filmov
tv
Spare Parts #13 - Making A Square Broach
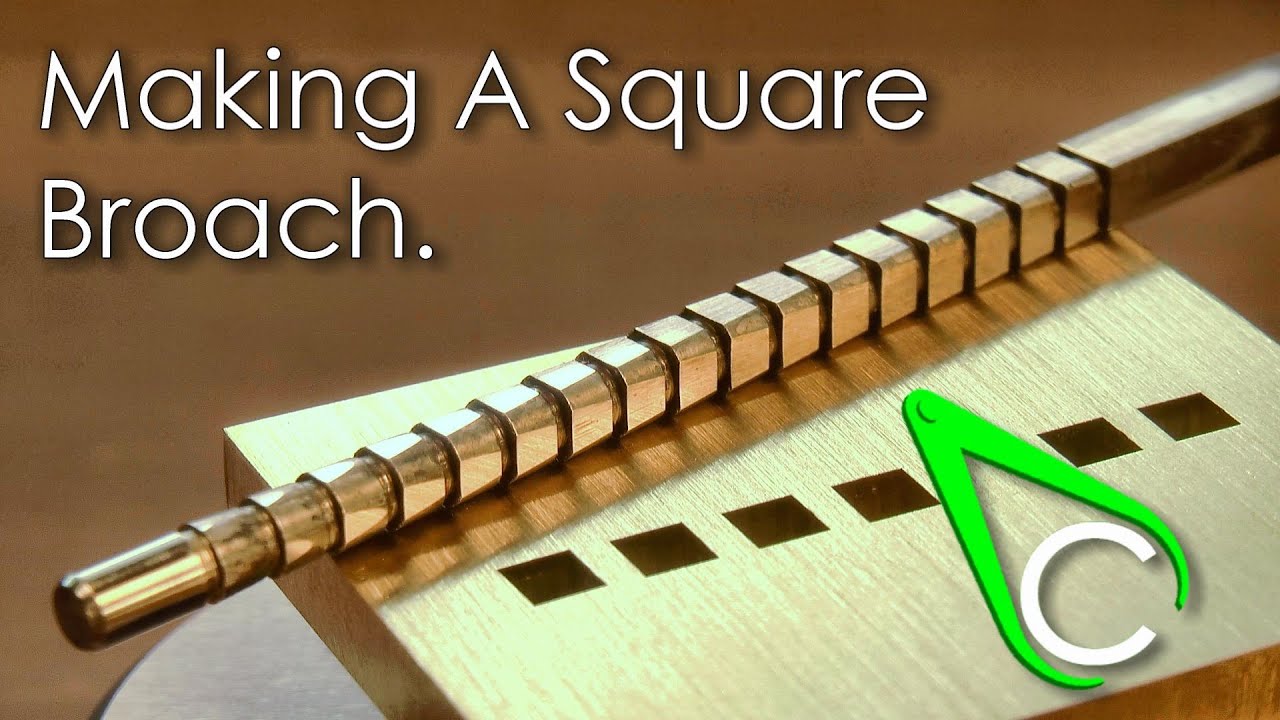
Показать описание
Making A Square Broach, by Clickspring.
It's not necessarily a common event, but when you need to make a square hole, it can be difficult to get a precise result. One of the best methods to achieve a professional cut is to use a custom made broach, so in this video I go through the process of making one from scratch.
________________________________________________________
A very special thank you to patron Dan Keen.
________________________________________________________
You can also help me make these videos by purchasing via the following Amazon Affiliate links:
Cameras used in this video:
Tools & Shop Products:
Abbreviated Transcript:
00:06 No matter what your style of metal working project might be, every now and then there's a need to form a precise square hole.
00:21 A pilot hole locates the exact position of the desired square, and then the broach is forced through the workpiece.
00:53 And that's because, all of the teeth prior to the last tooth collectively prepare the opening for the final tooth to set the dimension, so within reason, we can tolerate some small errors in those teeth, providing that the very last one is correct.
01:26 Its much too long and slender to be turned between centers, so I'll need to form the features by incrementally extending the work from a 4 jaw chuck. And the other key feature is the pilot diameter, which must be centered on the square, so I'm taking care to center the raw stock prior to forming that cylindrical shape.
01:48 I have the work reasonably well centered to begin with, so that when I position the dial indicator, the error that I see for each jaw is quite small I then use 2 chuck keys in opposition to each other, to move the work, so that the dial reads directly between the original 2 readings for both jaws.
02:13 Once its close, I move the zero reference to that point, so that becomes my target when I start to center the other two jaws. Once the work gets close to being centered, the errors start to sit nicely either side of that zero reference, and it gets easier to pull it into position.
