filmov
tv
Machinist's Minutes: Gibs and Ways
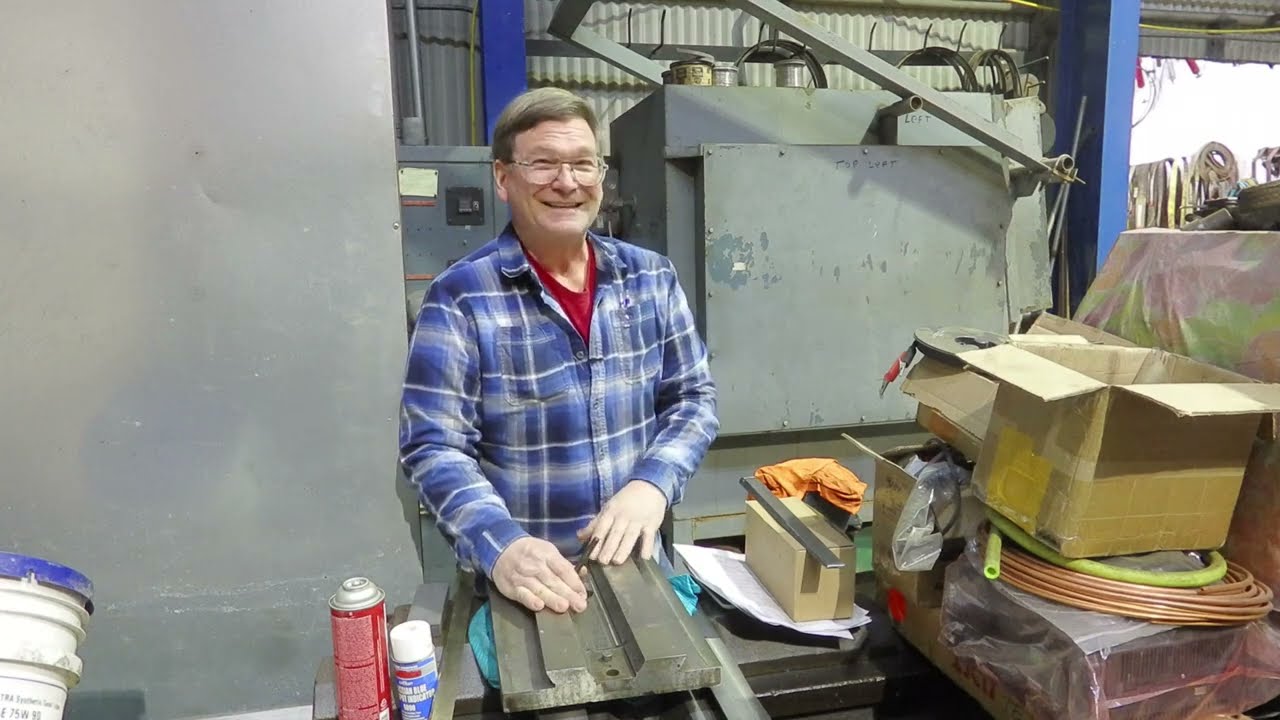
Показать описание
Understanding these is vital to understanding how to address slop in your machines.
Machinist's Minutes: Gibs and Ways
Machinist's Minutes: Gib head keys and how to install/remove them
Machinist's Minute: Gibs
Machinist's Minute: Extending the Life of Your Gibs
Seig mini lathe rebuild #34 machining brass gibs Part A
Machinist's Minute(s): The Best Engineer to Work With
Machinist's Minute(s): The Machinist's Eye
Machinist's Minute: Gib head keys
Adjusting the GIBS 1 of 2
Machinist's Minute: The Fourth Axis on Bridgeport Style Mills
Machinist's Minute: Personal Jobs
Machinist's Minute: Types of Mills
Machinist's Minute: Sunnen Hones Are Useful in a Job Shop!
Machinist's Minute: You're expected to know EVERYTHING.
If you've ever used a Machinist's level you'll understand. #machinist #maths #dw0rtor...
Machinist's Minutes: CNC's vs Manual Machining
Machinist's Minute: A tough little mic
Machinist's Minute: Make sure to snug your tooling up!
Machinist's Minute: On 'Price Gouging'
Machinist's Minute: Portable tool precision
12 Machine Gib adjustment
Machinist's Minute: Lifting to within 0.0001' with precision mics
Machinist's Minute: Field Work at Placer Mines
Machinist's Minute: Dialing in a threaded part
Комментарии