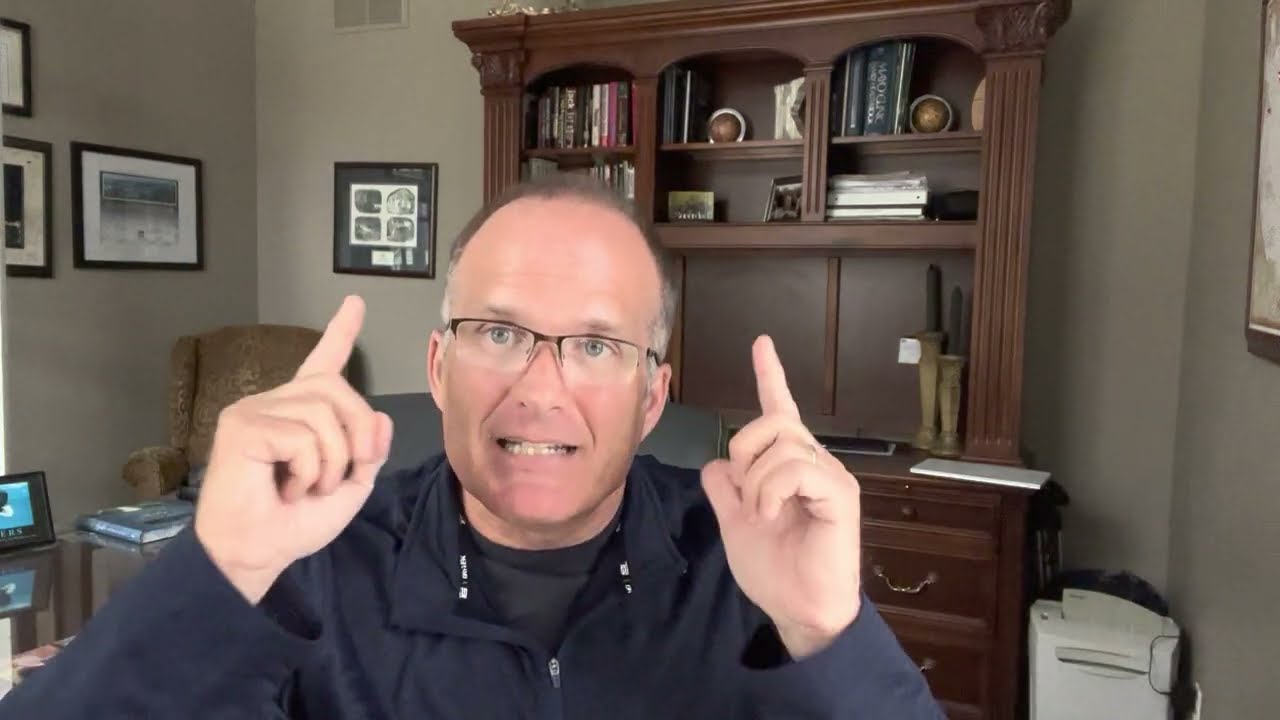
Показать описание
This video is a reply to a maintenance manager's question about issuing discipline to craft employees for rule violations. What advice do I have and what have I learned in my journey. Spoiler Alert: I did it wrong for 20 years. I did it well for 14. I know what works. See my story.
-------------------------------------------------------------------
100% Satisfaction and Money back Guarantee on all services
--------------------------------------------------------------------
I want a Mentor, Coach and/or Consulting from Joe -- up to 1 hour
---------------------------------------------------------------------
A Plant Manager's Resume Guide -- USD $50.00
* I created a guide to you creating an outstanding eye-catching resume.
----------------------------------------------------------------------
A Plant Manager's key points to mastering the Job Interview -- USD $50.00
-----------------------------------------------------------------------
Get both my Resume Guide and Mastering the Job Interview for USD $75.00
-- 25% Off when you bundle!!!
-------------------------------------------------------------------------
How to Negotiate a Pay Raise -- Step by Step
-------------------------------------------------------------------------
Get my Book from Amazon: Zero to Hero: How to Jumpstart your Reliability Journey
given today's Business Challenges
If you are having difficulty buying book and you are Non-US; Try Amazon.UK.
-----------------------------------------------------------------------------------------
-----------------------------------------------------------------------------------------
Video by Lean Driven Reliability LLC
-----------------------------------------------------------------------------------------
Has this content improved your career? Got you a promotion? consider supporting me through Subscribe Star for $10/month via this link:
-----------------------------------------------------------------------------------------
I am not a Financial Advisor. The content of these videos is not intended to be advice, but rather to tell my experience and story; they are for your entertainment only. Seek professional advice before making any financial decision including when to become financially independent and/or retire early.