02:53 But even doing this quickly, you can see that it will take a fair amount of time to do this for every cut, so there's a strong incentive to bypass this centering process if we can. For now though, the work is centered, so I can make a start on cutting that pilot diameter.
03:39 Next I'm using the first groove position to register the tool after extending the work, and then I'm using the hand wheels to advance the tool the required amount to form the next groove. Now inevitably I will have introduced a small eccentricity to each of these cuts, and the teeth won't be precisely spaced either. But as I mentioned before, they don't really need to be.
04:14 Providing I don't introduce any gross errors, It's close enough for the final result, and by accepting a small error, I can move through this part of the process very quickly.
05:14 The total amount of metal to be removed, is determined by the difference between the pilot diameter and the diameter of the circle that just encloses the final square. That metal removal must now be shared across all of the teeth, so it determines how much I feed out before cutting each tooth, and that in turn ends up determining the broach depth of cut.
05:32 The diameter difference also gives an indication of how many teeth are required to keep the chip load manageable.
06:15 At this point all of the features of the broach have been formed, so it can now be quench hardened, and on this occasion I'm using the tray that I recently made for the current clock project.
07:07 In an industrial setting a broach is far more likely to be pulled through the work rather than pushed like this, and there's a real risk of fracture using an arbor press in this way, so be sure to take it carefully.
07:19 Make sure the broach is perfectly vertical before you push it through, and as always have your eye protection on. But even with all of the compromises, its still a great way to use home shop tools to quickly shape a precise square hole.
Making A Square Broach, by Clickspring.
It's not necessarily a common event, but when you need to make a square hole, it can be difficult to get a precise result. One of the best methods to achieve a professional cut is to use a custom made broach, so in this video I go through the process of making one from scratch.
________________________________________________________
A very special thank you to patron Dan Keen.
________________________________________________________
You can also help me make these videos by purchasing via the following Amazon Affiliate links:
Cameras used in this video:
Tools & Shop Products:
Abbreviated Transcript:
00:06 No matter what your style of metal working project might be, every now and then there's a need to form a precise square hole.
00:21 A pilot hole locates the exact position of the desired square, and then the broach is forced through the workpiece.
00:53 And that's because, all of the teeth prior to the last tooth collectively prepare the opening for the final tooth to set the dimension, so within reason, we can tolerate some small errors in those teeth, providing that the very last one is correct.
01:26 Its much too long and slender to be turned between centers, so I'll need to form the features by incrementally extending the work from a 4 jaw chuck. And the other key feature is the pilot diameter, which must be centered on the square, so I'm taking care to center the raw stock prior to forming that cylindrical shape.
01:48 I have the work reasonably well centered to begin with, so that when I position the dial indicator, the error that I see for each jaw is quite small I then use 2 chuck keys in opposition to each other, to move the work, so that the dial reads directly between the original 2 readings for both jaws.
02:13 Once its close, I move the zero reference to that point, so that becomes my target when I start to center the other two jaws. Once the work gets close to being centered, the errors start to sit nicely either side of that zero reference, and it gets easier to pull it into position.
02:53 But even doing this quickly, you can see that it will take a fair amount of time to do this for every cut, so there's a strong incentive to bypass this centering process if we can. For now though, the work is centered, so I can make a start on cutting that pilot diameter.
03:39 Next I'm using the first groove position to register the tool after extending the work, and then I'm using the hand wheels to advance the tool the required amount to form the next groove. Now inevitably I will have introduced a small eccentricity to each of these cuts, and the teeth won't be precisely spaced either. But as I mentioned before, they don't really need to be.
04:14 Providing I don't introduce any gross errors, It's close enough for the final result, and by accepting a small error, I can move through this part of the process very quickly.
05:14 The total amount of metal to be removed, is determined by the difference between the pilot diameter and the diameter of the circle that just encloses the final square. That metal removal must now be shared across all of the teeth, so it determines how much I feed out before cutting each tooth, and that in turn ends up determining the broach depth of cut.
05:32 The diameter difference also gives an indication of how many teeth are required to keep the chip load manageable.
06:15 At this point all of the features of the broach have been formed, so it can now be quench hardened, and on this occasion I'm using the tray that I recently made for the current clock project.
07:07 In an industrial setting a broach is far more likely to be pulled through the work rather than pushed like this, and there's a real risk of fracture using an arbor press in this way, so be sure to take it carefully.
07:19 Make sure the broach is perfectly vertical before you push it through, and as always have your eye protection on. But even with all of the compromises, its still a great way to use home shop tools to quickly shape a precise square hole.
Making A Square Broach, by Clickspring.
Комментарии