filmov
tv
Toolmakers Vice Build Part 3 - Grinding and Finishing
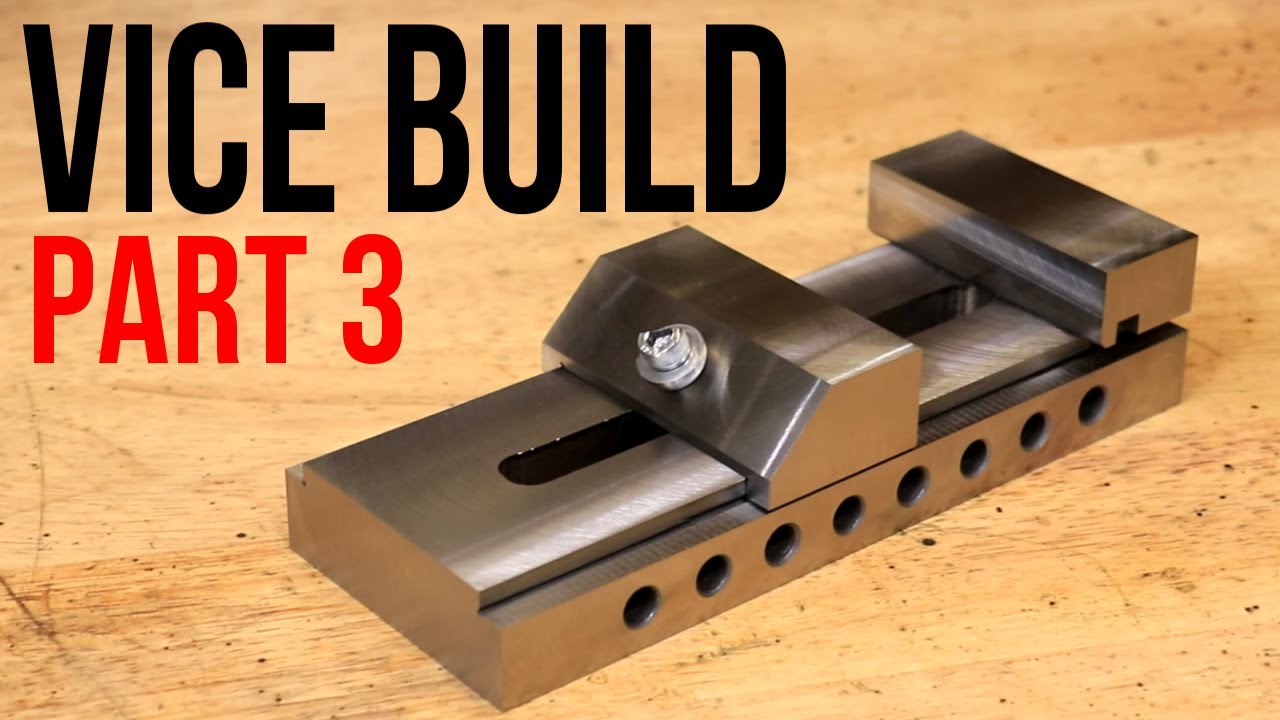
Показать описание
Whilst I got good results from this set up, I strongly recommend against doing this machining process on a mill.
G'day everyone,
welcome back to part 3 of making a toolmaker vice for the milling machine. in the previous video I case hardened and tempered it to 55-60 HRC. in this video I intend to grind it down to final dimension and test it.
Without access to a surface grinder, I decided to use a grinding stone mounted in the mill to grind the part. This was not an easy, nor pleasant process which took a lot of trial and error to get right. whilst I do not recommend this method, I was able to get it to work, with hopefully minimal long term consequences to the mill.
cheers
G'day everyone,
welcome back to part 3 of making a toolmaker vice for the milling machine. in the previous video I case hardened and tempered it to 55-60 HRC. in this video I intend to grind it down to final dimension and test it.
Without access to a surface grinder, I decided to use a grinding stone mounted in the mill to grind the part. This was not an easy, nor pleasant process which took a lot of trial and error to get right. whilst I do not recommend this method, I was able to get it to work, with hopefully minimal long term consequences to the mill.
cheers
Toolmakers Vice Build Part 3 - Grinding and Finishing
WIYB Toolmakers Collaboration Machinist Vice Part 3
WIYB TMC Machinist Vise Part 3
WIYB Vice part #3
Mr Pete's Tool Makers Vise Part 3 of 4
Making A Toolmakers Vice From Scrap
Emmert 6A Toolmakers Vise Restoration - Part 3: Making Copper Soft Jaws
Making A Toolmakers Mill Vise - Machining The Vise (Part 1)
#toolmakers vise#assembly #cleaning #WD 40 #shorts
Case Hardening And Heat Treatment - Making A Toolmakers Mill Vice (Part 2)
Make Toolmakers Screwless Vise from scrap - Part 1 milling all the parts.
TIPS #350 pt 1 tubalcain MAKES A TOOLMAKER'S VISE
Home Built Vise Part 3: Making A Core Box for the Castings
Making a Sine Vise for Grinding a jib 18 inch
The Toolmakers Vise - It's Not What You Think - Rob's Garage
WIYB TMC Machinist Vise Part 1
Very good improvement for milling machine vice
Restoration of large vices for a milling machine part 1
Easy clamping, orcan precision Machine vise for milling , vmc #machining #viral #shorts
RHS VICE678-1 | WEDM Stainless Steel Tool Maker vise clamping 100mm
Testing my DIY Milling Vise Clamps
Mini mill precision vise #shorts
surface grinder machine vice clamp block face on grinding on work #surfacegrinder #machine
DIY - A Milling VISE
Комментарии