filmov
tv
Machining 304 Stainless Steel: Feeds & Speeds WW167
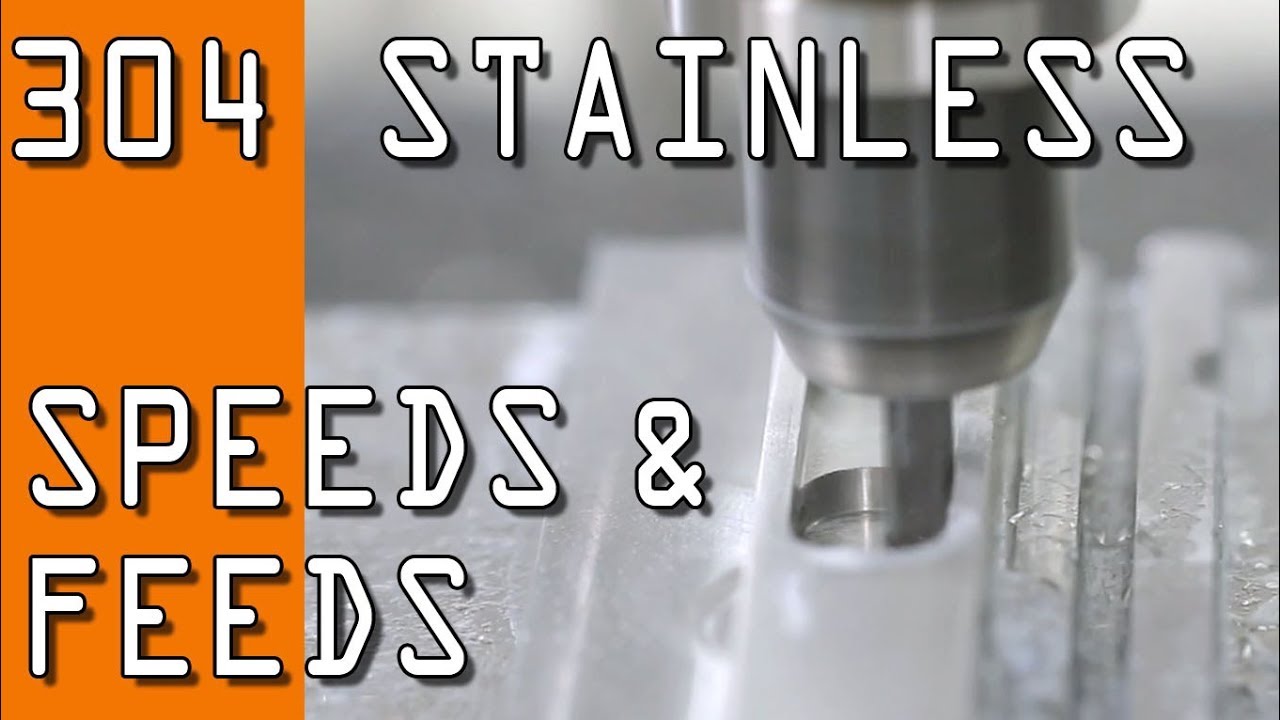
Показать описание
Let's experiment with Feeds & Speeds to CNC Machine 304 Stainless Steel, including outside profiles, internal pockets and drilling 304 Stainless!
~~~~~~~~~~~~~~~~~~~~~~~~~~~~
Links for this video
CREDIT:
~~~~~~~~~~~~~~~~~~~~~~~~~~~~
Reach us / CNC Info:
Manufacturing Entrepreneurship Resources:
~~~~~~~~~~~~~~~~~~~~~~~~~~~~
~~~~~~~~~~~~~~~~~~~~~~~~~~~~
Links for this video
CREDIT:
~~~~~~~~~~~~~~~~~~~~~~~~~~~~
Reach us / CNC Info:
Manufacturing Entrepreneurship Resources:
~~~~~~~~~~~~~~~~~~~~~~~~~~~~
Machining 304 Stainless Steel: Feeds & Speeds WW167
STEEL, STAINLESS STEEL and TITANIUM, 6 flute end mill!!
DiPosFeed, Grade 7035 Insert - Stainless
AnoleX CNC 3020 Evo 304 stainless steel sheet cutting!
Ultra-Tool Seven Flute 377 Series milling 304 Stainless Steel
NEW End Mill Cuts Through Stainless Steel Like BUTTER
Milling AISI 304 / EN 1.4301
Stainless Steel (304 vs 316) for CNC machining
The feed mixer adopts pure copper motor propeller blades, which provide stronger power.
Finishing 304 stainless steel with YG2025 CVD coated grade #yg1cuttingtools
Fictiv | 303/304L/316L Stainless Steel CNC Material
Dormer Pramet's New face milling range for stainless steel.
Milling 304 Stainless with a Carbide End Mill | Speeds and Feeds Tool Test
303 & 304 Stainless Steel Lathe Speeds & Feeds! WW204
How to Face & Engrave 304 Stainless Steel | WW251
50mm high feed making light work of 304 stainless steel || Promac Precision Ltd
SS303 SS304 CNC Machining Auger Milling Screw Shaft 40mm Feed Screw
How to efficiency machining 304 stainless steel
How to mill 304 Stainless Steel - Mastercam 2020
Roughing and finishing 304 stainless steel with YG2025 CVD coated grade. #yg1cuttingtools
HOW TO: Drill Stainless Steel - 6 Tips
Machining 304 Stainless Steel. Korloy Carbide Insert & Tool
304 Stainless Steel CNC
Cnc milling 304 stainless steel
Комментарии