filmov
tv
Robotic Bartender Powered by ClearCore - Teknic's Industrial I/O & Motion Controller
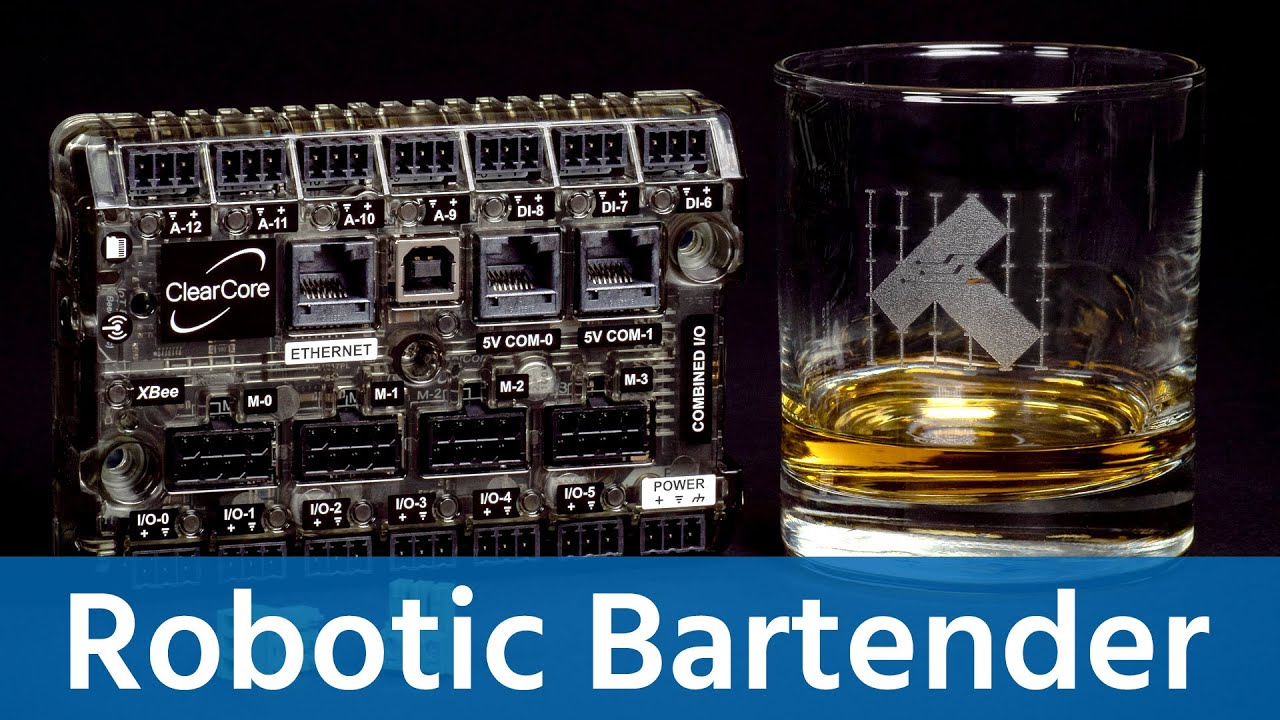
Показать описание
ClearCore can control 4 axes of servo or stepper motion; has software-configurable, analog and digital I/O (directly 24 volt compatible); multiple serial ports; Ethernet; and a 32-bit floating point CPU (and more) for only $99. ClearCore’s C++ motion and I/O library makes programming easy (and the source code is all available as a free download).
If you really want easy programming, download the free (optional) Arduino wrapper library and you can program ClearCore just like an Arduino (a turbocharged, industrial Arduino).
Teknic wants your feedback. Like this video? Give it a thumbs up! Be sure to comment with any questions about motion control and let us know what you did or did not like about the video.
For more information on Teknic ClearPath servos, subscribe to our channel and visit Teknic's website.
Robotic Bartender Powered by ClearCore - Teknic's Industrial I/O & Motion Controller
Bartender Robot
Robot bartender for the event and entertainment gastronomy
Cocktail Made By Robot Bartender
Robot bartender mixes it up
Robotic Bartender [UPGRADED]
World Premiere of ShotBot 2- Robotic Bartender and Drinking Game Entertainment Platform
Dragos' Robotic Bartender Using Industrial Controller Systems (ICS)
Your Next Bartender Might Be A Robotic Vending Machine | Strictly Robots
Robot Bartender...wow
robot bartender arduino diy , automatic bar
Robot Bartender Makes a Stiff Drink
Fetch Grasping - Robotic Bartender
Robotic bartender serves up mixed drinks
Robotic bartenders
Robotic bartender
Teknic ClearCore Unboxing, Blink and UDP
Robot barman . Automatic cocktail dispenser. Arduino drink robot..
Automated Bartender for Restaurants - Somabar
Automatic Bartender
What'll It Be? Robot Bartender 'Barney' Can Mix Dozens Of Cocktails, Tell Bad Jokes
Robot Drink Bar-A Robot serves you 😄😄 5G+Mobile Payment
Homemade Automated Cocktail Bar using Arduino
Bartender part 33(3)
Комментарии