#reliability, #maintenancebestpractices, #plantmanager, #reliabilityengineer, #maintenancemanager, #maintenanceplanning, #assetmanagement
Professionally, I am is first and foremost a plant manager, leader and now an entrepreneur. I have been a plant manager 3 times (largest plant $1.5B in sales / 2000 employees), a large department manager twice, an engineer, and due to results and methods, I was appointed the global director of reliability and maintenance for a Fortune 200 company.
My unique approach to driving reliability results come from not only my 35 years of experience, but also by combining Lean and Reliability best practices (I am a CMRP and have extensive Lean/Six-sigma training internal to Alcoa). Lean provides the waste focus and drives understanding of current state which has proven to be the "secret sauce" to achieving sustainable, scalable and rapid results -- most often in just weeks. Lean, as a general rule, has not been applied to maintenance and reliability -- and is fertile ground. Don't let this sound complicated -- it is very basic: Know current state through observation and the required actions will present themselves. ALL best practices target waste elimination.
Financial Independence Retire Early - This channel started to change the maintenance and reliability consulting industry. Viewers began to ask for content on my FIRE journey (I retired at 54 yo). I am happy to share my story, successes, failures, and lessons learned. The content is intended to make you think and create your story. My path is my path -- not right or wrong. Again, I am not a financial advisor -- I'm a story teller. My hope is you will have less fear and more success by hearing my journey.
-------------------------------------------------------------------
100% Satisfaction and Money back Guarantee on all services
--------------------------------------------------------------------
I want a Mentor, Coach and/or Consulting from Joe -- up to 1 hour
---------------------------------------------------------------------
A Plant Manager's Resume Guide -- USD $50.00
* I created a guide to you creating an outstanding eye-catching resume.
----------------------------------------------------------------------
A Plant Manager's key points to mastering the Job Interview -- USD $50.00
-----------------------------------------------------------------------
Get both my Resume Guide and Mastering the Job Interview for USD $75.00
-- 25% Off when you bundle!!!
-------------------------------------------------------------------------
How to Negotiate a Pay Raise -- Step by Step
-------------------------------------------------------------------------
Get my Book from Amazon: Zero to Hero: How to Jumpstart your Reliability Journey
given today's Business Challenges
If you are having difficulty buying book and you are Non-US; Try Amazon.UK.
-----------------------------------------------------------------------------------------
-----------------------------------------------------------------------------------------
Video by Lean Driven Reliability LLC
-----------------------------------------------------------------------------------------
Has this content improved your career? Got you a promotion? consider supporting me through Subscribe Star for $10/month via this link:
-----------------------------------------------------------------------------------------
I am not a Financial Advisor. The content of these videos is not intended to be advice, but rather to tell my experience and story; they are for your entertainment only. Seek professional advice before making any financial decision including when to become financially independent and/or retire early.
#reliability, #maintenancebestpractices, #plantmanager, #reliabilityengineer, #maintenancemanager, #maintenanceplanning, #assetmanagement
Professionally, I am is first and foremost a plant manager, leader and now an entrepreneur. I have been a plant manager 3 times (largest plant $1.5B in sales / 2000 employees), a large department manager twice, an engineer, and due to results and methods, I was appointed the global director of reliability and maintenance for a Fortune 200 company.
My unique approach to driving reliability results come from not only my 35 years of experience, but also by combining Lean and Reliability best practices (I am a CMRP and have extensive Lean/Six-sigma training internal to Alcoa). Lean provides the waste focus and drives understanding of current state which has proven to be the "secret sauce" to achieving sustainable, scalable and rapid results -- most often in just weeks. Lean, as a general rule, has not been applied to maintenance and reliability -- and is fertile ground. Don't let this sound complicated -- it is very basic: Know current state through observation and the required actions will present themselves. ALL best practices target waste elimination.
Financial Independence Retire Early - This channel started to change the maintenance and reliability consulting industry. Viewers began to ask for content on my FIRE journey (I retired at 54 yo). I am happy to share my story, successes, failures, and lessons learned. The content is intended to make you think and create your story. My path is my path -- not right or wrong. Again, I am not a financial advisor -- I'm a story teller. My hope is you will have less fear and more success by hearing my journey.
Комментарии