filmov
tv
Primitive Technology: Wood Ash Cement 💟💟💟
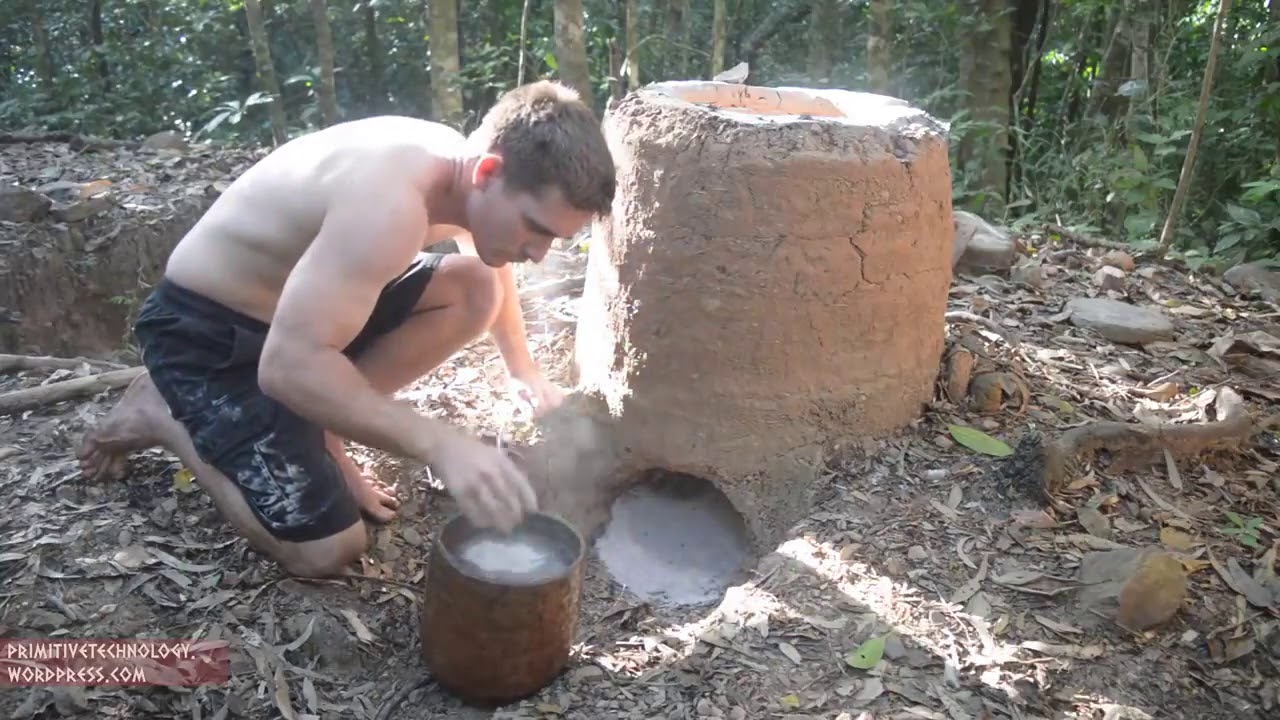
Показать описание
Primitive Technology: Wood Ash Cement - Creating wood ash cement from scratch
Follow Primitive Technology:
Watch More Primitive Technology:
I developed an experimental cement from made only from re-fired wood ash as its cementitious material. It was mixed with crushed terracotta as an aggregate and formed into a cube. The cement set hard after 3 days and did not dissolve in water after this period.
Process: First I burnt bark and leaves in a kiln at high temperatures to produce well burnt, mostly white wood ash. The ash was then mixed into water and stirred well. The excess water was poured off and the resulting paste was made into pellets and allowed to dry. A pellet was then re-heated in the forge until it glowed about orange hot. This was then taken out, cooled and dropped in a pot of water. The pellet dissolved and boiled due to a chemical reaction with the water. The paste was stirred and crushed terracotta (old tiles from previous projects) was added and mixed to form a mouldable mortar. This was formed into a cube and allowed to set for three days (in the video, a cube made exactly the same way 3 days previously was used due to time constraints). The resultant cube was strong and made a slight ringing sound when tapped with a finger nail. It was placed in water for 24 hours to simulate a very heavy rain event and did not dissolve or release residues into the water.
My current theory: The main component of wood ash consists of calcium in some form (e.g. calcium carbonate, calcium oxide). This can be up to 45% from my research. Calcium is in higher concentration in the bark and leaves of a tree. When the ash is mixed with water, the soluble component of wood ash (10% pot ash) dissolves into the water. But seeing that it does nothing for the cementing process, it is drained off leaving the insoluble calcium (and other components) in the paste. Doing this probably raises the relative percentage of calcium in the paste to about 50% or more. Most of the other 50 % consists of silica and alumina whi
Follow Primitive Technology:
Watch More Primitive Technology:
I developed an experimental cement from made only from re-fired wood ash as its cementitious material. It was mixed with crushed terracotta as an aggregate and formed into a cube. The cement set hard after 3 days and did not dissolve in water after this period.
Process: First I burnt bark and leaves in a kiln at high temperatures to produce well burnt, mostly white wood ash. The ash was then mixed into water and stirred well. The excess water was poured off and the resulting paste was made into pellets and allowed to dry. A pellet was then re-heated in the forge until it glowed about orange hot. This was then taken out, cooled and dropped in a pot of water. The pellet dissolved and boiled due to a chemical reaction with the water. The paste was stirred and crushed terracotta (old tiles from previous projects) was added and mixed to form a mouldable mortar. This was formed into a cube and allowed to set for three days (in the video, a cube made exactly the same way 3 days previously was used due to time constraints). The resultant cube was strong and made a slight ringing sound when tapped with a finger nail. It was placed in water for 24 hours to simulate a very heavy rain event and did not dissolve or release residues into the water.
My current theory: The main component of wood ash consists of calcium in some form (e.g. calcium carbonate, calcium oxide). This can be up to 45% from my research. Calcium is in higher concentration in the bark and leaves of a tree. When the ash is mixed with water, the soluble component of wood ash (10% pot ash) dissolves into the water. But seeing that it does nothing for the cementing process, it is drained off leaving the insoluble calcium (and other components) in the paste. Doing this probably raises the relative percentage of calcium in the paste to about 50% or more. Most of the other 50 % consists of silica and alumina whi