filmov
tv
Pattern Making for the Foundry - The Basics you NEED to Know!
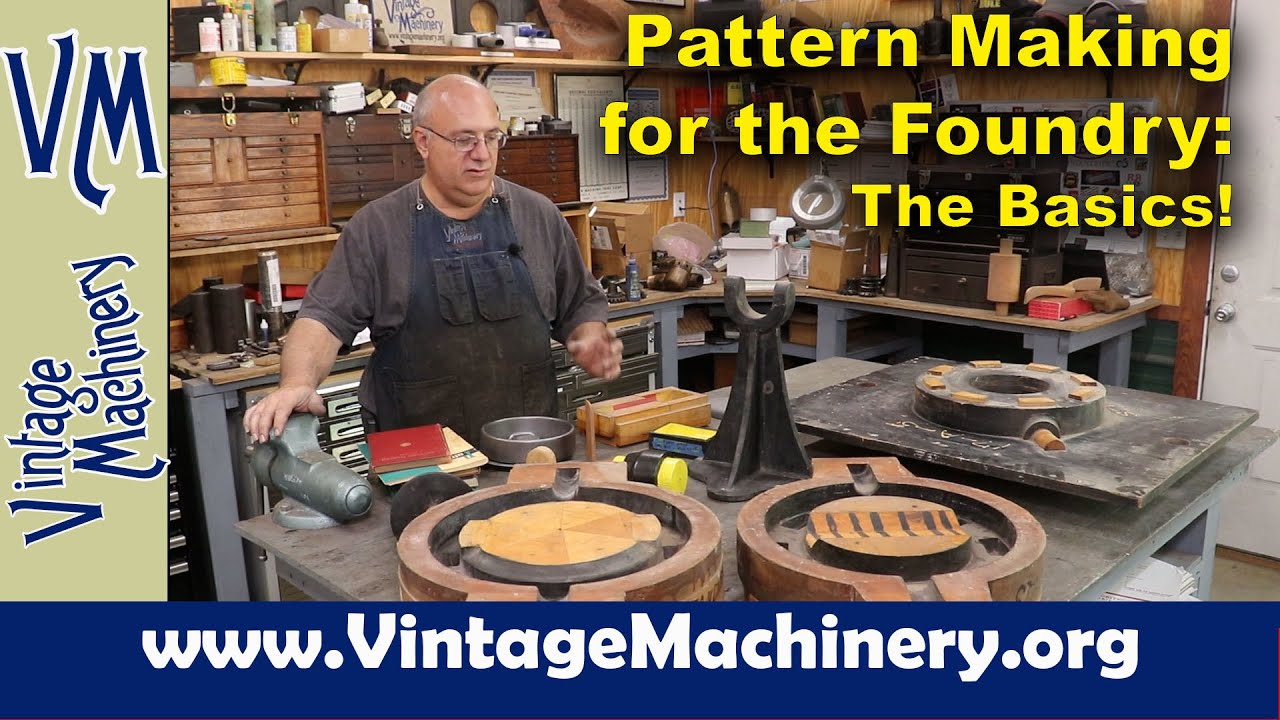
Показать описание
Some of the basics you need to know if you are going to make a pattern to have cast in metal at a foundry along with examples of patterns that I have in my collection made both by myself as well as professional pattern makers. Patterns need:
1 - Draft
2 - No sharp Corners - radiuses and fillets
3 - Scaled up in size to account for Shrink
4 - Be extremely smooth
Check out some molding videos at Windy Hill Foundry:
Make a one time donation to VintageMachinery via PayPal:
Sponsored by:
American Rotary Phase Converters
Use checkout code "Vintage10" for a 10% discount on all AD, ADX and AI converters!
1 - Draft
2 - No sharp Corners - radiuses and fillets
3 - Scaled up in size to account for Shrink
4 - Be extremely smooth
Check out some molding videos at Windy Hill Foundry:
Make a one time donation to VintageMachinery via PayPal:
Sponsored by:
American Rotary Phase Converters
Use checkout code "Vintage10" for a 10% discount on all AD, ADX and AI converters!
Pattern Making for the Foundry - The Basics you NEED to Know!
Foundry Pattern Making for Brass Casting
Foundry Pattern Making from Parts
DIMENSIONING FOUNDRY PATTERNS
FOUNDRY PATTERN MAKING NEW 19 AUGUST 2020
SIMPLE PATTERN MAKING AND POURING THE FIRST PIECE
Foundry Pattern Making: atlas compound slides #3
FOUNDRY PATTERNMAKING - Fillets 664 pt 1 tubalcain
Capgemini Written Exam Updated Pattern | Essay Writing OR Verbal Ability? Capgemini Preparation 2025
Lanhai pattern making - Foundry casting
Wood Pattern Making Process #1
pattern Making for foundry wooden
Foundry pattern modification
Foundry Exercise | Mechanical Engineering workshop
pattern Making for foundry wooden Aluminium
Foundry Pattern Making
DJJ2032 (FOUNDRY : PATTERN MAKING)
Split piece pattern
pattern Making for foundry
pattern making for foundry
Building a pattern to cast a diesel engine cylinder head #foundry #patternmaking #machining
Innovations in Wooden Foundry Mold and Pattern Making with the Rhino CNC Router-video
Wood or Aluminum mold pattern making for valve foundry casting use
FOUNDRY PATTERNMAKING - Fillets 665 pt 2 tubalcain
Комментарии