filmov
tv
Vanner takes the L on repairability
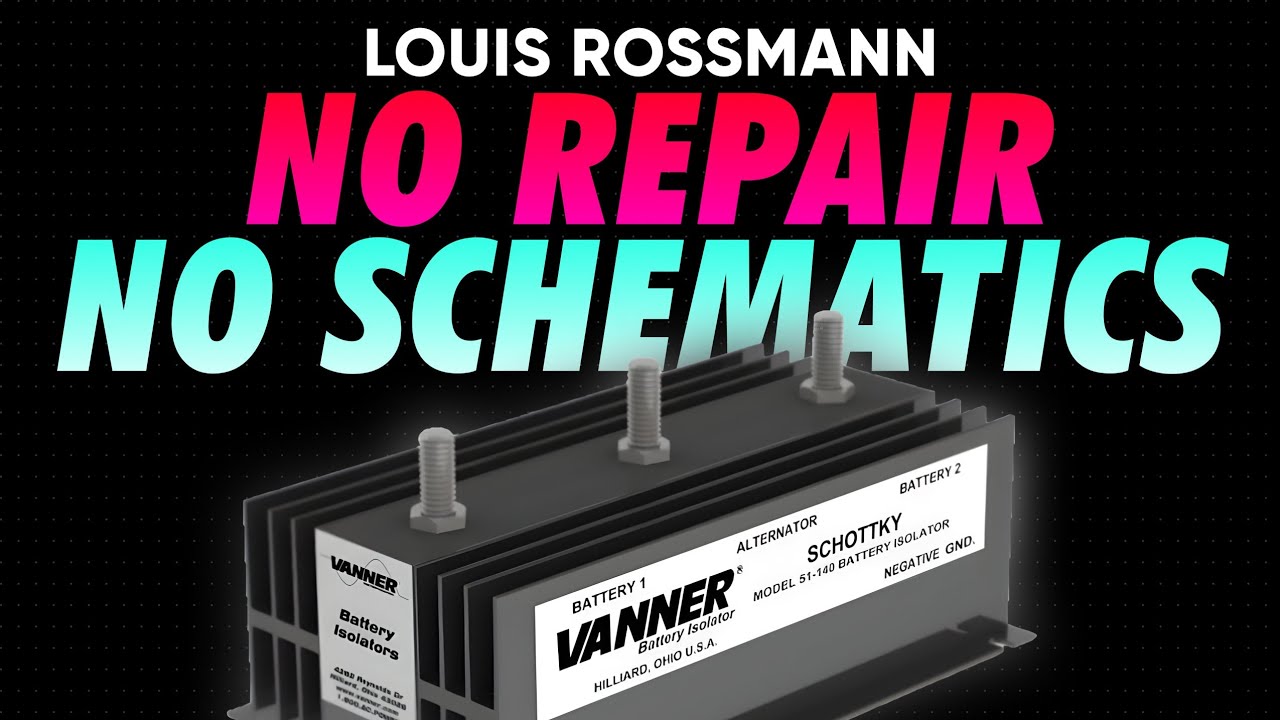
Показать описание
👉 LEARN HOW TO DO THIS:
👉 CHIPS & COMPONENTS:
👉 TOOLS USED:
✓ Soldering Irons:
✓ CHEAP HAKKO ALTERNATIVES:
✓ Preferred Soldering Tips
✓ Microscopes:
✓ Soldering/Repair Supplies:
✓ Diagnostic tools:
✓ Ultrasonic Cleaning:
✓ Desk supplies:
✓ Screwdrivers:
✓ RECORDING EQUIPMENT:
👉 Affiliate:
👉 Leave a tip for us via cryptocurrency if we've helped you out:
› Bitcoin: 1EaEv8DBeFfg6fE6BimEmvEFbYLkhpcvhj
› Bitcoin Cash: qzwtptwa8h0wjjawr5fsm0ku8kf40amgqgm6lx4jxh
› Dash: XwQpZuvMvU44JT7C7Uh6xHvkSadzJw9fMN
› Dogecoin: DKetsoCvwa2hF29ssgUA4Wz4hxT4kj3KLU
› Ethereum: 0x6f6870feb48f08388ee345cf0261e2f03d2fa310
› Ethereum classic: 0x671bfd61ba87edf6365c97cea33d66ba73645510
› Litecoin: LWnbTTAjojZQt68ihFJFgQq3cYHUsTcyd7
› Verge: DFumZ5sMhi3JktLQpsTVtV9xUt3zKDrcZV
› Zcash: t1Ko3FkphQYoQroQc8k2DVk4WKMAbmNR8PH
› Zcoin: a8QdvArHmdRYe1MjiqtP6jDNe6Z4JgnRKZ
Комментарии